The Role of Industrial Appliance Adhesive Manufacturers in Modern Manufacturing
The Role of Industrial Appliance Adhesive Manufacturers in Modern Manufacturing
In today’s fast-paced world, manufacturing industries are constantly pressured to improve efficiency, enhance product quality, and reduce costs. One critical component in achieving these goals, particularly in the industrial appliance sector, is the use of specialized adhesives. Adhesives have become a cornerstone in appliance assembly, replacing traditional mechanical fasteners due to their ability to provide a cleaner, more efficient, and durable bond.
Industrial appliance adhesive manufacturers play a vital role in supplying high-performance bonding solutions that meet the stringent requirements of modern manufacturing processes. From ensuring structural integrity to providing electrical insulation, these adhesives contribute significantly to appliances’ functionality, longevity, and overall quality. This article delves into the importance of adhesive manufacturers in the appliance industry, the types of adhesives used, and the benefits they provide in the production process.
The Importance of Adhesives in the Appliance Industry
Adhesives have transformed the way appliances are designed and manufactured, offering solutions that go beyond the capabilities of traditional bonding methods like screws, bolts, and welds. Adhesives in the appliance industry help to:
- Improve product aesthetics by eliminating visible fasteners.
- Provide superior bonding strength, ensuring the long-term durability of products.
- Allow lighter materials to be used, reducing the overall weight of appliances.
- Enhance energy efficiency by sealing components tightly and minimizing air leakage.
- Simplify manufacturing processes, reducing the need for complex machinery and assembly techniques.
Industrial appliance adhesive manufacturers are at the forefront of innovation, developing adhesives that cater to the unique demands of modern appliances, such as enhanced heat resistance, flexibility, and environmental sustainability.
Critical Types of Adhesives Used in Industrial Appliances
The choice of adhesive in the appliance manufacturing industry depends on the product’s specific requirements, such as the materials involved, the operating conditions, and the desired properties of the final bond. Below are the most commonly used types of adhesives:
1. Epoxy Adhesives
Epoxy adhesives are known for their high bonding strength and durability, making them ideal for use in appliances subject to heavy loads or extreme conditions. They also offer excellent resistance to heat, chemicals, and moisture, ensuring that appliances maintain their performance over time.
2. Polyurethane Adhesives
Polyurethane adhesives are prized for their flexibility and ability to bond various materials, including metals, plastics, and glass. These adhesives are commonly used to assemble refrigerators, washing machines, and other appliances that require solid and flexible bonds.
3. Silicone Adhesives
Silicone adhesives are highly resistant to temperature extremes and are commonly used in appliances that operate in high-heat environments, such as ovens and stovetops. Their elasticity and resistance to degradation make them a go-to solution for sealing and bonding components exposed to harsh conditions.
4. Acrylic Adhesives
Acrylic adhesives are known for their fast curing times and excellent adhesion properties. They are used in applications where speed and strength are critical, such as assembling smaller appliances like blenders and coffee makers.
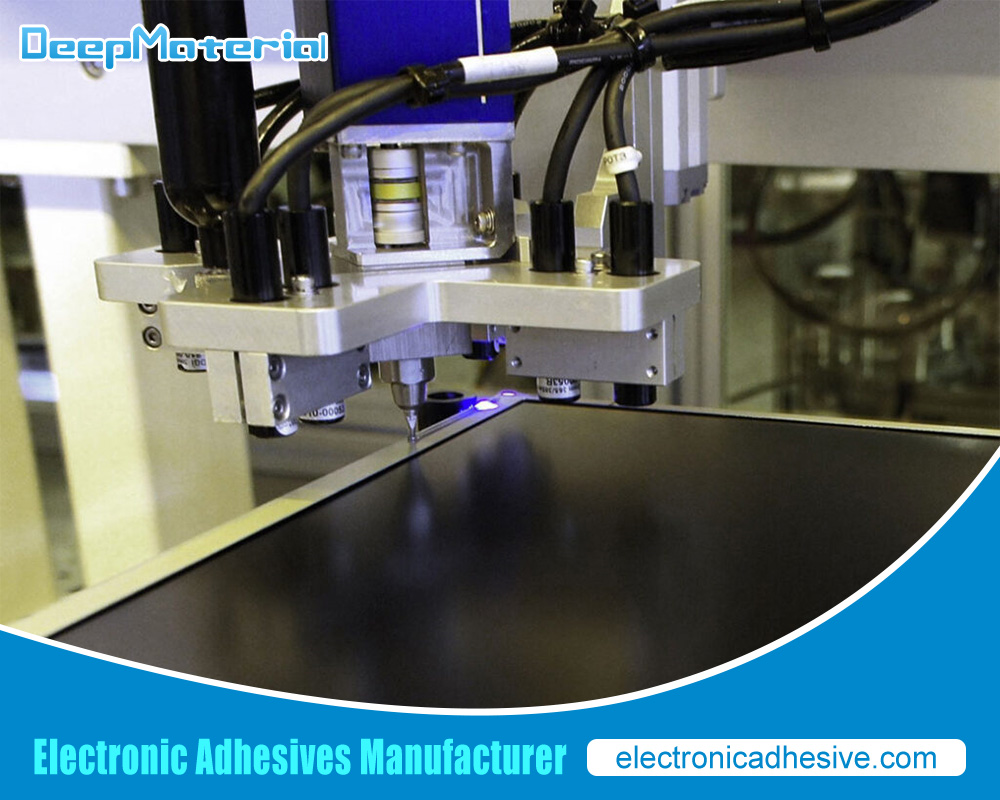
Advantages of Using Adhesives in Appliance Manufacturing
The shift toward adhesives in appliance manufacturing offers several key benefits, driving their increasing adoption across the industry. Below are some of the most notable advantages:
Improved Durability
- Adhesives provide a strong and consistent bond that can withstand vibration, thermal expansion, and environmental stressors. It leads to more durable appliances that perform better over time, reducing the need for repairs and replacements.
Weight Reduction
- Using adhesives allows manufacturers to use lighter materials without sacrificing strength. It can lead to more energy-efficient appliances, as lighter products consume less power during operation and transport.
Enhanced Aesthetics
- Adhesives contribute to sleeker, more attractive designs by eliminating the need for mechanical fasteners. The absence of screws, rivets, and other visible fasteners gives appliances a smooth, seamless appearance, which is increasingly desirable in today’s consumer market.
Increased Production Efficiency
- Adhesives simplify the assembly process by reducing the need for complicated machinery and techniques. It can lead to faster production times, lower labor costs, and fewer assembly errors, ultimately improving the overall efficiency of the manufacturing process.
Noise and Vibration Dampening
- Adhesives provide excellent dampening properties, reducing noise and vibration in dishwashers, washing machines, and dryers. This results in quieter operation and a more pleasant user experience.
Challenges Faced by Industrial Appliance Adhesive Manufacturers
While adhesives offer many advantages, there are also challenges that industrial appliance adhesive manufacturers must address to ensure their products meet the evolving needs of the industry. These challenges include:
Adapting to New Materials
As manufacturers increasingly adopt new materials like lightweight composites and advanced plastics, adhesive manufacturers must continuously develop products that can effectively bond these materials. Creating adhesives that offer the necessary performance characteristics requires ongoing research and development.
Environmental Regulations
Adhesive manufacturers must comply with strict environmental regulations regarding using volatile organic compounds (VOCs) and other hazardous chemicals. This has led to the development of eco-friendly adhesives that minimize environmental impact while delivering high performance.
Heat and Chemical Resistance
Many modern appliances, such as ovens and refrigerators, are exposed to extreme temperatures and harsh chemicals. Adhesive manufacturers must formulate products that can withstand these conditions without degrading, ensuring the longevity and safety of the appliance.
Meeting Industry Standards
Adhesive manufacturers must ensure their products comply with industry-specific standards and certifications, such as those set by Underwriters Laboratories (UL) and other regulatory bodies. It involves rigorous testing and quality control measures to ensure the adhesives meet safety and performance requirements.
Future Trends in Industrial Appliance Adhesives
The appliance industry constantly evolves, and adhesive manufacturers must stay ahead of emerging trends to remain competitive. Some of the key trends shaping the future of industrial appliance adhesives include:
Sustainability and Eco-Friendly Adhesives
As consumers and governments become increasingly focused on sustainability, the demand for environmentally friendly adhesives grows. Manufacturers are developing adhesives free from harmful chemicals, offering biodegradable options, and reducing energy consumption during production and application.
Smart Adhesives for Connected Appliances
With the rise of smart appliances, there is an increasing need for adhesives that can bond components involved in data transfer and electronic connectivity. Adhesive manufacturers are exploring new technologies to create adhesives with conductive properties, which are essential for the functionality of smart devices.
Customization and Specialized Formulations
Every appliance has unique bonding requirements, driving the demand for customized adhesive formulations. Manufacturers work closely with appliance makers to develop adhesives tailored to specific applications, such as high-temperature resistance for ovens or dishwasher waterproofing.
Automated Adhesive Application Systems
Automation is transforming the manufacturing landscape, and adhesive application is no exception. Many appliance manufacturers are investing in automated systems that can precisely apply adhesives to components, improving accuracy, reducing waste, and speeding up production lines. Adhesive manufacturers are responding by developing formulations optimized for automated application processes.
The Role of Adhesive Manufacturers in Ensuring Appliance Safety
Adhesive manufacturers play a critical role in ensuring the safety of appliances, particularly in high-risk applications such as ovens, heaters, and electrical devices. Adhesives used in these products must withstand extreme temperatures, electrical currents, and exposure to hazardous substances without compromising their integrity. Adhesive manufacturers conduct extensive testing and quality assurance to ensure their products meet safety standards and can perform under the most demanding conditions.
By providing fire-resistant, non-toxic adhesives capable of insulating electrical components, these manufacturers contribute significantly to the overall safety of household and industrial appliances.
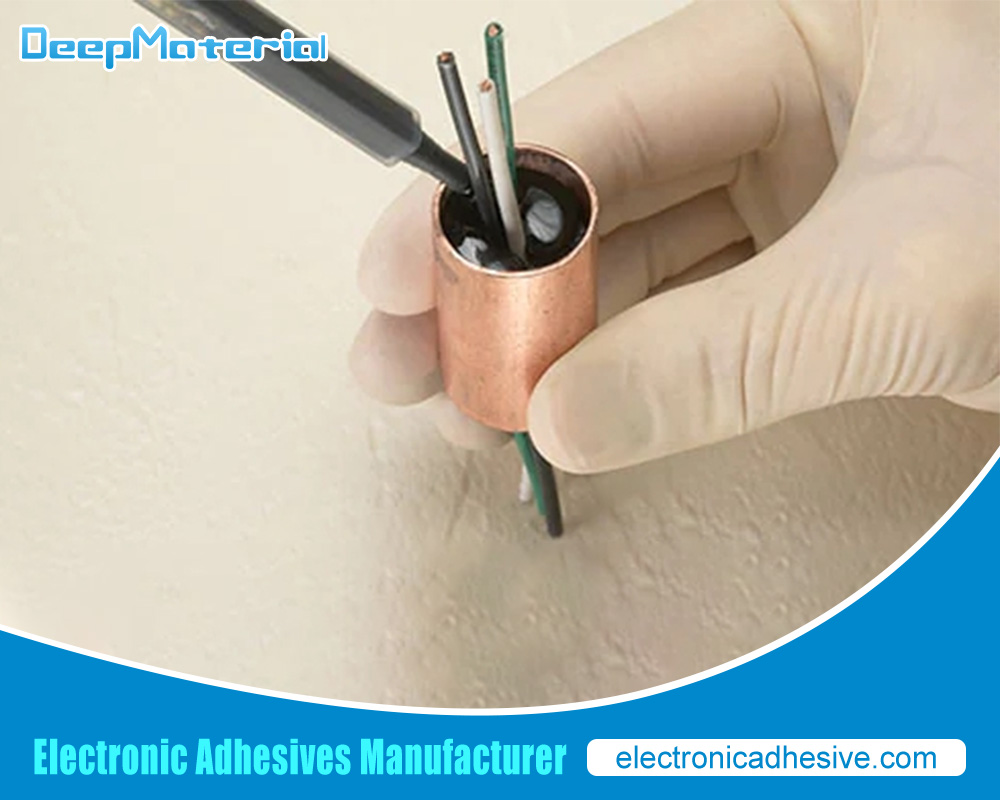
Conclusion
The importance of industrial appliance adhesive manufacturers must be addressed in today’s manufacturing world. As appliances become more complex, energy-efficient, and aesthetically pleasing, the role of adhesives in their production grows in importance. Industrial appliance adhesive manufacturers provide the bonding solutions necessary for modern appliances and drive innovation in areas like sustainability, safety, and performance.
For more about choosing the role of industrial appliance adhesive manufacturers in modern manufacturing, you can pay a visit to DeepMaterial at https://www.electronicadhesive.com/ for more info.