Understanding Underfill Epoxy in BGA Applications
Understanding Underfill Epoxy in BGA Applications
Introduction to BGA and Underfill Epoxy
Ball Grid Array (BGA) is a type of surface-mount packaging used for integrated circuits. It offers several advantages over traditional packages, including better thermal and electrical performance, higher pin density, and smaller package size. However, the reliability of BGA packages can be compromised due to thermal and mechanical stresses during operation. Underfill epoxy is used to address these issues.
Underfill epoxy is crucial in the electronics industry, particularly in BGA applications. It is applied between the BGA chip and the substrate to fill the gaps and provide mechanical support. This article delves into the significance of underfill epoxy in BGA, its types, application processes, benefits, and challenges.
The Importance of Underfill Epoxy in BGA
Enhancing Mechanical Reliability
BGA packages are susceptible to thermal cycling, which causes materials to expand and contract. This thermal mismatch between the BGA chip and the substrate can lead to solder joint failures. Underfill epoxy helps mitigate these stresses by providing a cushion that absorbs and distributes the mechanical strain, thereby enhancing the mechanical reliability of the BGA package.
Improving Thermal Management
Underfill epoxy plays a vital role in improving the thermal performance of BGA packages. Filling the gaps between the chip and the substrate enhances thermal conductivity and helps dissipate heat more effectively. This is particularly important in high-performance applications where efficient heat management is critical to ensure the longevity and reliability of the device.
Preventing Moisture and Contaminant Ingress
Another critical function of underfill epoxy is to protect the BGA package from environmental factors such as moisture and contaminants. By creating an airtight seal around the chip, underfilled epoxy prevents the ingress of moisture and other harmful substances that can lead to corrosion and electrical failures.
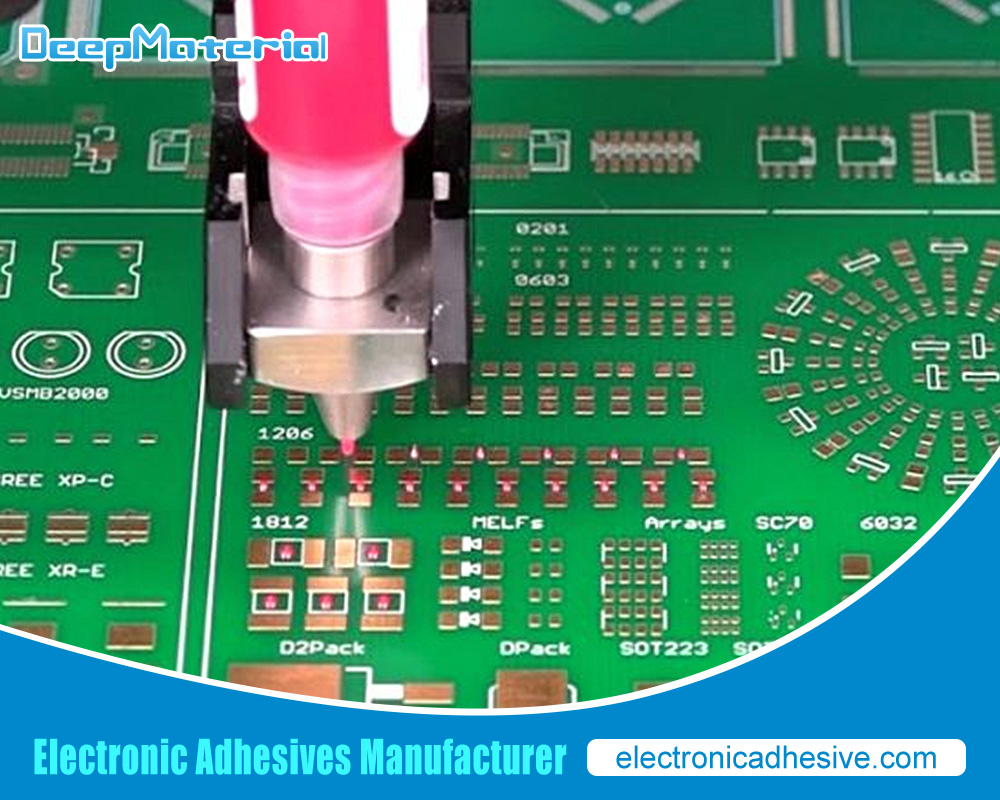
Types of Underfill Epoxy
Capillary Flow Underfill
Capillary flow underfill is the most common type used in BGA applications. It is applied in a liquid state and flows into the gaps between the chip and the substrate through capillary action. Once the epoxy is entirely dispensed, it is cured to form a solid, protective layer. This underfill type is ideal for high-reliability applications and is widely used in consumer electronics, automotive, and aerospace industries.
No-Flow Underfill
No-flow underfill is applied to the substrate before the BGA chip is placed. The underfill material melts and fills the gaps during reflow, simultaneously forming solder joints. This method is advantageous in high-throughput manufacturing environments as it reduces the processing steps and improves production efficiency.
Molded Underfill
A molded underfill is a pre-applied underfill molded to the shape of the BGA package. This method is commonly used in advanced packaging technologies such as wafer-level packages (WLP) and system-in-package (SiP). Molded underfill offers excellent mechanical protection and is suitable for applications where space constraints and high performance are critical.
Corner Bond and Edge Bond Underfill
Corner bond and edge bond underfills are applied only to the corners or edges of the BGA package. These types provide partial mechanical reinforcement and are often used in applications where full underfill is not required. They balance reliability and cost, making them suitable for consumer electronics and industrial applications.
Application Processes for Underfill Epoxy
Dispensing
Dispensing is a critical step in the underfill process. The epoxy is dispensed onto the substrate using precision dispensing equipment. The amount and placement of the epoxy must be carefully controlled to ensure complete coverage and avoid voids. Modern dispensing systems use automated equipment with vision systems to achieve high accuracy and consistency.
Capillary Action
After dispensing, the underfilled epoxy flows into the gaps between the BGA chip and the substrate through capillary action. The flow dynamics depend on the epoxy’s viscosity, the gap size, and the surface tension. Optimizing these parameters is essential to achieving complete and uniform filling.
Curing
Once the underfill epoxy is dispensed and has flowed into place, it must be cured to form a solid, protective layer. Curing is typically done through thermal processes, where the assembly is heated to a specific temperature for a set duration. Some advanced underfill materials offer UV or dual-curing mechanisms to enhance processing flexibility and efficiency.
Post-Curing Inspection
After curing, the BGA assembly must be inspected to ensure the underfill epoxy has been correctly applied and cured. Non-destructive inspection methods such as X-ray imaging and acoustic microscopy are commonly used to detect voids, delamination, and other defects that could compromise the package’s reliability.
Benefits of Using Underfill Epoxy in BGA
Enhanced Reliability
The primary benefit of using underfill epoxy in BGA applications is the significant enhancement of mechanical and thermal reliability. By mitigating thermal and mechanical stresses, underfill epoxy helps prevent solder joint failures and extends the operational life.
Improved Performance
Underfill epoxy improves the overall performance of BGA packages by enhancing thermal management and protecting against environmental factors. This is particularly important in high-performance applications where reliable operation under challenging conditions is crucial.
Cost-Effectiveness
While the initial cost of applying underfilled epoxy may be higher, the long-term benefits, such as reduced failure rates and extended device lifespan, result in overall cost savings. The improved reliability and performance also translate to fewer warranty claims and customer returns.
Design Flexibility
The use of underfill epoxy allows for greater design flexibility in BGA packages. It enables more diminutive and densely packed packages, essential for modern electronic devices. This flexibility helps designers meet the ever-increasing demands for miniaturization and higher performance in consumer electronics, automotive, and industrial applications.
Challenges and Considerations
Material Selection
Choosing the right underfill epoxy material ensures optimal performance and reliability. Factors such as viscosity, curing time, thermal conductivity, and adhesion properties must be carefully considered. The material must also be compatible with the other components and processes used in the assembly.
Process Control
Achieving consistent and reliable underfill applications requires precise process control. Factors such as dispensing accuracy, flow dynamics, and curing conditions must be tightly controlled to avoid defects such as voids, delamination, and incomplete coverage. Implementing robust process control measures is essential to ensure high-quality results.
Inspection and Testing
Thorough inspection and testing are crucial to ensure the underfill epoxy has been correctly applied and cured. Non-destructive testing methods such as X-ray imaging and acoustic microscopy are commonly used to detect defects that could compromise the reliability of the BGA package. Implementing comprehensive inspection and testing protocols helps ensure the highest quality standards are met.
Environmental Impact
Like many other materials in the electronics industry, underfill epoxy raises concerns about environmental impact and sustainability. Manufacturers must consider the ecological implications of their material choices and processes and strive to minimize waste and reduce the use of hazardous substances. Developing and adopting eco-friendly materials and methods is an ongoing challenge in the industry.
Future Trends and Innovations
Advanced Materials
Ongoing research and development in underfill epoxy materials are focused on enhancing performance and sustainability. New materials with improved thermal conductivity, lower viscosity, and faster curing times are being developed to meet the evolving demands of advanced electronic applications. Additionally, there is a growing emphasis on developing environmentally friendly and sustainable materials.
Automation and Precision
Advancements in automation and precision dispensing technologies enable more accurate and efficient underfill application processes. Automated systems with advanced vision and control capabilities are helping manufacturers achieve higher consistency and throughput, reduce the risk of defects, and improve overall quality.
Integration with Advanced Packaging Technologies
As electronic devices evolve, there is a growing need for advanced packaging technologies such as wafer-level packages (WLP), system-in-package (SiP), and 3D packaging. Underfill epoxy is critical in these advanced packaging solutions, providing mechanical and thermal support. Ongoing innovations in underfill materials and processes are essential to meet the demands of these cutting-edge technologies.
Sustainability Initiatives
The electronics industry is increasingly focusing on sustainability and environmental responsibility. Efforts are being made to develop eco-friendly underfill epoxy materials and processes that minimize environmental impact. These initiatives include reducing the use of hazardous substances, improving recyclability, and adopting greener manufacturing practices.
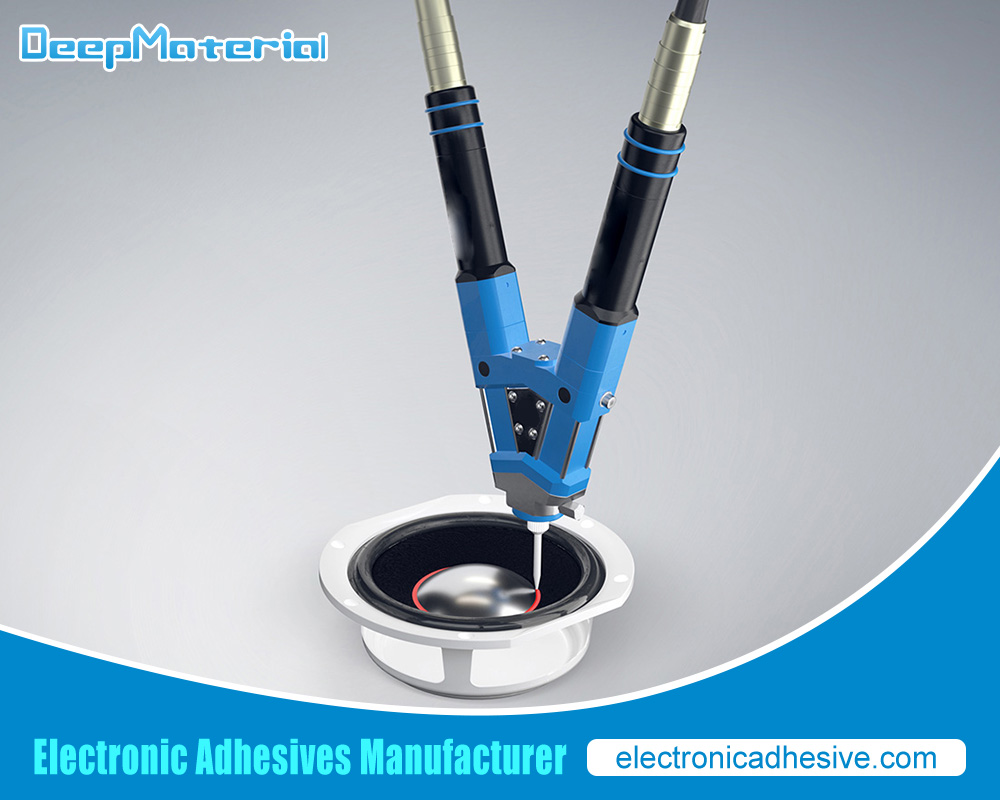
Conclusion
Underfill epoxy is essential in BGA applications, providing critical mechanical support, thermal management, and protection against environmental factors. Its use significantly enhances the reliability and performance of BGA packages, making it indispensable in modern electronics. Despite the challenges and considerations, ongoing materials and process advancements are driving underfill epoxy technology improvements. As the industry continues to evolve, the role of underfill epoxy will remain vital in meeting the demands of advanced electronic applications.
For more about understanding underfill epoxy in BGA applications, you can pay a visit to DeepMaterial at https://www.electronicadhesive.com/ for more info.