PCB Potting Compound: Comprehensive Guide
PCB Potting Compound: Comprehensive Guide
Printed Circuit Boards (PCBs) are fundamental components in virtually every electronic device, providing the structural platform for circuit assembly. As electronic devices become increasingly complex, protecting PCBs becomes crucial. One effective method for safeguarding these delicate components is using PCB potting compounds. This article provides a comprehensive overview of PCB potting compounds, their benefits, applications, types, and how they are used to protect electronic circuits.
What is PCB Potting Compound?
PCB potting compound is a protective insulating material applied to PCBs to encapsulate and shield them from various environmental hazards. The term “potting” comes from placing the PCB in a “pot” or mold, where the compound is poured to surround the electronic components. Once the compound cures and hardens, it creates a protective barrier around the PCB.
The primary function of potting compounds is to provide a layer of insulation and protection to the PCB, shielding it from external elements like moisture, dust, chemicals, and physical impacts. Potting compounds are widely used in various industries, including automotive, aerospace, consumer electronics, and medical devices.
Benefits of Using PCB Potting Compounds
The use of PCB potting compounds offers numerous advantages that help to enhance the performance and longevity of electronic devices. Some key benefits include:
Environmental Protection
Electronic devices are often exposed to harsh environmental conditions, such as high humidity, temperature fluctuations, and chemical exposure. PCB potting compounds act as a protective layer, preventing moisture, contaminants, and corrosive substances from penetrating the PCB and damaging sensitive components.
Improved Electrical Insulation
Potting compounds provide excellent electrical insulation, reducing the risk of short circuits or electrical failure. This is especially important in high-voltage applications, where proper insulation is critical to ensure safe and reliable operation.
Mechanical Stability
Potting compounds add mechanical strength to the PCB, protecting it from vibrations, shocks, and physical damage. This is essential in applications where electronic devices are subjected to mechanical stress, such as in automotive or aerospace environments.
Thermal Management
Heat is a byproduct of electronic device operation, and excessive heat can degrade PCB performance. Some potting compounds have thermal conductivity properties, which help dissipate heat away from critical components, preventing overheating and extending the device’s lifespan.
Tamper Resistance
In applications where security is a concern, potting compounds can deter PCB tampering or reverse engineering. Once the compound hardens, removing it without damaging the components is complex, making it challenging for unauthorized individuals to access the circuitry.
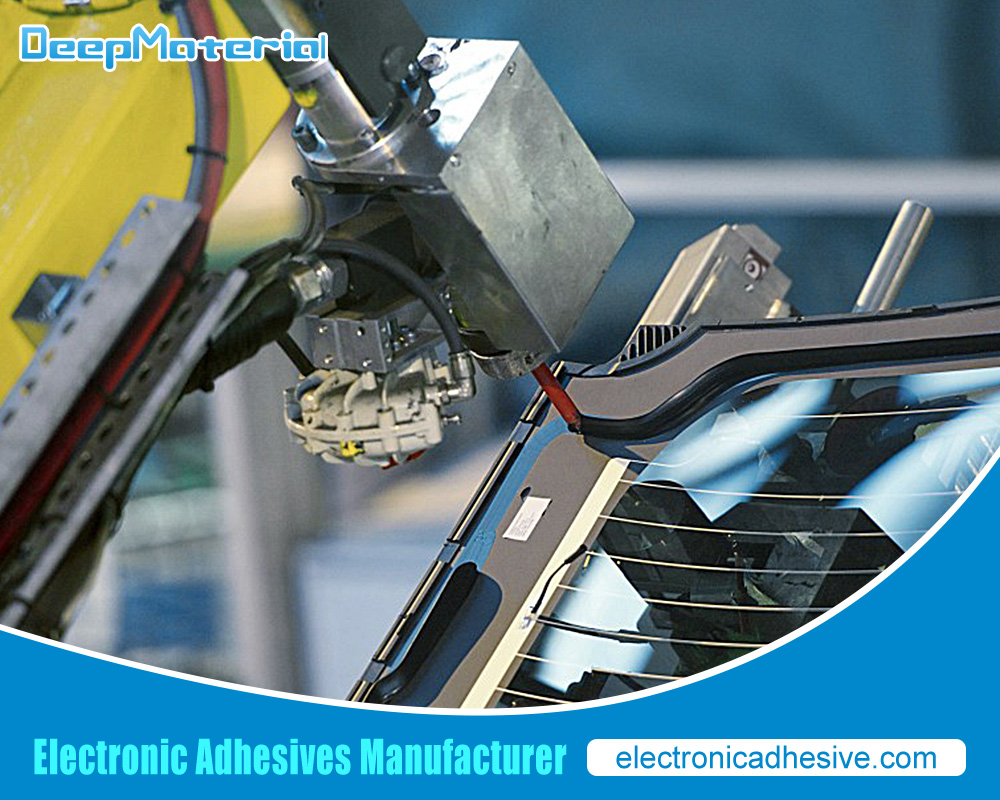
Types of PCB Potting Compounds
Several types of potting compounds are available, each with unique properties and suitability for different applications. The choice of potting compound depends on factors like environmental conditions, thermal requirements, and the specific needs of the PCB. Common types of PCB potting compounds include:
Epoxy Potting Compounds
Epoxy is one of the most commonly used potting compounds due to its excellent adhesion, durability, and chemical resistance. It forms a rigid, hard coating around the PCB, offering mechanical solid protection and electrical insulation. Epoxy compounds are well-suited for applications where the PCB may be exposed to harsh environmental conditions, such as chemicals or extreme temperatures.
However, once cured, epoxy compounds can be challenging to remove, making rework or repairs more difficult. Additionally, as epoxy is a relatively brittle material, it may not be ideal for flexible applications.
Polyurethane (PU) Potting Compounds
Polyurethane potting compounds are known for their flexibility and resilience. Unlike epoxy, polyurethane compounds remain somewhat elastic after curing, making them suitable for applications that involve frequent mechanical vibrations or thermal expansion and contraction. They also offer excellent moisture and chemical resistance.
Polyurethane compounds are often used in automotive and consumer electronics applications where flexibility and vibration resistance are essential. However, they may not provide the same level of mechanical strength as epoxy compounds, making them less suitable for highly demanding environments.
Silicone Potting Compounds
Silicone potting compounds are prized for their exceptional thermal stability and flexibility. They can withstand a wide range of shallow to high temperatures, making them ideal for applications requiring heat resistance and flexibility. Silicone compounds also have excellent electrical insulation properties and are resistant to moisture and chemicals.
Because of their flexibility and ability to remain stable at extreme temperatures, silicone potting compounds are commonly used in aerospace, automotive, and outdoor electronic applications. However, they can be more expensive than other potting compounds and may have longer curing times.
Acrylic Potting Compounds
Acrylic potting compounds offer fast curing times and good adhesion properties. They provide adequate protection against moisture and chemicals but may not have the same durability or mechanical strength as epoxy or silicone compounds. Acrylic compounds, such as consumer electronics, are often used in applications that require moderate protection and quick processing times.
Urethane-Modified Epoxy Compounds
Urethane-modified epoxy compounds combine the best of both worlds, offering epoxy’s mechanical strength and polyurethane’s flexibility. These compounds are designed to provide excellent protection in applications requiring rigidity and flexibility.
Applications of PCB Potting Compounds
Potting compounds are used in various industries and applications where PCBs require protection from environmental or operational stress. Some typical applications include:
Automotive Electronics
In the automotive industry, electronic control units (ECUs) and other PCBs are subjected to harsh conditions, including temperature fluctuations, vibrations, and exposure to chemicals like oils and coolants. Potting compounds protect these sensitive components and ensure reliable operation in demanding environments.
Aerospace Electronics
Aerospace applications require PCBs to withstand extreme temperatures, pressure changes, and mechanical stress. Potting compounds with high thermal stability and flexibility protect avionics and other critical electronics in aircraft and space vehicles.
Consumer Electronics
Potting compounds provide protection against moisture, dust, and physical damage in consumer electronics. Devices such as smartphones, laptops, and wearables often use potting compounds to enhance the durability and longevity of internal PCBs.
Medical Devices
Medical devices must be protected from moisture, bodily fluids, and other contaminants, especially those used in external or implantable applications. Potting compounds encapsulate and protect PCBs in medical devices, ensuring they function reliably in sterile or harsh environments.
Renewable Energy Systems
Renewable energy systems, such as solar panels and wind turbines, often operate outdoors where PCBs are exposed to extreme weather conditions. Potting compounds protect the PCBs in these systems from moisture, temperature changes, and other environmental hazards.
Application Process of PCB Potting Compounds
Applying potting compounds to a PCB involves several steps, and it is essential to follow the correct procedure to ensure proper protection. Here is an overview of the typical application process:
Preparation
Before applying the potting compound, the PCB must be thoroughly cleaned to remove dust, oils, or contaminants. This ensures good adhesion of the potting compound to the PCB’s surface. In some cases, a primer may be applied to improve adhesion.
Mixing
If the potting compound consists of two parts (such as epoxy or polyurethane), they must be mixed according to the manufacturer’s instructions. Accurate mixing is critical to achieving the desired properties of the cured compound.
Dispensing
The potting compound is then dispensed onto the PCB. Large-scaleThiscan can be done manually for large-scale production using syringes, dispensers, or automated dispensing machines. The compound should be applied evenly to cover all components on the PCB.
Curing
After the compound has been applied, it needs time to cure and harden. Curing times vary depending on the type of potting compound and environmental conditions, such as temperature and humidity. Some compounds cure at room temperature, while others may require heat curing in an oven.
Inspection
Once the compound has cured, the encapsulated PCB is inspected for any defects or air bubbles that may have formed during the potting process. Any issues should be addressed before the PCB is used in its final application.
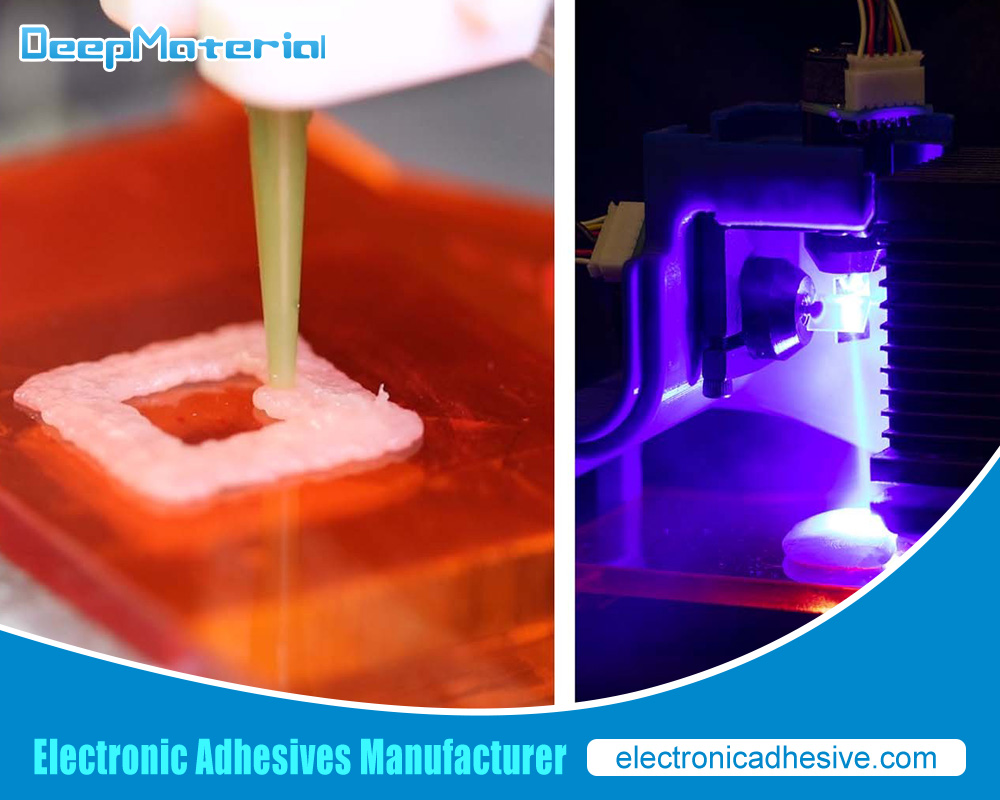
Conclusion
PCB potting compounds are essential to modern electronics manufacturing, providing critical protection for sensitive components in various industries and applications. Whether safeguarding against moisture, temperature extremes, mechanical stress, or tampering, potting compounds ensure electronic devices’ long-term reliability and performance. By selecting the correct type of potting compound and following the proper application process, manufacturers can enhance the durability and functionality of their products, ultimately leading to greater customer satisfaction and fewer device failures.
For more about choosing the top PCB potting compound: comprehensive guide, you can pay a visit to DeepMaterial at https://www.electronicadhesive.com/ for more info.