Understanding Electric Motor Epoxy Adhesive: Uses, Benefits, and Application Techniques
Understanding Electric Motor Epoxy Adhesive: Uses, Benefits, and Application Techniques
Electric motors are vital in various industrial and consumer applications, powering everything from household appliances to heavy machinery. Ensuring their reliability and longevity is crucial, and one of the critical materials that contribute to this is epoxy adhesive. Specifically designed for electric motors, epoxy adhesive plays a significant role in bonding, sealing, and insulating. This article delves into electric motor epoxy adhesive’s uses, benefits, and application techniques.
What is an Electric Motor Epoxy Adhesive?
Electric motor epoxy adhesive is a specialized type of epoxy resin used in the manufacturing and maintenance of electric motors. Epoxy adhesives are known for their strong bonding capabilities, chemical resistance, and excellent electrical insulation properties. These features make them ideal for electric motors where reliability and performance are paramount.
Composition and Properties
Epoxy adhesives comprise two main components: the resin and the hardener. When mixed, these components undergo a chemical reaction that results in a rigid, durable bond. For electric motor applications, the epoxy adhesive must have specific properties:
- Electrical Insulation:It should have high dielectric strength to prevent electrical failures.
- Thermal Conductivity:Adequate thermal conductivity helps dissipate heat generated within the motor.
- Chemical Resistance:It should resist oils, solvents, and other chemicals typically encountered in motor environments.
- Mechanical Strength:High tensile and shear strength are necessary to withstand operational stresses.
Uses of Electric Motor Epoxy Adhesive
Electric motor epoxy adhesive is used in various motor manufacturing and repair stages. Its applications can be broadly categorized into bonding, sealing, and insulating.
Bonding
Epoxy adhesives are widely used to bond components within electric motors. These include:
- Stator and Rotor Assembly:The adhesive ensures a strong bond between the stator and rotor components, maintaining alignment and operational integrity.
- Magnet Bonding:Permanent magnets in brushless motors are bonded using epoxy adhesives, ensuring they remain securely in place during operation.
- Component Fixation:Various motor parts, such as windings and insulation materials, are fixed using epoxy adhesives to prevent movement and vibrations.
Sealing
Epoxy adhesives seal components to protect them from environmental factors and contaminants.
- End Bell Sealing:End bells are sealed with epoxy to prevent the ingress of dust, moisture, and other contaminants.
- Junction Boxes:Electrical connections and junction boxes within the motor are sealed to protect against corrosion and short circuits.
Insulating
The electrical insulation properties of epoxy adhesives make them ideal for insulating components and preventing electrical failures.
- Coil Insulation:Motor windings and coils are often coated with epoxy to enhance insulation and prevent short circuits.
- Slot Insulation:Slots housing the windings are insulated with epoxy to ensure electrical isolation.
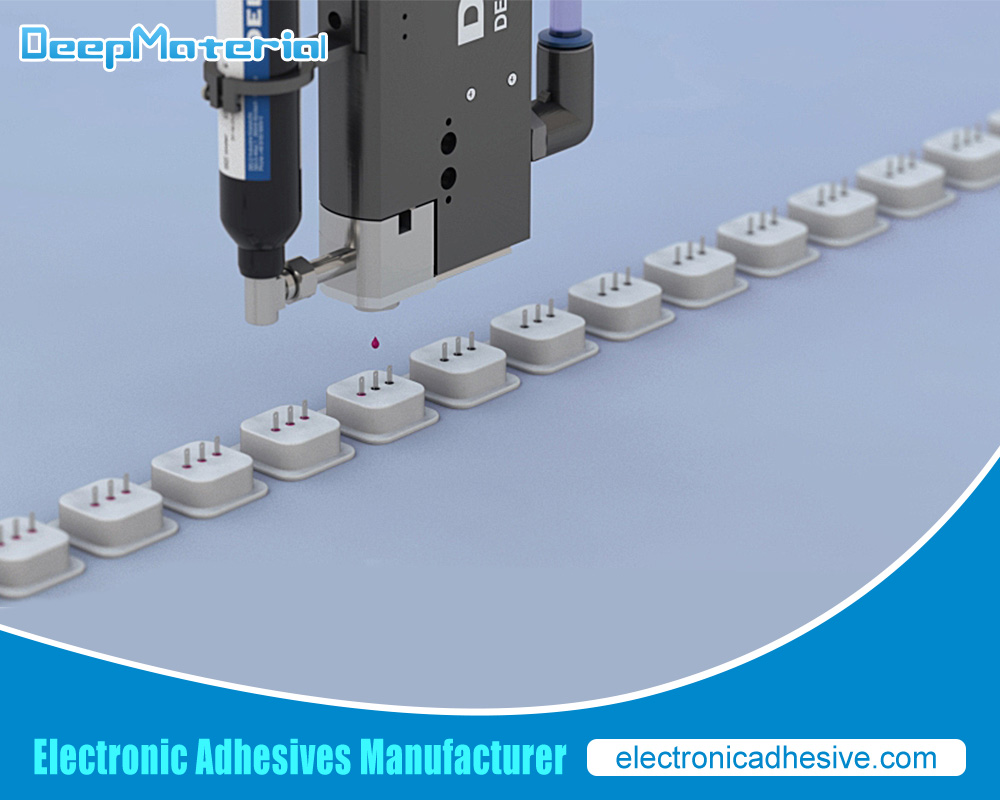
Benefits of Using Electric Motor Epoxy Adhesive
Using epoxy adhesive in electric motors offers several benefits to their performance, reliability, and longevity.
Enhanced Durability
Epoxy adhesives form durable bonds that withstand mechanical stresses, vibrations, and thermal cycling. This durability ensures that the motor components remain securely bonded throughout the motor’s operational life.
Improved Electrical Insulation
The high dielectric strength of epoxy adhesives provides excellent electrical insulation, reducing the risk of short circuits and electrical failures. This is particularly important in high-voltage and high-performance motors.
Resistance to Environmental Factors
Epoxy adhesives resist various environmental factors, including moisture, chemicals, and temperature variations. This resistance helps protect motor components from corrosion, contamination, and degradation.
Thermal Management
Some epoxy adhesives are formulated with enhanced thermal conductivity, helping to dissipate heat generated within the motor. Efficient thermal management is crucial for preventing overheating and ensuring optimal motor performance.
Ease of Application
Modern epoxy adhesives are designed for easy application, with user-friendly mixing ratios and application methods. This simplifies the manufacturing and repair processes, reducing production times and costs.
Application Techniques for Electric Motor Epoxy Adhesive
Applying epoxy adhesive correctly is crucial to achieving the desired bonding, sealing, and insulating properties. Here are some best practices for applying electric motor epoxy adhesive.
Surface Preparation
Proper surface preparation is essential for achieving a solid bond. The surfaces to be bonded should be clean, dry, and free from contaminants such as grease, oil, and dust.
- Cleaning:Use solvents or cleaning agents to remove grease or oil from the surfaces.
- Abrasion:Lightly scuff the surfaces with sandpaper to create a rough texture, enhancing the adhesive bond.
- Drying:Ensure the surfaces are dehydrated before applying the adhesive.
Mixing the Adhesive
Epoxy adhesives typically consist of two parts: resin and hardener. The resin and hardener must be mixed in the correct ratio to ensure proper curing and performance.
- Measuring:Measure the resin and hardener according to the manufacturer’s instructions.
- Mixing:Thoroughly mix the two components until a uniform consistency is achieved. Use a clean mixing tool and container to avoid contamination.
Application Methods
The application method depends on the motor’s specific requirements and the adhesive being used.
- Brushing:For coating and insulating applications, epoxy can be applied using a brush.
- Dispensing:Use a dispensing tool or syringe to apply the adhesive for precise bonding and sealing.
- Spreading:Spread the adhesive evenly over the surfaces to be bonded, ensuring complete coverage.
Curing
Curing is when the epoxy adhesive undergoes a chemical reaction to harden and form a strong bond. Temperature, humidity, and curing time can influence the curing process.
- Room Temperature Curing:Most epoxy adhesives cure at room temperature. Ensure the bonded parts remain undisturbed during the curing process.
- Heat Curing:Some applications may require heat curing to accelerate the process or achieve specific properties. Follow the manufacturer’s recommendations for heat curing.
Quality Control
After application and curing, quality control checks are essential to ensure the adhesive has achieved the desired properties.
- Visual Inspection:Check for defects, such as air bubbles, incomplete coverage, or contamination.
- Mechanical Testing:Perform tensile and shear tests to verify the bond strength.
- Electrical Testing:Test the electrical insulation properties to ensure proper insulation.
Advances in Electric Motor Epoxy Adhesive Technology
The field of epoxy adhesives for electric motors is continuously evolving, with ongoing research and development leading to new formulations and technologies.
Nano-Enhanced Epoxies
Nano-enhanced epoxy adhesives incorporate nanoparticles to improve mechanical strength, thermal conductivity, and electrical insulation. These advanced adhesives offer superior performance, making them suitable for high-demand applications.
UV-Curable Epoxies
UV-curable epoxy adhesives cure rapidly upon exposure to ultraviolet light. This technology allows quick curing times and precise control over the process, making it ideal for high-speed manufacturing environments.
Environmentally Friendly Formulations
With increasing emphasis on sustainability, manufacturers are developing environmentally friendly epoxy adhesives with reduced volatile organic compounds (VOCs) and improved biodegradability. These formulations offer the same high performance while minimizing environmental impact.
Flexible Epoxies
Traditional epoxy adhesives are known for their rigidity, which can be a limitation in applications requiring flexibility. Flexible epoxy adhesives maintain strong bonding properties while allowing for movement and thermal expansion, making them suitable for dynamic applications.
Case Studies: Real-World Applications of Electric Motor Epoxy Adhesive
Automotive Electric Motors
Electric motors are used in various automotive applications, from electric vehicles (EVs) to hybrid powertrains. Epoxy adhesives play a critical role in ensuring the performance and reliability of these motors.
- EV Motors:High-performance epoxy adhesives bond and insulate components in EV motors, providing the necessary thermal management and electrical insulation.
- Hybrid Systems:In hybrid vehicles, epoxy adhesives bond magnets and other components, ensuring efficient and reliable operation.
Industrial Machinery
Industrial machinery relies on robust electric motors for various applications, including conveyor systems, pumps, and compressors. Epoxy adhesives are essential in maintaining the integrity of these motors.
- Pumps and Compressors:Epoxy adhesives seal and insulate components in pumps and compressors, protecting them from harsh environments and ensuring reliable performance.
- Conveyor Systems:In conveyor systems, epoxy adhesives bond and insulate motor components, reducing downtime and maintenance costs.
Consumer Electronics
Electric motors in consumer electronics, such as fans, vacuum cleaners, and kitchen appliances, also benefit from epoxy adhesive technology.
- Fans:Epoxy adhesives bond and insulate motor components in fans, ensuring quiet and efficient operation.
- Vacuum Cleaners:In vacuum cleaners, epoxy adhesives provide strong bonding and insulation, enhancing motor performance and durability.
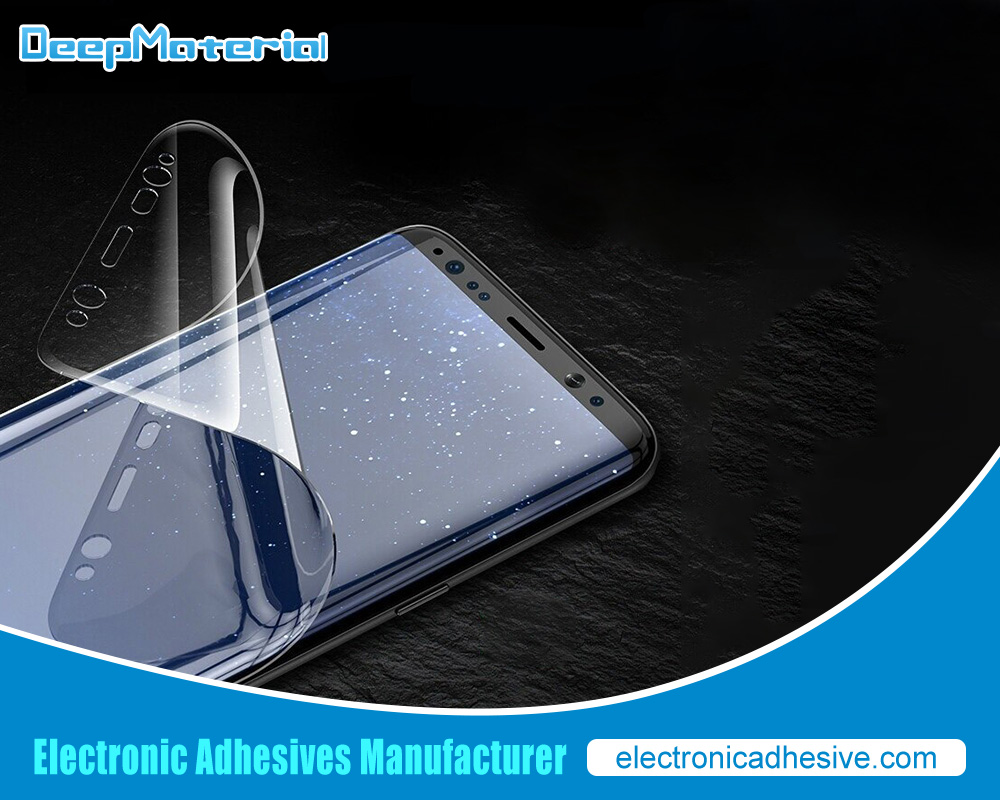
Conclusion
Electric motor epoxy adhesive is a vital material in the manufacturing and maintenance of electric motors. It offers enhanced durability, electrical insulation, and resistance to environmental factors. By understanding its uses, benefits, and application techniques, manufacturers and maintenance professionals can ensure electric motors’ reliable and efficient performance in various applications. With ongoing advancements in epoxy adhesive technology, the future holds even greater potential for improved performance and sustainability in electric motor applications.
For more about understanding electric motor epoxy adhesive: uses, benefits, and application techniques, you can pay a visit to DeepMaterial at https://www.electronicadhesive.com/ for more info.