The Role of Automotive Bonding Adhesives in Modern Vehicle Manufacturing
The Role of Automotive Bonding Adhesives in Modern Vehicle Manufacturing
The quest for improved performance, safety, and efficiency has led to significant advancements in materials and manufacturing techniques in the automotive industry. One of the key innovations driving this evolution is using automotive bonding adhesives. As the demand for lightweight vehicles and enhanced structural integrity grows, automotive bonding adhesive manufacturers are stepping up to provide solutions that meet the challenges of modern automotive design. This article explores the significance of automotive bonding adhesives, their types, applications, benefits, and future trends in the industry.
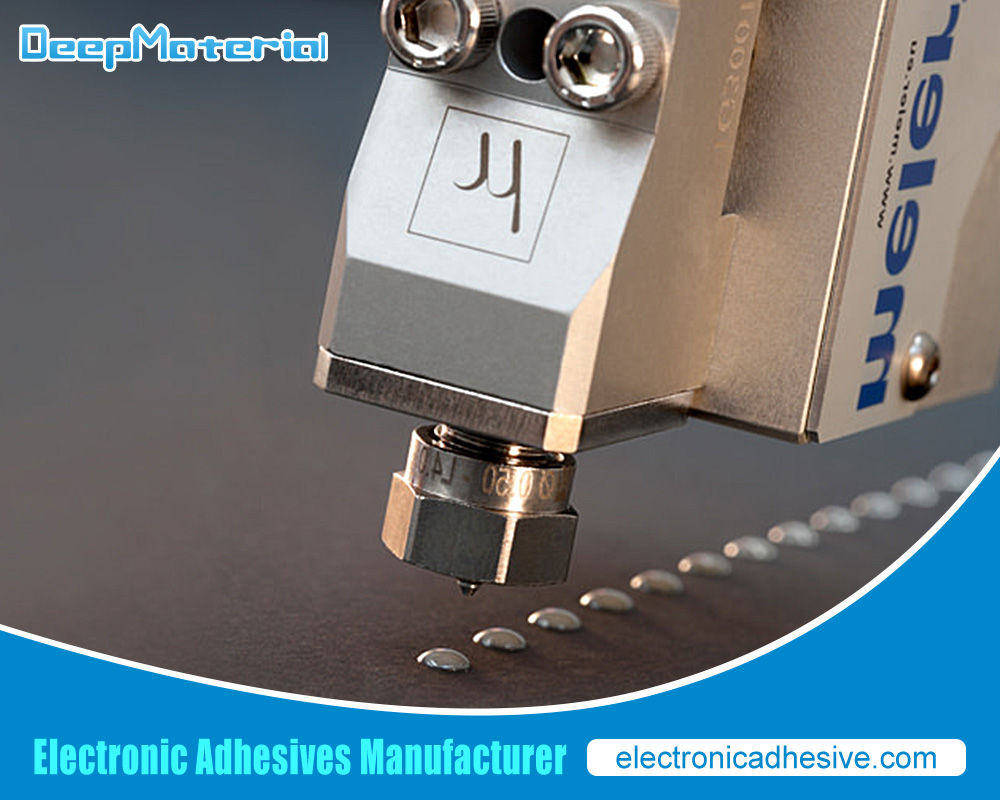
Understanding Automotive Bonding Adhesives
Automotive bonding adhesives are specialized adhesives designed to bond various materials used in vehicle manufacturing. These adhesives play a crucial role in joining components, enhancing the overall strength and durability of the vehicle.
Types of Automotive Bonding Adhesives
There are several types of automotive bonding adhesives, each suited for different applications:
Polyurethane Adhesives
- Flexible and durable.
- Excellent for bonding dissimilar materials.
- Commonly used in structural bonding and sealing applications.
Epoxy Adhesives
- Strong bonding capabilities.
- Resistant to heat and chemicals.
- Ideal for applications requiring high strength.
Acrylic Adhesives
- Fast curing and strong.
- Good resistance to environmental factors.
- Often used in glass bonding and trim applications.
Silicone Adhesives
- Excellent flexibility and temperature resistance.
- Used for sealing and bonding applications where movement is expected.
Critical Applications in Automotive Manufacturing
Automotive bonding adhesives are used in various applications, including:
Body Assembly
- Joining panels and components to create a cohesive structure.
Glass Installation
- Bonding windshields and windows securely.
Interior Assembly
- Attaching trim pieces and upholstery.
Underbody Protection
- Sealing and bonding materials to prevent corrosion and damage.
Benefits of Using Automotive Bonding Adhesives
The advantages of incorporating automotive bonding adhesives into vehicle manufacturing processes are significant:
Enhanced Structural Integrity
Weight Reduction
- Bonding adhesives enable the use of lighter materials, contributing to overall weight reduction.
Stress Distribution
- The flexibility of adhesives allows for better stress distribution, reducing the risk of structural failure.
Improved Safety
Crashworthiness
- Adhesives can enhance the vehicle’s ability to withstand impact, improving occupant safety.
Vibration Damping
- They help absorb vibrations, leading to a smoother ride and less component wear.
Greater Design Flexibility
Material Compatibility
- Bonding adhesives can bond various materials, including metals, plastics, and composites, allowing for innovative designs.
Aesthetic Appeal
- Seamless joints can be achieved, enhancing the visual appeal of the vehicle.
The Role of Automotive Bonding Adhesive Manufacturers
Automotive bonding adhesive manufacturers play a vital role in developing and supplying these crucial materials. Their expertise in formulating adhesives that meet the specific needs of the automotive industry is essential for ensuring quality and performance.
Key Players in the Industry
The automotive bonding adhesive market features several leading manufacturers, each contributing unique formulations and technologies:
3M
- Known for a wide range of bonding solutions tailored for automotive applications.
Henkel
- Offers innovative adhesive technologies, including LOCTITE products.
Sika
- Specializes in structural adhesives that enhance durability and safety.
BASF
- Provides a variety of adhesive solutions with a focus on sustainability.
Research and Development
Continuous R&D is crucial for automotive bonding adhesive manufacturers to stay ahead of market trends. This involves:
Material Innovation
- Developing new adhesive formulations that enhance performance and reduce environmental impact.
Testing and Certification
- Rigorous testing ensures that adhesives meet automotive standards for safety and performance.
Collaboration with OEMs
- Working closely with Original Equipment Manufacturers (OEMs) to develop tailored solutions that meet specific requirements.
Future Trends in Automotive Bonding Adhesives
As the automotive industry continues to evolve, so do the needs and technologies associated with bonding adhesives. Here are some key trends to watch:
Shift Toward Lightweight Materials
Electric Vehicles (EVs)
The rise of EVs drives the demand for lightweight materials and adhesives that facilitate this transition.
Advanced Composites
The use of composite materials is increasing, necessitating adhesives that can bond these materials effectively.
Sustainability Focus
Eco-Friendly Formulations
- Manufacturers are increasingly developing less environmentally harmful adhesives that can be recycled.
Reduced VOC Emissions
- Innovations are being made to reduce volatile organic compounds (VOCs) in adhesive formulations.
Automation and Smart Manufacturing
Automated Bonding Processes
- The integration of robotics in adhesive application processes is improving efficiency and consistency.
Smart Adhesives
- Development of adhesives with built-in sensors to monitor the integrity of bonds over time.
Selecting the Right Automotive Bonding Adhesive: Key Considerations
Choosing the appropriate automotive bonding adhesive is crucial for ensuring optimal performance and safety in vehicle manufacturing. Here are some essential factors to consider when selecting the suitable adhesive for a specific application:
Material Compatibility
- Dissimilar Materials:Ensure the adhesive is compatible with bonded materials, such as metals, plastics, or composites.
- Surface Preparation: Some adhesives require specific surface treatments (e.g., cleaning or priming) for optimal adhesion.
Environmental Resistance
- Temperature Extremes: Evaluate the adhesive’s performance under varying conditions, especially for parts exposed to high heat or cold.
- Chemical Exposure:Consider potential exposure to chemicals, such as fuels, oils, and cleaning agents, which can affect adhesive performance.
Bonding Strength
- Load Requirements: Assess the mechanical loads the bonded joint will experience, ensuring the adhesive can withstand these stresses without failure.
- Peel and Shear Strength: Look for adhesives with high peel and shear strength, particularly for critical structural applications.
Cure Time and Application Method
- Cure Speed: Determine how quickly the adhesive sets and achieves full strength, which can impact manufacturing efficiency.
- Application Technique:Choose an adhesive that matches the application method (e.g., manual, automated, or spray).
Regulatory Compliance
- Safety Standards: Ensure the adhesive meets relevant safety and performance standards set by industry regulators.
- Environmental Regulations:Consider adhesives that comply with environmental regulations, especially regarding VOC emissions.
Aesthetic Considerations
- Precise or Color Matching:For visible joints, select adhesives that can either cure clear or be color-matched to the components for aesthetic appeal.
- Surface Finish:Assess how the adhesive affects the surface finish of the bonded parts, as this can impact the vehicle’s overall appearance.
Manufacturer Support and Expertise
- Technical Support: Choose manufacturers with strong technical support and resources for selecting and applying adhesives.
- R&D Capabilities: Look for manufacturers with a solid research and development background to ensure access to innovative adhesive solutions.
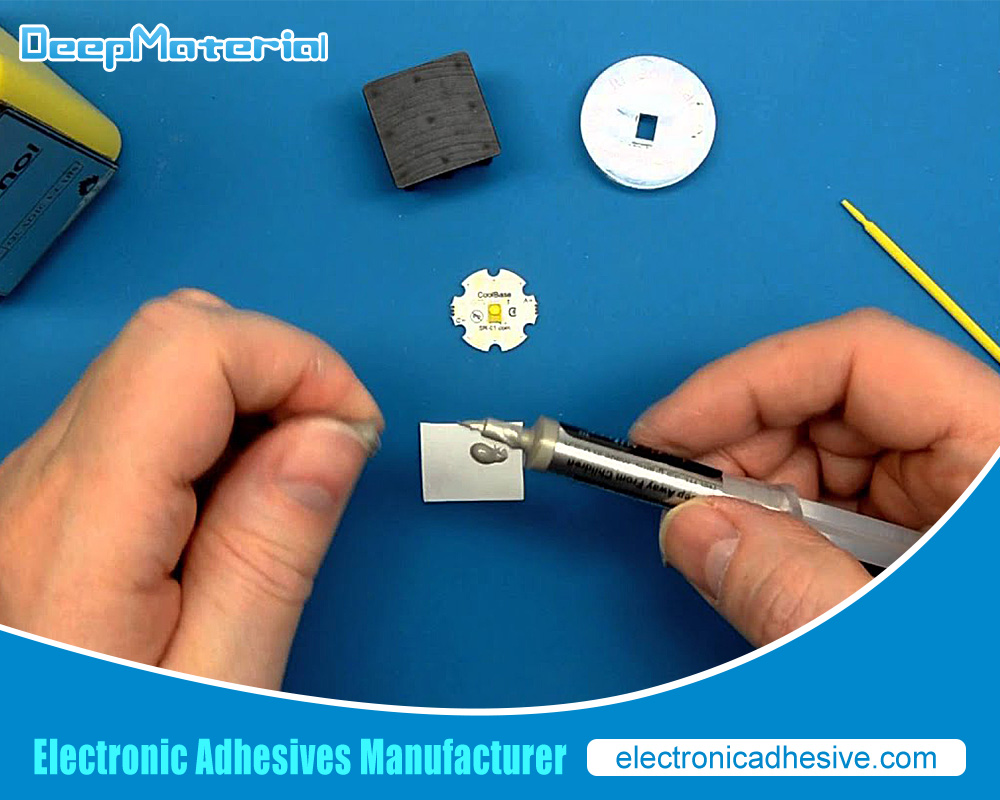
Conclusion
The automotive industry is undergoing rapid changes, driven by technological advancements and evolving consumer demands. Automotive bonding adhesives have emerged as a critical component in this transformation, offering solutions that enhance safety, performance, and design flexibility. As automotive bonding adhesive manufacturers continue to innovate and respond to the industry’s needs, the future of vehicle manufacturing looks promising. By prioritizing sustainability and efficiency, these manufacturers are shaping the vehicles of tomorrow and contributing to a more sustainable future for the automotive sector. As we move forward, the role of these adhesives will undoubtedly remain central to the development of safer, lighter, and more efficient vehicles.
For more about choosing the role of automotive bonding adhesives in modern vehicle manufacturing, you can pay a visit to DeepMaterial at https://www.electronicadhesive.com/ for more info.