The Importance of OLED Display Module Adhesive in Modern Technology
The Importance of OLED Display Module Adhesive in Modern Technology
The advancement of display technologies has revolutionized how we interact with devices, enhancing user experience across various platforms. One of the most significant developments in this arena is the OLED (Organic Light Emitting Diode) display, known for its vibrant colors, deep blacks, and flexibility. However, the efficiency and performance of OLED displays rely heavily on the adhesive used in their assembly. OLED display module adhesive ensures durability, optical clarity, and overall functionality. This article delves into the characteristics, applications, benefits, and considerations of OLED display module adhesives, highlighting their importance in modern technology.
Understanding OLED Technology
Before exploring the role of adhesives, it is essential to understand the fundamentals of OLED technology. OLED displays are composed of organic compounds that emit light when an electric current is applied. Unlike traditional LCDs, which require backlighting, OLEDs are self-emissive, providing several advantages, including:
- Enhanced Color Accuracy:OLED displays can produce a wider color gamut, creating more vivid and lifelike images.
- Better Contrast Ratios:Turning individual pixels off ultimately allows for true blacks and superior contrast.
- Thinner and Lighter Design: OLED technology enables slimmer devices, making them more portable and aesthetically pleasing.
- Wider Viewing Angles:OLED screens maintain color fidelity and brightness even at extreme angles.
While these advantages are significant, they also create unique challenges in manufacturing, particularly concerning adhesion.
The Role of Adhesive in OLED Display Modules
The adhesive is integral to OLED display modules for several reasons:
- Structural Integrity: Adhesives provide the necessary bonding strength between different display layers, ensuring they remain intact during operation and handling.
- Optical Clarity:High-quality adhesives enhance light transmission, minimizing reflections and distortions that can degrade the viewing experience.
- Environmental Protection:Adhesives act as a barrier against moisture and contaminants, safeguarding the display’s internal components from environmental damage.
- Thermal Management: Effective adhesives can help dissipate heat generated during operation, reducing the risk of thermal stress on the display components.
Types of OLED Display Module Adhesives
Various types of adhesives are used in OLED display modules, each with specific characteristics and applications. Understanding these types can help manufacturers choose the suitable adhesive for their needs:
1. Acrylic Adhesives
- Properties: Acrylic adhesives are known for their excellent clarity and UV resistance. They offer good bonding strength and are relatively easy to process.
- Applications:Acrylic adhesives are commonly used for laminating display panels and are ideal for applications where optical clarity is paramount.
2. Silicone Adhesives
- Properties: Silicone adhesives are highly flexible, durable, and resistant to extreme temperatures. They also offer good adhesion to a variety of substrates.
- Applications: Often used in applications requiring flexibility and durability, silicone adhesives are ideal for curved or flexible OLED displays.
3. Epoxy Adhesives
- Properties: Epoxy adhesives provide excellent mechanical strength and chemical resistance. They cure to form a rigid bond, offering strong adhesion.
- Applications: Epoxy adhesives are suitable for high-stress applications and often assemble components requiring high structural integrity.
4. Polyurethane Adhesives
- Properties: Polyurethane adhesives are known for their flexibility and impact resistance. They offer good adhesion to various materials and can withstand harsh environmental conditions.
- Applications: Polyurethane adhesives are often chosen for their durability in consumer electronics applications, requiring a balance between flexibility and strength.
5. Hot Melt Adhesives
- Properties: Hot melt adhesives are thermoplastic materials applied in a molten state. They cool quickly to form a solid bond.
- Applications:Hot melt adhesives are often used in fast production lines and are suitable for temporary bonding or applications requiring quick assembly.
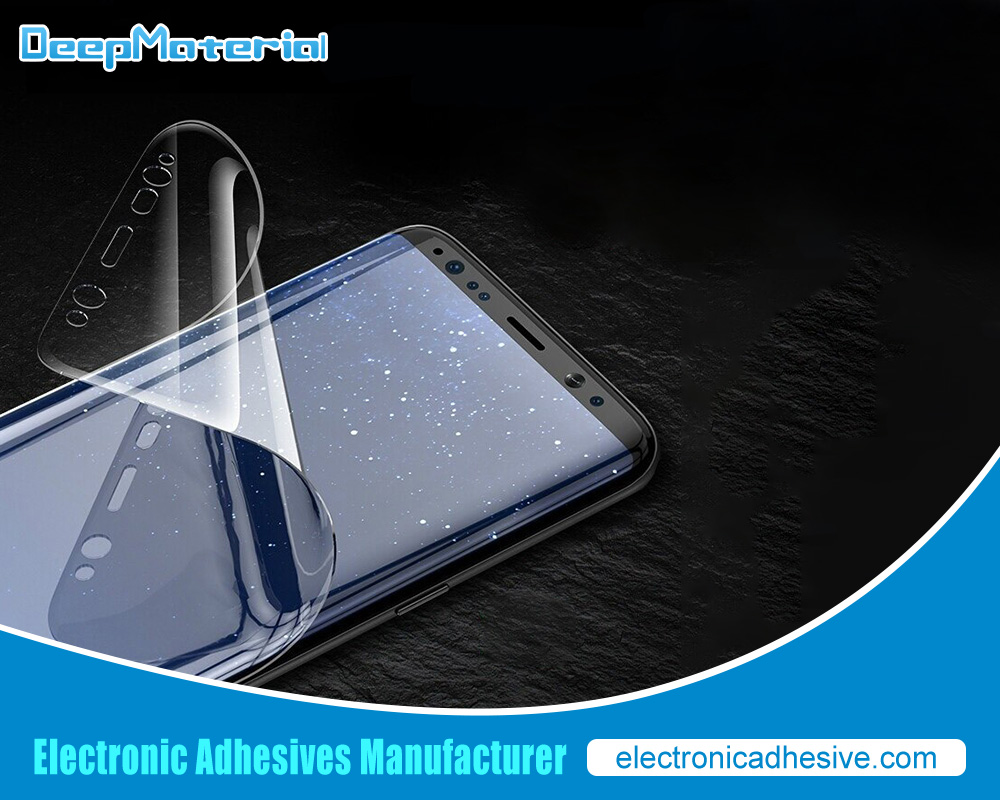
Key Benefits of Using OLED Display Module Adhesive
Utilizing the suitable adhesive in OLED display modules offers several advantages that contribute to the overall performance and longevity of the displays:
Improved Durability
- Resistance to Environmental Factors: High-quality adhesives protect against moisture, dust, and chemicals, which can extend the display’s lifespan.
- Enhanced Shock Resistance: Adhesives with excellent mechanical properties can absorb shocks and impacts, preventing damage to the display.
Enhanced Performance
- Optical Clarity: Choosing an adhesive with high optical clarity ensures the display maintains its vibrant colors and sharpness.
- Thermal Stability: Adhesives that can withstand high temperatures help maintain the performance of OLED displays even under demanding conditions.
Cost-Effectiveness
- Reduced Manufacturing Costs: Using efficient adhesives can streamline manufacturing, lowering production costs.
- Minimized Returns and Repairs:Displays with superior adhesive properties are less likely to fail, reducing warranty claims and associated costs.
Flexibility in Design
- Compatibility with Various Substrates: Different types of adhesives allow manufacturers to bond OLED displays to a wide range of materials, enabling innovative designs.
- Adaptability to Various Applications:Whether for consumer electronics, automotive displays, or industrial applications, the suitable adhesive can enhance the functionality of OLED displays across sectors.
Considerations When Choosing OLED Display Module Adhesives
Selecting the appropriate adhesive for OLED display modules involves several considerations to ensure optimal performance:
Bonding Strength
- Assessment of Material Compatibility: The bonding strength of the adhesive must be evaluated for the materials used in the display module.
- Testing Under Stress Conditions:Conducting tests to determine how the adhesive performs under various stress conditions can inform the selection process.
Optical Properties
- Transparency and Light Transmission:The adhesive must maintain high levels of transparency to ensure that the display’s color accuracy is not compromised.
- Refractive Index Matching:Adhesives with a refractive index similar to the display materials can minimize reflections and improve image quality.
Curing Time
- Impact on Production Efficiency: The adhesive’s curing time can significantly affect manufacturing. Fast-curing adhesives can improve throughput.
- Environmental Conditions:The curing method (e.g., heat or UV) must be considered to align with the production environment.
Environmental Resistance
- Durability Against Moisture and Chemicals: To protect the display, the adhesive must sufficiently resist moisture, chemicals, and temperature fluctuations.
- Testing for Reliability: Performing reliability tests can ensure that the adhesive can withstand the intended environmental conditions.
Innovations in OLED Display Module Adhesives
As technology continues to evolve, so do the adhesives used in OLED display modules. Recent innovations focus on enhancing performance, sustainability, and application versatility:
Sustainable Adhesives
- Biodegradable Options: With a growing emphasis on environmental sustainability, some manufacturers are developing biodegradable adhesives that reduce ecological impact.
- Recyclability: Adhesives that can be easily removed without damaging the display can facilitate recycling efforts.
Smart Adhesives
- Temperature and Humidity Indicators: Some modern adhesives incorporate features that change color or provide visual cues based on temperature or humidity, helping manufacturers monitor conditions during assembly.
- Self-Healing Properties: Research into self-healing adhesives aims to create materials that can recover from minor damages, extending the display’s life.
Advanced Bonding Technologies
- Laser Bonding Techniques: Innovative bonding techniques using lasers can improve the precision of adhesive application and reduce the risk of damage to sensitive display components.
- Pressure-Sensitive Adhesives: These adhesives allow easy repositioning and application, enhancing manufacturing.
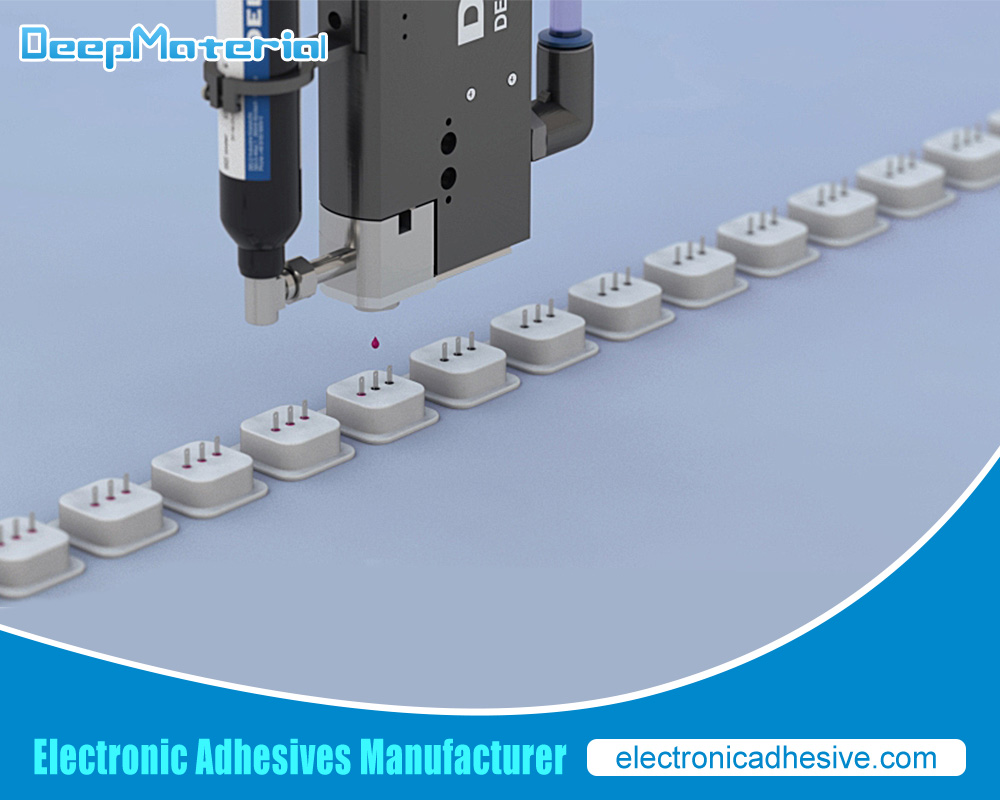
Conclusion
The significance of OLED display module adhesive cannot be overstated in today’s technology-driven world. As OLED displays become increasingly prevalent in various applications, from smartphones and televisions to automotive interfaces, the demand for reliable, high-performance adhesives continues to grow. The choice of adhesive influences not only the durability and optical quality of the display but also the overall user experience. As manufacturers innovate and improve adhesive technologies, the future of OLED displays looks promising, paving the way for even more advancements in display performance, sustainability, and design flexibility. Understanding and utilizing the suitable OLED display module adhesive is essential for harnessing the full potential of this transformative technology.
For more about choosing the importance of OLED display module adhesive in modern technology, you can pay a visit to DeepMaterial at https://www.electronicadhesive.com/ for more info.