Understanding Adhesives for Electronic Components: A Comprehensive Guide
Understanding Adhesives for Electronic Components: A Comprehensive Guide
In electronics, the reliable and efficient performance of devices heavily depends on the quality and functionality of their components. One critical aspect often overlooked is the role of adhesives in the assembly and protection of electronic components. This article delves into the various types of adhesives for electronic components, their properties, applications, and considerations for optimal performance.
1. Introduction to Adhesives in Electronics
Adhesives are essential in the assembly and protection of electronic components. They serve multiple purposes, including securing components to printed circuit boards (PCBs), providing insulation, and offering thermal management. The choice of adhesive can impact electronic devices’ overall reliability, durability, and performance.
1.1 The Role of Adhesives
Adhesives in electronics are not merely bonding agents but play a crucial role in ensuring device structural integrity and functionality. They are used in applications such as:
- Component Mounting:Securing components to PCBs or substrates.
- Insulation:Providing electrical insulation between components.
- Thermal Management:Assisting in heat dissipation to prevent overheating.
- Protection:Shielding sensitive components from environmental factors.
1.2 Types of Adhesives
There are several types of adhesives used in electronics, each with unique properties and applications:
- Epoxy Resins
- Silicone Adhesives
- Acrylic Adhesives
- Polyurethane Adhesives
- Conductive Adhesives
2. Properties of Adhesives for Electronics
Several properties must be considered when selecting an adhesive for electronic components to ensure optimal performance and compatibility with the device’s requirements.
2.1 Adhesive Strength and Bonding
The adhesive strength, or the ability to create a strong bond between surfaces, is critical. Factors influencing adhesive strength include:
- Surface Preparation:Proper cleaning and preparation of surfaces enhance bonding.
- Curing Conditions:Temperature and humidity during curing can affect bond strength.
- Material Compatibility:The adhesive must be compatible with the materials being bonded.
2.2 Electrical Insulation
For many electronic applications, adhesives need to provide effective electrical insulation. This prevents short circuits and ensures the safety of the device. Key considerations include:
- Dielectric Strength:The adhesive’s ability to withstand electrical stress.
- Volume Resistivity:Resistance to electrical current flow.
2.3 Thermal Conductivity
In electronics, managing heat is crucial. Adhesives with high thermal conductivity help dissipate heat away from sensitive components, reducing the risk of overheating. Properties to consider:
- Thermal Conductivity:Measured in watts per meter-kelvin (W/m·K).
- Thermal Stability:The adhesive’s adhesive performance is at varying temperatures.
2.4 Chemical Resistance
Electronics are exposed to various chemicals, including cleaning agents and environmental pollutants. Adhesives must be resistant to these substances to maintain their integrity. Important factors:
- Chemical Compatibility:The adhesive’s ability to resist chemical degradation.
- Durability:Long-term performance under chemical exposure.
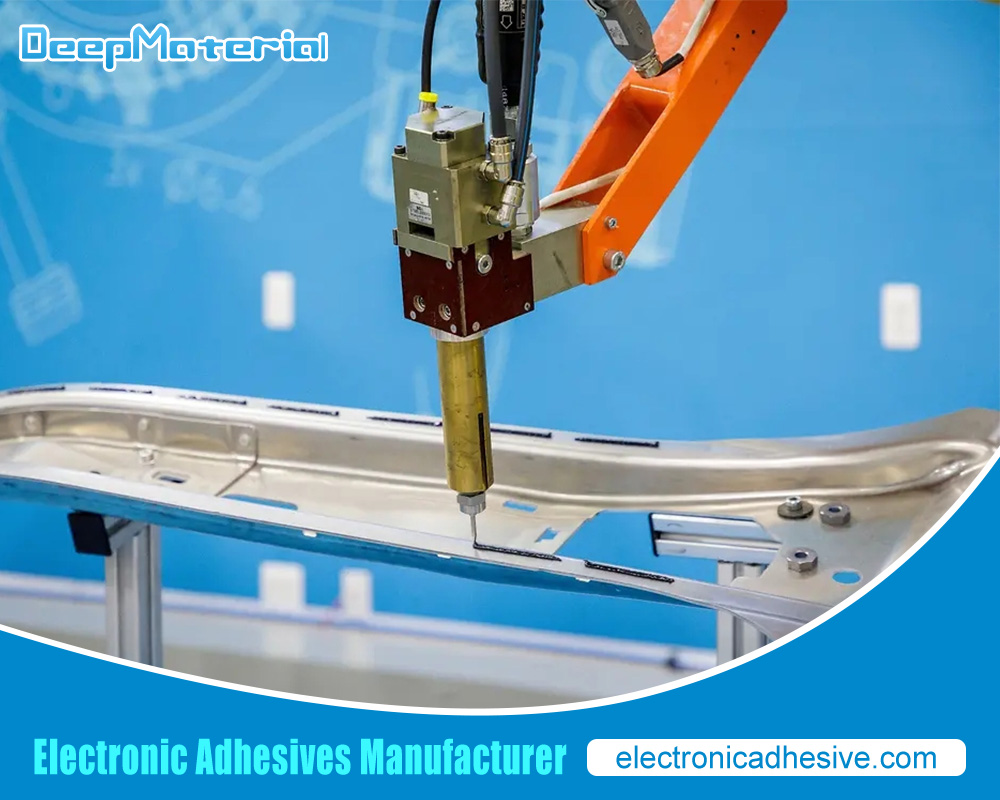
3. Types of Adhesives for Electronic Components
Each type of adhesive has specific properties suited for different electronic applications. Understanding these types helps choose the suitable adhesive for a particular use case.
3.1 Epoxy Resins
Epoxy resins are widely used due to their strong bonding capabilities and durability. They are suitable for:
- Component Mounting:Securely bonding components to PCBs.
- Encapsulation:Protecting components from environmental factors.
3.1.1 Properties of Epoxy Resins
- High Bond Strength:Provides a solid and durable bond.
- Thermal Stability:Can withstand high temperatures.
- Chemical Resistance:Resists most chemicals and solvents.
3.1.2 Applications
- Electronics Encapsulation:Protecting delicate electronic components.
- PCB Assembly:Bonding components and providing structural integrity.
3.2 Silicone Adhesives
Silicone adhesives are known for their flexibility and temperature resistance. They are used in applications where flexibility and thermal stability are required.
3.2.1 Properties of Silicone Adhesives
- Flexibility:Allows for thermal expansion and contraction.
- High-Temperature Resistance:Can withstand extreme temperatures.
- Electrical Insulation:Provides effective electrical insulation.
3.2.2 Applications
- Thermal Management:Used in thermal interface materials.
- Sealing and Insulation:This protects and seals electronic components.
3.3 Acrylic Adhesives
Acrylic adhesives offer quick curing times and good initial tack. They are suitable for various electronic applications, including:
3.3.1 Properties of Acrylic Adhesives
- Fast Curing:Quick setting time reduces production time.
- Good Bonding Strength:Provides a solid bond to various substrates.
- UV Resistance:Can withstand exposure to UV light.
3.3.2 Applications
- Component Bonding:This is for applications requiring quick assembly.
- Protective Coatings:For shielding components from environmental damage.
3.4 Polyurethane Adhesives
Polyurethane adhesives are known for their versatility and durability. They are used in applications where toughness and flexibility are required.
3.4.1 Properties of Polyurethane Adhesives
- High Strength:Provides strong and durable bonds.
- Flexibility:Allows for movement and expansion.
- Environmental Resistance:Resists moisture and chemicals.
3.4.2 Applications
- Component Mounting:This is used to secure components in rugged environments.
- Protective Coatings:Providing additional protection against moisture and chemicals.
3.5 Conductive Adhesives
Conductive adhesives are used when electrical conductivity is required between components. They are essential for:
3.5.1 Properties of Conductive Adhesives
- Electrical Conductivity:Allows for electrical connections between components.
- Thermal Conductivity:Often used in thermal management applications.
- Adhesive Strength:Ensures strong bonding while maintaining conductivity.
3.5.2 Applications
- Interconnects:Connecting electronic components where traditional soldering is not feasible.
- Shielding:Providing electromagnetic shielding in sensitive devices.
4. Selecting the Right Adhesive for Your Application
Choosing the suitable adhesive involves considering various factors to ensure it meets the specific requirements of the electronic components and the intended application.
4.1 Application Requirements
Consider the specific needs of the application, such as:
- Bond Strength:Determine the required strength for secure bonding.
- Thermal Management:Choose adhesives with appropriate thermal conductivity.
- Environmental Factors:Consider exposure to chemicals, moisture, and temperature variations.
4.2 Compatibility
Ensure the adhesive is compatible with the materials used—test adhesion to ensure a robust and reliable bond.
4.3 Curing Conditions
Different adhesives require different curing conditions. Ensure the curing process aligns with the production environment and the adhesive’s requirements.
4.4 Testing and Validation
Perform thorough testing to validate the adhesive’s performance in real-world conditions. This includes:
- Mechanical Testing:Assess bond strength and durability.
- Electrical Testing:Ensure electrical insulation and conductivity.
- Thermal Testing:Verify thermal stability and conductivity.
5. Future Trends and Innovations in Adhesives for Electronics
The field of adhesives for electronics is continuously evolving with advancements in technology. Future trends include:
5.1 Advanced Materials
Innovations in adhesive materials, such as nano-composites and advanced polymers, offer improved strength, flexibility, and thermal management performance.
5.2 Environmental Considerations
A growing focus is on developing eco-friendly adhesives with reduced environmental impact, such as water-based or bio-based adhesives.
5.3 Enhanced Performance
Research and development efforts aim to enhance adhesive properties, including higher thermal and electrical conductivity, better chemical resistance, and improved long-term durability.
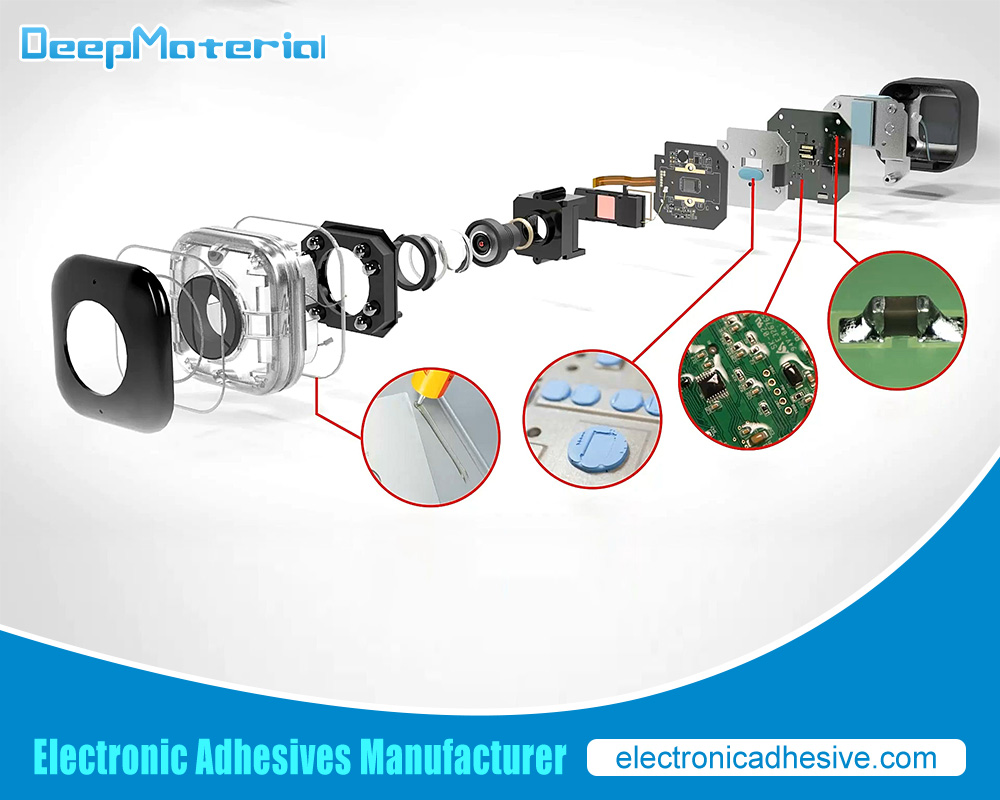
Conclusion
Adhesives play a crucial role in the assembly and protection of electronic components. Understanding the properties and applications of different adhesives helps select the most suitable option for specific needs. As technology advances, the development of new adhesive materials and formulations continues to enhance the performance and reliability of electronic devices. By considering factors such as bonding strength, electrical insulation, thermal management, and environmental resistance, manufacturers can ensure the optimal performance of their electronic components and devices.
For more about understanding adhesives for electronic components: a comprehensive guide, you can pay a visit to DeepMaterial at https://www.electronicadhesive.com/ for more info.