The Intricacies and Innovations of Electronic Encapsulation
The Intricacies and Innovations of Electronic Encapsulation
In the realm of modern electronics, electronic encapsulation plays a pivotal role. This process, which involves protecting electronic components and circuits, ensures their longevity, reliability, and performance in various environments. As electronics become increasingly sophisticated and miniaturized, encapsulation techniques have evolved to meet the demanding needs of contemporary technology. This article delves into the intricacies of electronic encapsulation, exploring its importance, methods, materials, and future trends.
The Importance of Electronic Encapsulation
Electronic encapsulation is essential for several reasons. First and foremost, it protects electronic components from environmental factors such as moisture, dust, chemicals, and temperature extremes. This protection is crucial for maintaining the functionality and longevity of electronic devices, especially those used in harsh environments like automotive, aerospace, and industrial applications.
Encapsulation also provides electrical insulation, preventing short circuits and electrical failures. By isolating sensitive components, encapsulation helps maintain the integrity of the electrical signals and reduces the risk of interference and crosstalk between different parts of the circuit.
Furthermore, encapsulation enhances the mechanical stability of electronic assemblies. It provides physical support, reducing the risk of damage due to vibration, shock, or mechanical stress. This is particularly important in applications where devices are subjected to constant movement or potential impact.
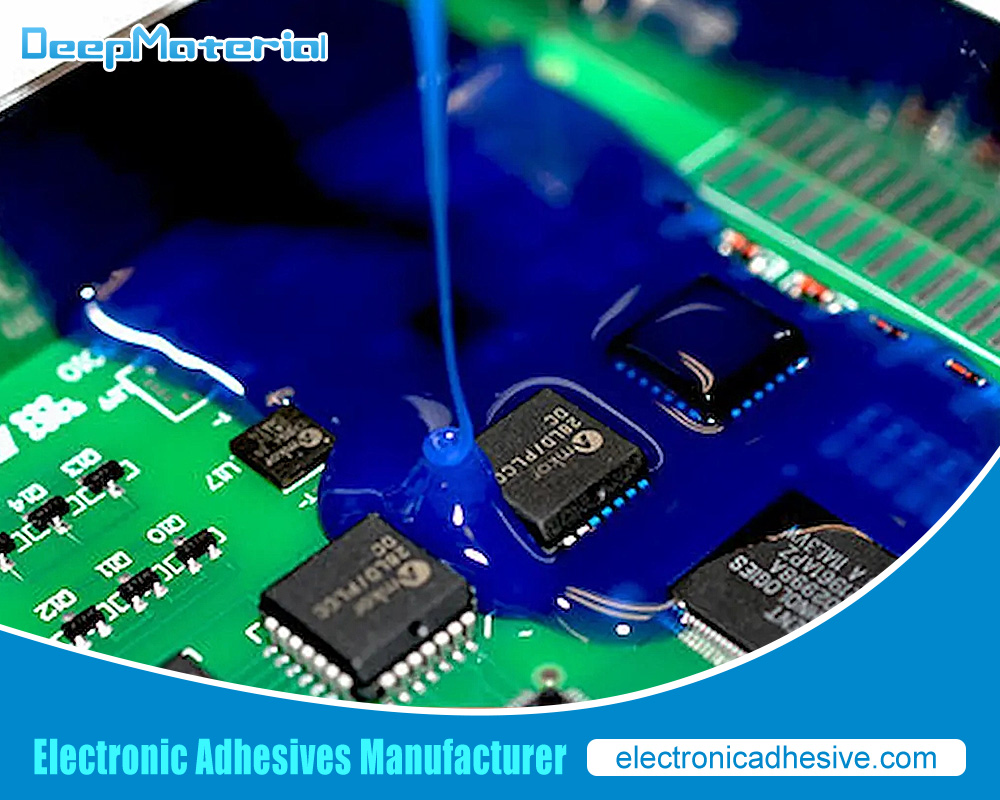
Methods of Electronic Encapsulation
Several methods are employed in electronic encapsulation, each tailored to specific requirements and applications. The choice of method depends on factors such as the type of components being protected, the environmental conditions they will be exposed to, and the desired mechanical and electrical properties of the encapsulant.
Potting
Potting is one of the most common encapsulation methods. It involves placing the electronic assembly into a mold or case and then filling it with a liquid encapsulant, which hardens to form a solid, protective layer. Potting materials are typically thermosetting polymers like epoxy, polyurethane, or silicone. This method provides excellent protection against environmental factors and mechanical stresses.
Potting is widely used in applications where components are exposed to harsh conditions, such as automotive and aerospace electronics. It ensures that the components are fully enclosed and protected, offering high reliability and durability.
Conformal Coating
Conformal coating involves applying a thin, protective material layer directly onto the electronic assembly’s surface. Unlike potting, which fully encapsulates the components, conformal coatings are much thinner and conform to the contours of the components. Common materials used for conformal coatings include acrylics, silicones, polyurethanes, and perylene.
This method protects moisture, dust, and chemical contaminants while allowing heat dissipation and maintaining a lightweight profile. Conformal coatings are often used in consumer electronics, medical devices, and military applications where weight and space constraints are critical.
Encapsulation Resins
Encapsulation resins protect electronic components by encapsulating them in a resin material. These resins are typically poured or injected into a mold containing the electronic assembly and then cured to form a solid protective layer. Epoxy resins are commonly used due to their excellent mechanical and thermal properties.
This method is suitable for applications requiring high levels of protection and durability, such as in power electronics and industrial equipment. Encapsulation resins provide excellent resistance to environmental factors and mechanical stress, ensuring the longevity and reliability of the components.
Overmolding
Overmolding is a technique in which electronic components are placed in a mold, and a second material is injected over them to form a protective layer. This method often creates integrated electronic assemblies with complex shapes and designs. Overmolding materials can include thermoplastics, elastomers, or thermosetting polymers.
This technique is commonly used in producing connectors, sensors, and other electronic devices where a seamless integration of components and protective layers is required. Overmolding provides robust mechanical protection and can enhance the final product’s aesthetic appeal.
Materials Used in Electronic Encapsulation
The choice of encapsulation material is critical to the performance and reliability of the protected electronic components. Various materials are used, each offering specific properties and benefits.
Epoxy Resins
Epoxy resins are widely used in electronic encapsulation due to their excellent mechanical strength, thermal stability, and chemical resistance. They provide high protection against environmental factors and mechanical stresses, making them ideal for applications in harsh environments.
Epoxy resins are commonly used in potting and encapsulation resins, providing a solid, durable protective layer for electronic assemblies. They are also used in over-molding applications requiring high strength and stability.
Polyurethane Resins
Polyurethane resins offer flexibility and excellent resistance to abrasion and impact. They are often used in applications where components are subjected to mechanical stress and movement. Polyurethanes also provide good chemical resistance and can be formulated to have specific electrical properties.
Polyurethane resins are commonly used in potting and encapsulation applications where flexibility and durability are required. They are also used in over-molding and conformal coating applications where a protective yet flexible layer is needed.
Silicone Resins
Silicone resins are known for their excellent thermal stability, flexibility, and resistance to moisture and chemicals. They provide high protection in applications where components are exposed to extreme temperatures and environmental conditions.
Silicone resins are commonly used in conformal coatings and potting applications, providing a flexible, protective layer for electronic assemblies. They are also used in over-molding applications where thermal stability and flexibility are critical.
Acrylics
Acrylics are commonly used in conformal coatings due to their excellent adhesion, transparency, and ease of application. They provide reasonable protection against moisture, dust, and chemicals while allowing for easy inspection of the components.
Acrylic conformal coatings are often used in consumer electronics, medical devices, and other applications requiring lightweight and transparent protection. They provide a thin, protective layer that conforms to the contours of the components.
Parylene
Parylene is a unique polymer used in conformal coatings due to its excellent barrier properties and ability to conform to complex shapes. It is applied through a vapor deposition, ensuring a uniform, pinhole-free coating.
Parylene is commonly used in medical devices, aerospace electronics, and other applications where high levels of protection and reliability are required. It provides an excellent barrier against moisture, chemicals, and other environmental factors.
Challenges in Electronic Encapsulation
Despite its numerous benefits, electronic encapsulation presents several challenges. One of the primary challenges is selecting the appropriate encapsulation material and method for a specific application. This requires a thorough understanding of the components’ environmental conditions, mechanical stresses, and electrical requirements.
Another challenge is ensuring the compatibility of the encapsulation material with the components. Some materials may cause adverse reactions, such as corrosion or degradation of the elements, leading to failures. Thorough testing and evaluation are essential to ensure compatibility and reliability.
Encapsulation itself can also be challenging. It requires precise control of the material application, curing processes, and quality assurance to ensure consistent and reliable protection. Any defects or inconsistencies in the encapsulation layer can compromise the security and lead to failures.
Future Trends in Electronic Encapsulation
As technology advances, the electronic encapsulation field is also evolving. Several trends are shaping the future of encapsulation techniques and materials.
Advanced Materials
Research and development are focused on creating advanced encapsulation materials with enhanced properties. This includes materials with improved thermal conductivity, electrical insulation, and mechanical strength. Nanocomposites and hybrid materials are being explored to provide superior protection and performance.
Miniaturization and Integration
The trend towards miniaturization and integrating electronic components drives the need for more compact and efficient encapsulation techniques. Innovative methods such as wafer-level and 3D encapsulation are being developed to meet the demands of modern electronics.
Environmentally Friendly Encapsulation
There is a growing emphasis on environmentally friendly and sustainable encapsulation materials and processes. This includes the development of biodegradable and recyclable materials and processes that reduce waste and energy consumption. The push towards green electronics influences the materials and methods used in encapsulation.
Smart Encapsulation
Smart encapsulation involves integrating sensing and monitoring capabilities into the encapsulation layer. This allows for real-time monitoring of the health and performance of the encapsulated components, enabling predictive maintenance and improving reliability. Smart encapsulation materials can detect changes in temperature, humidity, and mechanical stress, providing valuable data for optimizing performance and longevity.
Additive Manufacturing
Additive manufacturing, or 3D printing, is revolutionizing the field of electronic encapsulation. This technology allows for creating complex, custom-designed encapsulation structures with precise control over the material properties. Additive manufacturing enables the production of lightweight, high-performance encapsulation solutions tailored to specific applications.
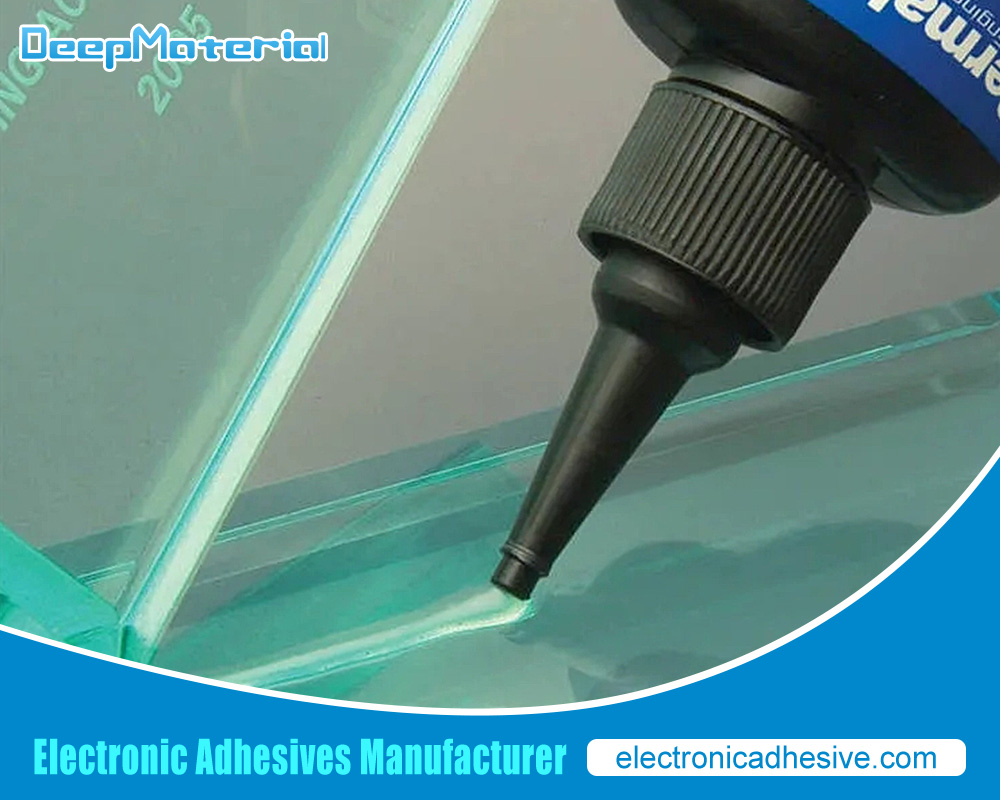
Conclusion
Electronic encapsulation is a critical aspect of modern electronics, providing essential protection and enhancing the performance and reliability of electronic components. The various methods and materials used in encapsulation offer unique benefits and are tailored to meet the specific requirements of different applications.
As technology advances, the field of electronic encapsulation is evolving, with new materials, techniques, and trends shaping the future. The development of advanced materials, miniaturization, environmentally friendly solutions, brilliant encapsulation, and additive manufacturing are driving innovation and expanding the possibilities for electronic encapsulation.
The ongoing research and development in this field promise to address the challenges and push the boundaries of what is possible, ensuring that electronic components can withstand the demands of increasingly sophisticated and harsh environments. Electronic encapsulation remains a vital component of the electronics industry, contributing to the reliability, durability, and performance of devices that power our modern world.
For more about choosing the intricacies and innovations of electronic encapsulation, you can pay a visit to DeepMaterial at https://www.electronicadhesive.com/ for more info.