Rubber Bonding Adhesive: Comprehensive Guide and Applications
Rubber Bonding Adhesive: Comprehensive Guide and Applications
Rubber bonding adhesives are crucial in various industries because they enable solid and durable bonds between rubber and other materials. Adhering rubber to substrates such as metals, plastics, glass, or fabric has revolutionised product design and efficiency in automotive, electronics, construction, and general manufacturing. This article delves into the types, features, applications, and best practices of rubber bonding adhesives.
Understanding Rubber Bonding Adhesives
Rubber bonding adhesives are designed to create strong adhesion between rubber and various substrates. Due to rubber’s flexibility, elasticity, and resilience, bonding requires adhesives with special properties. The challenge is to find an adhesive that can accommodate the movement and elasticity of rubber while providing a firm bond.
Characteristics of Rubber Adhesion
The unique characteristics of rubber bonding adhesives include:
- Elasticity and Flexibility: They must be able to stretch and contract with the rubber without losing their bond.
- Durability: Rubber adhesives must withstand environmental factors like moisture, temperature changes, and chemical exposure.
- Versatility: Rubber bonding adhesives can bond different types of rubber, including natural rubber, silicone rubber, nitrile rubber, and synthetic rubbers like EPDM.
Types of Rubber Bonding Adhesives
Rubber bonding adhesives can be classified into several types based on their formulation and bonding mechanism:
Contact Adhesives
These adhesives form bonds when both surfaces are coated and then pressed together. They are typically solvent-based, and evaporation of the solvent creates a sticky surface. Contact adhesives often bond rubber to metal or other non-porous surfaces.
- Advantages: Strong initial tack, quick drying, and high strength.
- Applications: Shoe soles, automotive gaskets, and conveyor belts.
Cyanoacrylate Adhesives (Super Glue)
Cyanoacrylates are well-known for their rapid bonding properties. When used for rubber bonding, they provide excellent adhesion, especially for smaller surfaces and quick fixes.
- Advantages: Fast curing, strong bond with minimal clamping.
- Applications: Electronics, small seals, and quick repairs.
Epoxy Adhesives
Epoxy adhesives are two-part systems that cure chemically to form a rigid bond. They are ideal for bonding rubber to rigid surfaces like metal or plastic and provide excellent resistance to environmental factors.
- Advantages: High strength, chemical resistance, and ability to bond dissimilar materials.
- Applications: Automotive parts, industrial machinery, and outdoor equipment.
Polyurethane Adhesives
Polyurethanes are flexible and highly durable, making them suitable for bonding rubber to various substrates. These adhesives remain flexible even after curing and can withstand multiple stresses.
- Advantages: Flexibility, weather resistance, and versatility.
- Applications: Windshields, footwear, and outdoor applications.
Silicone Adhesives
Silicone-based adhesives are advantageous when bonding silicone rubber. They provide excellent heat and chemical resistance and are commonly used in applications requiring flexibility at extreme temperatures.
- Advantages: Heat resistance, durability, and excellent bonding to silicone rubber.
- Applications: Automotive gaskets, aerospace components, and medical devices.
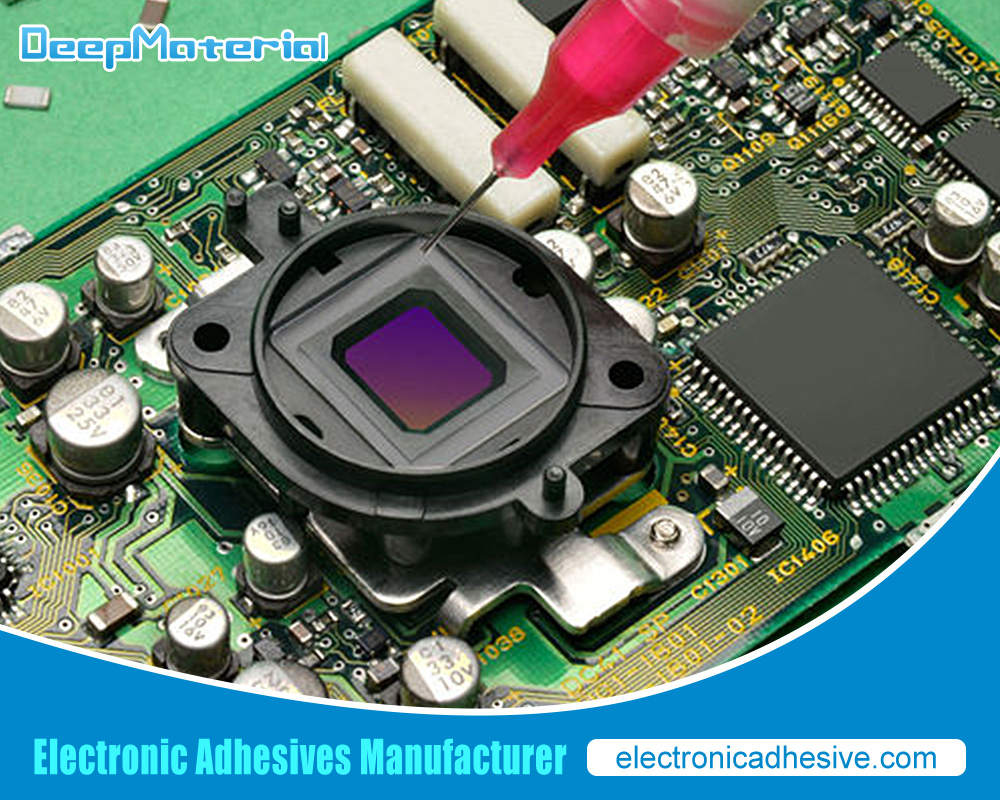
Application Techniques for Rubber Bonding Adhesives
Rubber bonding adhesives‘ effectiveness depends on the adhesive used and the application technique. Proper surface preparation, adhesive application, and curing are essential for a strong bond.
Surface Preparation
Before applying any adhesive, the surfaces to be bonded must be cleaned and prepared. Rubber, in particular, often contains release agents or surface contaminants that can weaken adhesion.
- Cleaning: Use solvents like acetone or isopropyl alcohol to clean the surfaces and remove oils, dirt, or grease.
- Abrasion: Lightly rub the rubber surface using sandpaper to improve mechanical adhesion. This is especially important for bonding to smooth surfaces.
- Priming: Some rubber adhesives require a primer to enhance adhesion. Primers create a thin layer that improves the bonding strength between the rubber and the adhesive.
Adhesive Application
- Contact Adhesives: Apply a thin, even adhesive layer to both surfaces. Allow it to dry until tacky before pressing the surfaces together.
- Cyanoacrylate Adhesives: Apply a small drop of adhesive to one surface and press the materials together immediately. Cyanoacrylates cure quickly, so precise application is essential.
- Epoxy and Polyurethane Adhesives: Mix the two components of the adhesive (resin and hardener) thoroughly before application. Apply to one or both surfaces and clamp them together during curing.
- Silicone Adhesives: Apply the adhesive to one surface and press the materials together. Silicone adhesives often require extended curing times, especially in areas with low humidity.
Curing
Different adhesives have varying curing times and conditions. For optimal bond strength, it is essential to follow the manufacturer’s instructions.
- Room Temperature Curing: Most adhesives cure at room temperature. The curing time can range from a few minutes (cyanoacrylates) to several hours (epoxies and polyurethanes).
- Heat Curing: Some adhesives require elevated temperatures to achieve full bond strength. Heat curing is commonly used for epoxy adhesives and provides additional strength.
- Humidity Curing: Silicone adhesives often require humidity to cure. Placing the bonded components in a humid environment can accelerate the curing process.
Common Applications of Rubber Bonding Adhesives
Rubber bonding adhesives have a wide range of applications across different industries due to their ability to bond rubber to various substrates. Below are some of the most common uses of these adhesives:
Automotive Industry
In the automotive sector, rubber bonding adhesives are used extensively to bond rubber to metal and plastic components. Rubber parts such as seals, gaskets, weatherstripping, and mounts need solid and flexible adhesives to ensure durability under stress, vibration, and exposure to elements.
- Windshields: Polyurethane adhesives are commonly used to bond rubber seals to car windshields, providing a strong bond that withstands outdoor conditions.
- Engine Mounts: Epoxy adhesives bond rubber components to metal engine parts, where they endure heat, oil, and vibration.
Electronics and Electrical Applications
Rubber bonding adhesives are essential in electronics and electrical applications, where they bond rubber components like gaskets, seals, and insulators to metal or plastic parts.
- Sealing Gaskets: Silicone adhesives are preferred for sealing electronic enclosures to protect against dust, moisture, and temperature fluctuations.
- Wire Insulation: Adhesives bond rubber insulation to electrical wires, protecting environmental factors.
Construction Industry
In construction, rubber bonding adhesives bond rubber membranes, flooring, and insulation to concrete, wood, and metal surfaces. The adhesives must withstand outdoor conditions, including moisture, UV exposure, and temperature changes.
- Roofing: Rubber bonding adhesives attach rubber membranes to roofs, providing waterproofing and durability.
- Flooring: Adhesives bond rubber tiles or mats to concrete or wooden floors in gyms, playgrounds, and industrial settings.
Footwear and Fashion
Rubber bonding adhesives are crucial in the footwear and fashion industry. They bond rubber soles to fabric or leather. The adhesives need to be flexible and resistant to wear and tear.
- Shoe Soles: Contact adhesives are commonly used to bond rubber soles to shoes, ensuring durability and flexibility.
- Leather and Fabric: Adhesives bond rubber to leather and fabric in accessories like bags and belts, where flexibility and strength are required.
Choosing the Right Rubber Bonding Adhesive
Selecting the suitable rubber bonding adhesive depends on several factors, including the type of rubber, the substrate, environmental conditions, and the specific application. Here are some considerations to help guide the selection process:
Type of Rubber
- Natural Rubber: Use highly flexible adhesives, such as polyurethane or contact adhesives.
- Silicone Rubber: Silicone adhesives or specially formulated cyanoacrylates best bond silicone rubber.
- Nitrile Rubber: Epoxy adhesives strongly bond with nitrile rubber, especially in applications exposed to oil or chemicals.
Substrate
- Metal: Epoxy and polyurethane adhesives are ideal for bonding rubber to metal due to their high strength and resistance to environmental factors.
- Plastic: Cyanoacrylates and contact adhesives work well for bonding rubber to plastic.
- Glass: Silicone adhesives are often used to bond rubber to glass, particularly in applications exposed to temperature changes.
Environmental Factors
Consider the operating environment when choosing an adhesive:
- Temperature: Use silicone adhesives for high-temperature applications, and avoid adhesives that may degrade at elevated temperatures.
- Moisture: Polyurethane and silicone adhesives offer excellent moisture resistance, making them suitable for outdoor or marine applications.
- Chemical Exposure: Epoxy adhesives provide good resistance to chemicals and oils, making them ideal for industrial applications.
Application Requirements
Consider the size, shape, and stress levels of the bonded components:
- Flexible Bonds: Use polyurethane or silicone adhesives for flexibility and movement applications.
- Rigid Bonds: Epoxy adhesives are better suited for rigid applications where strength is a priority.
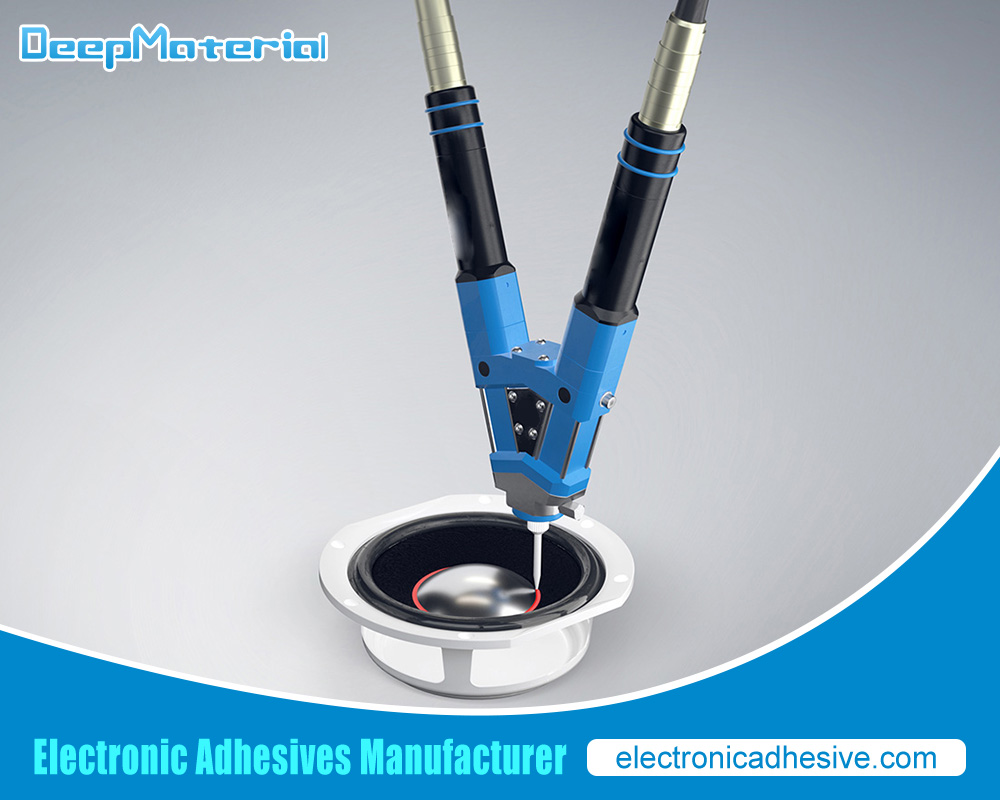
Conclusion
Rubber bonding adhesives are indispensable in modern manufacturing, providing strong, flexible, and durable bonds between rubber and various substrates. Whether in the automotive industry, electronics, construction, or footwear, these adhesives ensure products can withstand environmental stresses and maintain functionality. By understanding the different types of adhesives, their characteristics, and application techniques, users can select the suitable adhesive for their specific needs, ensuring long-lasting performance.
For more about choosing the top rubber bonding adhesive: comprehensive guide and applications, you can pay a visit to DeepMaterial at https://www.electronicadhesive.com/ for more info.