Understanding The Chemistry Behind Low Temperature Epoxy Adhesive
Understanding The Chemistry Behind Low Temperature Epoxy Adhesive
Epoxy adhesives have been rocking the industrial world for ages with their killer strength, durability, and versatility. But here’s the kicker: traditional epoxies need a bit of a heat boost to cure and bond just right. Recently, the spotlight’s turned to low-temperature epoxy adhesives, and let me tell you, they’re starting to steal the show with their cool features, especially handy in a slew of applications.
Low-temperature epoxy adhesives are like the special ops of the epoxy world. They get the job done at much chillier temps than their old-school siblings. These adhesives are perfect when cranking up the heat isn’t an option or it’s just plain undesirable—think construction sites, cars, and even spaceships. Getting a grip on the science behind these adhesives is key to making the most of their abilities and ensuring they stick it out where it counts.
The Basics of Epoxy Chemistry
Let’s break it down: epoxy resins are the heart of epoxy adhesives and are famous for their reactive epoxide group, also known as an oxirane ring. These resins come in various chemical flavors and properties, tailor-made to fit specific needs. The magic happens during the curing process, where the epoxide groups and a curing agent—a.k.a. a hardener or cross-linker—get cozy and react.
The curing agents are the unsung heroes here, playing a pivotal role in the final vibe of the cured material. Whether they’re amine-based, anhydride-based, or even catalytic, each type brings its own flair to the table, affecting everything from curing speed to the toughness and weather resistance of the adhesive. Picking the right curing agent is super crucial in concocting low-temperature epoxy adhesives because it’s what lets the adhesive do its thing without needing extra warmth.
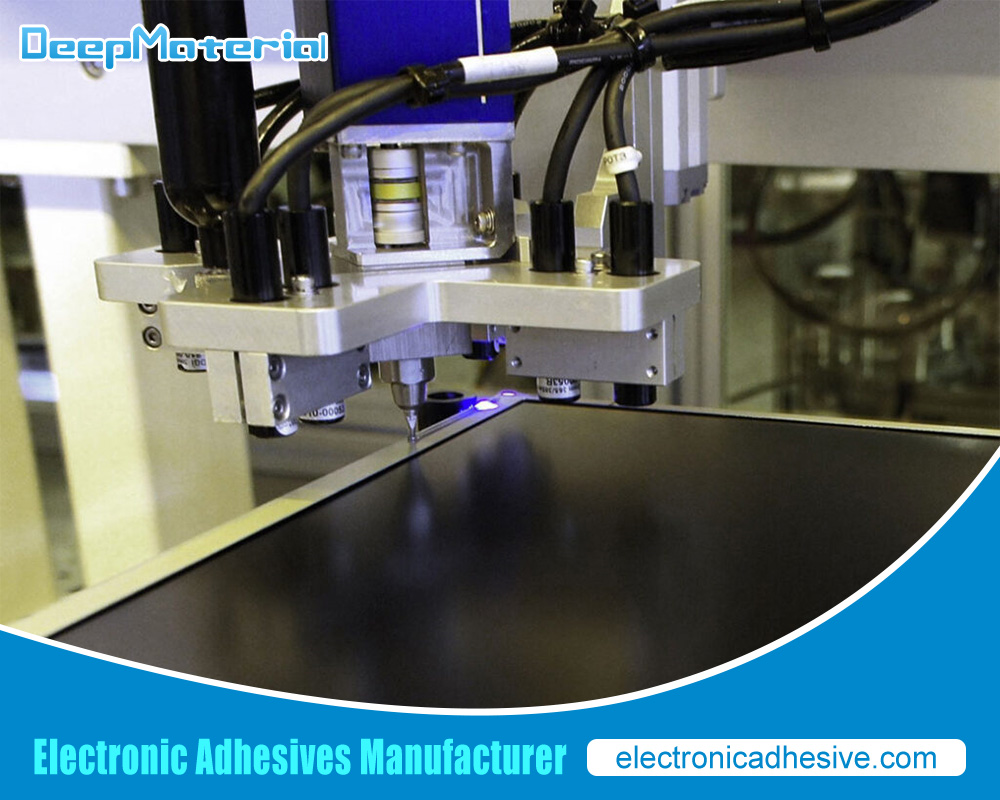
Curing Mechanisms of Epoxy Resins
Now, curing epoxy resins can go down a couple of ways, with thermal curing and room-temperature curing being the usual suspects. Thermal curing is all about bringing the heat, sparking those chemical reactions that turn the gooey resin into a tough, sturdy adhesive. On the flip side, room-temperature curing doesn’t need the heat wave; it leans on sneaky latent curing agents or nifty catalysts to kickstart the curing process right at comfy room temps.
Choosing between thermal and room-temperature curing is a big deal when developing low-temperature epoxy adhesives. Sometimes, you just can’t bring the heat, or it might wreck the materials you’re working with. That’s where room-temperature curing steps in, offering a more versatile and substrate-friendly option, especially when keeping things cool is part of the plan.
Factors Affecting the Curing Process
Let’s talk about what messes with the curing game of epoxy adhesives, especially those cool, low-temp ones! Temperature is the big boss here; it directly tweaks the speed of the chemical reactions that make the curing happen. Lower temperatures mean slower reaction times, so you might need longer for everything to set or a special curing agent to get that strong, snappy bond.
Now, don’t forget about other environmental party crashers like humidity and pressure. Humidity can change the speed of curing reactions, and pressure might mess with how the adhesive smooshes into the surfaces it’s bonding. Keeping these factors in check is key to making sure low-temp epoxies perform consistently and reliably.
Advantages of Low-Temperature Epoxy Adhesives
Diving into the perks, low-temperature epoxy adhesives are the new heroes in town, offering some great advantages. Their biggest bragging right is sticking things together brilliantly at lower temps. This is a game-changer when you can’t bring the heat—literally—or when the materials you’re working with throw a fit if they get too hot.
Also, these adhesives are quite the social butterflies, mingling with a broad range of materials, from mismatched substrates to the usual suspects. This makes them super handy in industries like construction, automotive, and aerospace. Thanks to their cool curing capabilities, they’re sparking all sorts of innovative designs and manufacturing tricks.
Applications of Low-Temperature Epoxy Adhesives
Speaking of where these adhesives strut their stuff, their unique talents are making waves in various fields. A standout role? Bonding different materials that usually wouldn’t get along, like metals, plastics, and composites. Low-temperature epoxies can bridge these gaps, ensuring strong, lasting bonds without the need for high heat.
In construction, these adhesives are popping up everywhere from sticking building parts together to fixing up concrete and laying down insulation. Their cool curing nature lets you plan projects more flexibly, without sweating over heat damage to delicate materials. Over in the automotive and aerospace arenas, they’re making it easier to assemble parts, patch up composite structures, and join things like metal and plastic without a meltdown.
Formulation Considerations for Low-Temperature Epoxies
When whipping up effective low-temperature epoxy adhesives, it’s all about nailing the recipe. Choosing the right epoxy resin and curing agent is where the magic starts, as these ingredients majorly affect how quickly the adhesive cures, its toughness, and how well it holds up against the elements.
Don’t forget about the extras! Adding flexibilizers, tougheners, fillers, and catalysts can really jazz up the performance of your low-temp epoxy adhesives. These additions are like spices in a stew, each one adding a little something special to enhance traits like impact resistance, thermal stability, and the ability to fill those pesky gaps.
Testing and Characterization of Low-Temperature Epoxy Adhesives
To make sure these adhesives stick it out, a thorough testing bash is a must. Mechanical tests like pulling, shearing, and peeling help us understand the strength and resilience under different stresses. Then there’s the heat check—using fancy techniques like differential scanning calorimetry (DSC) and thermogravimetric analysis (TGA) tells us about the adhesive’s curing behavior and how it handles the hot and cold.
But the real test is out in the wild—how does the adhesive hold up against moisture, chemicals, and the freeze-thaw cycle of the great outdoors? And most importantly, can it keep things stuck together for the long haul? Researchers and manufacturers are always on the ball, striving to dial up the performance and broaden the uses of these adhesives.
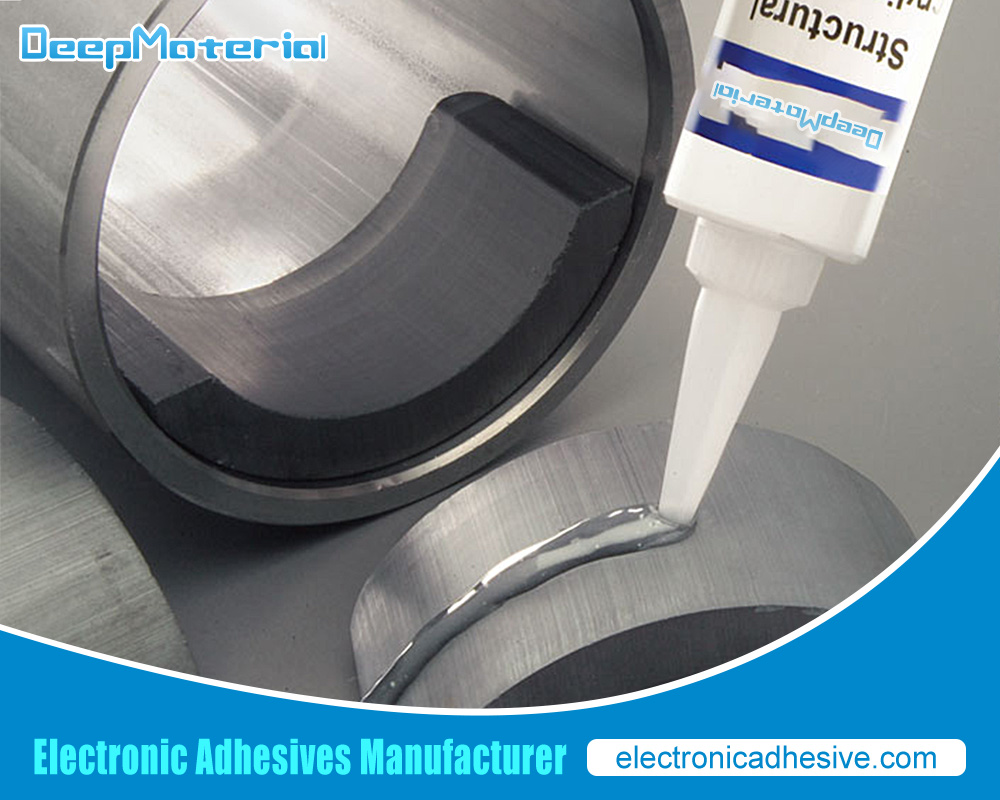
Emerging Trends and Future Developments
The world of low-temperature epoxy adhesives isn’t standing still—it’s always moving and shaking with new ideas and innovations. One hot topic? Crafting adhesives that set even in the chilliest conditions or speed up the curing without losing quality.
And let’s not forget about Mother Nature! There’s a hefty push towards greener, more planet-friendly adhesives. Think bio-based or recycled materials and new ways to cure that cut down on energy guzzle. As the thirst for versatile, top-notch adhesives grows across industries, the future looks bright (and sticky) for low-temperature epoxy adhesives.
With cutting-edge research and some clever chemistry, these adhesives are set to revolutionize product design, refine manufacturing, and boost sustainability in the biz.
For more about understanding the chemistry behind low temperature epoxy adhesive, you can pay a visit to DeepMaterial at https://www.electronicadhesive.com/ for more info.