PCB Adhesive
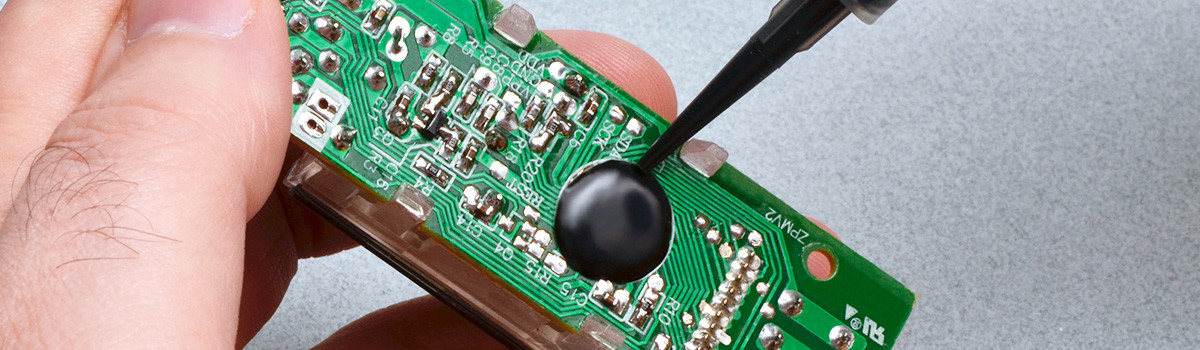
Printed Circuit Board (PCB) adhesive plays a crucial role in the assembly and reliability of electronic devices. It is a bonding agent that holds various components and layers of a PCB together, ensuring electrical connectivity, mechanical stability, and protection against environmental factors. This comprehensive guide provides a detailed overview of PCB adhesive, its types, applications, considerations, and best practices for successful implementation.
What is PCB Adhesive?
PCB adhesive, or printed circuit board adhesive, is a glue or bonding material used to assemble and manufacture printed circuit boards (PCBs). PCB adhesive is applied to bonds and specific components, such as surface-mount devices (SMDs) and through-hole components, to the PCB substrate.
PCB adhesives serve several purposes in the PCB assembly process. They provide mechanical support and help prevent components from loosening or becoming detached due to vibrations, shocks, or thermal cycling. Adhesives also enhance the electrical performance of the PCB by improving the grounding, reducing the impedance, and minimizing electromagnetic interference (EMI). Additionally, they protect against moisture, dust, and other contaminants.
Different types of PCB adhesives are available, and the selection depends on the specific requirements of the application and the components being bonded. Some common types of PCB adhesives include epoxy-based adhesives, acrylic-based adhesives, silicone-based adhesives, and polyurethane-based adhesives.
PCB adhesives are typically applied using automated dispensing systems or by manually applying the adhesive to specific areas of the PCB. After application, the bond is cured or hardened through a curing process, which may involve exposure to heat, UV light, or a combination of both, depending on the adhesive type.
Overall, PCB adhesives are crucial in ensuring printed circuit boards’ structural integrity, electrical performance, and reliability during their operation in various electronic devices and systems.
Types of PCB Adhesive
PCB adhesive refers to a type of glue used in the manufacturing and assembly of printed circuit boards (PCBs). PCB adhesives are used to bond components to the board’s surface and hold the different layers of the board together. Several types of PCB adhesive are available, each with unique characteristics and properties. This article will discuss some of the most common types of PCB adhesive.
- Epoxy Resin Adhesive: Epoxy resin adhesive is a two-part adhesive widely used in the electronics industry. It offers excellent adhesion, high strength, and good heat, chemicals, and moisture resistance. It is also easy to apply and cure, making it a popular choice for PCB assembly.
- Acrylic Adhesive: Acrylic adhesive is a single-component adhesive that offers good adhesion, excellent durability, and resistance to high temperatures. It is also easy to apply and cure and is widely used to assemble high-performance PCBs.
- Polyurethane Adhesive: Polyurethane adhesive is a two-component adhesive that offers excellent adhesion, high strength, and good resistance to heat, chemicals, and moisture. It is also highly resistant to mechanical stress and is often used to assemble heavy-duty PCBs.
- Silicone Adhesive: Silicone adhesive is a single-component adhesive that offers excellent adhesion, flexibility, and high-temperature resistance. It is also highly resistant to moisture and is often used to assemble PCBs exposed to harsh environmental conditions.
- Cyanoacrylate Adhesive: Cyanoacrylate adhesive is a single-component adhesive that offers fast curing times and excellent adhesion to various substrates. It is often used for bonding small components to the surface of the PCB.
Factors to Consider when Choosing PCB Adhesive
When choosing a PCB adhesive, several factors must be considered to ensure the adhesive is suitable for the specific application. Some of the critical factors to consider include:
- Electrical Conductivity: The glue used in PCBs should not have any electrical conductivity or leakage, as it can cause issues with the board’s performance. Thus, choosing an adhesive with a low electrical conductivity that can effectively insulate the conductive components is essential.
- Thermal Conductivity: PCBs generate a significant amount of heat, and it is necessary to have an adhesive that can effectively transfer the heat away from the components to prevent overheating. Therefore, selecting an adhesive with high thermal conductivity is crucial to ensure efficient heat dissipation.
- Mechanical Strength: PCBs can be subjected to significant mechanical stress during assembly and use, which can cause the adhesive to fail and components to become loose. Thus, it is essential to choose an adhesive with high mechanical strength that can withstand mechanical stress, such as vibrations, shocks, and temperature changes, to ensure the longevity of the PCB.
- Environmental Resistance: The adhesive used in PCBs must withstand harsh environmental conditions, such as moisture, humidity, and corrosive chemicals. Therefore, it is essential to select an adhesive with high ecological resistance that can protect the components and ensure the longevity of the PCB.
In addition to these factors, other considerations need to be considered, such as the curing time, viscosity, and ease of application. Therefore, it is essential to select an adhesive that can meet all the requirements of the specific application to ensure the performance and reliability of the PCB.
Surface Preparation for PCB Adhesive
Surface preparation is essential for successfully bonding between the Printed Circuit Board (PCB) and the adhesive. Adequate surface preparation is critical for a reliable and durable adhesive bond. Three commonly used surface preparation methods for PCB adhesive are cleaning and degreasing, surface roughening, and plasma treatment. In this answer, we will discuss these methods within 400 words.
- Cleaning and Degreasing:Cleaning and degreasing the PCB surface are the first and most crucial steps in surface preparation. Before applying the adhesive, the surface must be free of contaminants such as oils, dust, and debris. Any pollutants present on the surface can reduce the adhesive bond strength, cause poor wetting, and result in bond failure. The most common method of cleaning and degreasing the PCB surface is using isopropyl alcohol (IPA) or a specialized cleaning agent. The cleaning agent removes any unwanted contaminants from the surface and leaves it clean and ready for the next surface preparation step.
- Surface Roughening:Surface roughening is another method of preparing the PCB surface for adhesive bonding. The surface of the PCB is roughened by either mechanical abrasion or chemical etching. Roughening the surface increases the surface area of the PCB, allowing the adhesive to adhere more efficiently. A rougher surface also provides mechanical interlocking, which improves the bonding strength. The surface roughness should be within a specific range, as a too-rough character can lead to an uneven adhesive thickness, resulting in bond failure.
- Plasma Treatment:Plasma treatment is a surface preparation method that modifies the PCB surface by exposing it to low-pressure plasma. The plasma modifies the surface by introducing polar groups, increasing surface energy, and enhancing wetting. This method is particularly effective in preparing non-porous surfaces, such as polymers, for adhesive bonding. Plasma treatment is a dry and environmentally friendly process that produces uniform and predictable results, and it is also a quick process. It can be easily integrated into the PCB manufacturing process.
Application Methods for PCB Adhesive
The application method used for PCB adhesive is crucial in achieving a reliable and uniform bond between the adhesive and the PCB. The four commonly used methods for applying adhesive to a PCB are screen printing, dispensing, stenciling, and bonding films. Each method has its advantages and disadvantages, and the choice of method depends on the specific requirements of the adhesive and the PCB.
- Screen Printing:Screen printing is a popular method for applying adhesive to a PCB. In this method, the adhesive is applied through a stencil onto the surface of the PCB. The stencil is made of mesh material with a pattern that matches the adhesive application area. The adhesive is then placed on the stencil and pushed through the mesh onto the PCB surface with a squeegee. Screen printing allows for high-volume production and is suitable for producing PCBs with a large surface area. However, screen printing requires high setup costs, and the stencil needs to be replaced frequently.
- Dispensing:Dispensing is a flexible method for applying adhesive to a PCB. It involves using a dispensing machine that dispenses the adhesive in a controlled manner onto the surface of the PCB. The dispensing device can be programmed to dispense the adhesive in specific patterns and thicknesses. Dispensing is suitable for producing small batches of PCBs and applying high-viscosity sealants. However, dispensing requires high setup costs, and the adhesive thickness can be challenging to control.
- Stenciling:Stenciling is a method of applying adhesive to a PCB similar to screen printing. However, the stencil used in stenciling is made of a rigid material, such as metal or plastic. The adhesive is applied to the stencil, which is then placed onto the surface of the PCB. The adhesive is then pushed through the openings in the stencil onto the PCB surface. Stenciling is suitable for producing PCBs with a small surface area and applying low-viscosity sealants. However, stenciling requires a high setup cost, and the stencil needs to be replaced frequently.
- Bonding Films:Bonding films are pre-cut adhesive sheets applied to the PCB’s surface. The bonding film is placed onto the PCB surface and then heated to activate the adhesive. Bonding films are suitable for producing PCBs with complex shapes and applying low-viscosity sealants. Bonding films do not require any setup costs, and the adhesive thickness can be precisely controlled. However, bonding films can be challenging for PCBs with uneven surfaces.
Curing and Drying Processes
Curing and drying processes are essential in various industries to transform raw materials into finished products. These processes involve the application of heat, ultraviolet (UV) light, or moisture to initiate chemical reactions that result in the hardening or solidification of the material. This response will explore three standard curing and drying processes: heat, UV, and moisture.
- Heat Curing: Heat curing is a process that involves applying heat to a material to accelerate the chemical reaction and drying process. This method is commonly used in coatings, adhesives, and composites. The heat increases the evaporation rate, enabling the solvent or moisture in the material to escape quickly. As a result, the material solidifies or hardens.
The temperature and duration of heat curing depend on the specific material and its desired properties. For example, heat curing is used in the automotive industry to produce painted car bodies. The painted surfaces are heated in large ovens to promote solvent evaporation and ensure a durable and glossy finish.
- UV Curing: UV curing is a process that utilizes ultraviolet light to initiate a photochemical reaction that leads to the curing or drying of the material. It is widely used in printing, coatings, and electronics applications. UV-curable materials contain photoactive substances known as photoinitiators that react when exposed to UV light.
When the UV light hits the photoinitiator, it triggers a chain reaction, leading to the polymerization or cross-linking of the material. This process occurs almost instantly, resulting in rapid curing. UV curing offers advantages such as high-speed production, reduced energy consumption, and the ability to cure thin layers. However, it requires specialized equipment and materials sensitive to UV light.
- Moisture Curing:Moisture curing is a process that involves the absorption of moisture from the surrounding environment to initiate the curing and drying of the material. It is commonly used in adhesives, sealants, and coatings. Moisture-curable materials contain reactive functional groups that react with water vapor, triggering chemical reactions that lead to curing.
When the material absorbs moisture, it undergoes a series of reactions, including hydrolysis and condensation, resulting in the formation of cross-links and the hardening of the material. Moisture curing offers the advantage of simplicity, as it does not require additional equipment or external energy sources; however, it requires a controlled environment with adequate humidity levels for optimal curing.
In summary, heat, UV, and moisture curing are three standard processes used to cure and dry materials in various industries. Each method has its advantages and considerations, and the selection depends on factors such as material properties, desired curing speed, and production requirements. These processes are crucial in achieving the finished products’ desired performance and characteristics.
PCB Adhesive for Component Bonding
PCB adhesive is a crucial component of the printed circuit board (PCB) assembly used for component bonding. There are different types of PCB adhesive available in the market, and the choice of adhesive depends on the kind of technology used for component bonding, such as surface mount technology (SMT), through-hole technology (THT), and wire bonding.
- Surface Mount Technology (SMT):SMT is a popular technology used in PCB assembly where the components are directly mounted on the surface of the PCB. The adhesive used for SMT component bonding should have good thermal stability and high-temperature resistance to withstand the reflow process. The adhesive should also have excellent adhesion properties to bond the component to the PCB surface and prevent it from falling off during assembly.
The most commonly used adhesive for SMT is epoxy adhesive. Epoxy adhesive is a two-part adhesive that cures when mixed with a hardener. It has excellent bonding properties and high-temperature resistance, making it ideal for SMT component bonding.
- Through-Hole Technology (THT):THT is used in PCB assembly where the components are mounted through holes in the PCB. The adhesive used for THT component bonding should have good adhesion properties to hold the component in place during the assembly process. The adhesive should also be able to fill any gaps between the component and the PCB to ensure a secure bond.
The most commonly used adhesive for THT is cyanoacrylate adhesive. Cyanoacrylate is a fast-curing adhesive that forms a strong bond between the component and the PCB surface. It also has good gap-filling properties, making it ideal for THT component bonding.
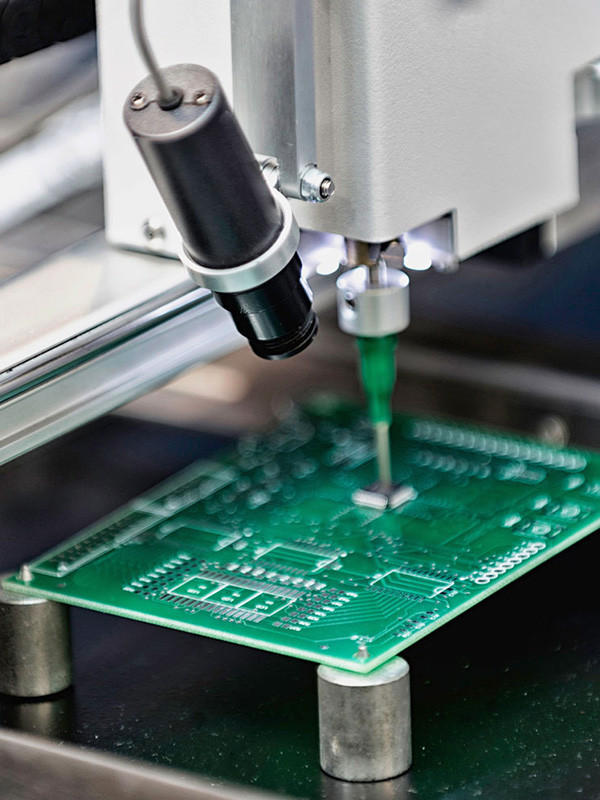
- Wire Bonding:Wire bonding is a technology that connects the component leads to the PCB surface using fine wires. The adhesive used for wire bonding should have good adhesion properties to hold the wire in place during the bonding process. The adhesive should also be able to withstand the stress caused by the wire during the operation of the PCB.
The most commonly used adhesive for wire bonding is epoxy adhesive. The epoxy adhesive has excellent adhesion properties and can withstand the stress caused by the wire during the operation of the PCB. It is also compatible with most wire-bonding machines used in PCB assembly.
PCB Adhesive for Encapsulation and Potting
PCB (Printed Circuit Board) adhesive is used for encapsulating and potting PCBs. Encapsulation refers to covering the PCB with a protective material layer to shield it from moisture, dust, and other contaminants. In contrast, potting refers to filling the internal cavities of the PCB with a material that provides mechanical support and enhances its durability. This response will discuss how PCB adhesive can help achieve these two goals: protection from moisture and contaminants and improving mechanical strength.
Protection from Moisture and Contaminants
PCBs are highly sensitive to moisture and contaminants. When exposed to water, PCBs can suffer from corrosion and degradation of the conductive traces, leading to malfunctions or even device failure. Contaminants such as dust, dirt, and other particles can also interfere with the operation of the PCB by causing short circuits and other electrical problems. PCB adhesive can help protect against these issues by creating a barrier between the PCB and its environment.
Several types of PCB adhesive can be used for encapsulation, including silicone, epoxy, and polyurethane. These materials are highly resistant to moisture and contaminants and can withstand various temperatures, making them ideal for use in harsh environments.
Silicone adhesives are a popular choice for PCB encapsulation because they are highly flexible and can conform to the shape of the PCB. They are also resistant to moisture and contaminants, making them ideal for use in applications where the PCB is exposed to harsh conditions.
Epoxy adhesives are another option for PCB encapsulation; they are highly resistant to moisture and contaminants and can also provide excellent mechanical support for the PCB. Epoxy adhesives can also be formulated to provide high thermal conductivity, making them ideal for applications where heat dissipation is a concern.
Enhancing Mechanical Strength
In addition to protecting from moisture and contaminants, PCB adhesive can also enhance the mechanical strength of the PCB. Potting the PCB with adhesive can help distribute stresses evenly throughout the device, reducing the likelihood of mechanical failure.
When choosing a PCB adhesive for potting, it is essential to consider the material properties of the adhesive. The adhesive should have a high strength-to-weight ratio, be resistant to thermal cycling and other environmental stresses, and be able to bond well to the PCB substrate.
Epoxy adhesives are popular for PCB potting because they provide excellent mechanical strength and durability. They can also be formulated to have a low coefficient of thermal expansion, which helps to reduce the stresses caused by temperature changes.
Reliability and Longevity Considerations
Reliability and longevity are critical considerations when designing and developing products, particularly for applications that require durability and longevity in harsh environments. Temperature, humidity, chemical exposure, and thermal cycling are some of the factors that can affect the reliability and longevity of a product.
- Temperature and humidity endurance:Temperature and humidity are two of the most significant factors that can impact the performance and lifespan of a product. High temperatures and humidity can cause components to deteriorate, corrode, or malfunction, reducing reliability and lifespan. To ensure that a product can withstand harsh temperatures and humidity, manufacturers must carefully select materials and components that can withstand these conditions.
For example, electronic components like resistors, capacitors, and transistors are typically rated for specific temperature ranges. When designing electronic systems that will operate in harsh environments, it’s critical to ensure that all components used in the system are rated to work within the expected temperature range. Additionally, manufacturers must use materials that can withstand high humidity levels, such as coatings and sealants that prevent moisture from penetrating the product’s components.
- Chemical resistance:Chemical exposure is another factor that can significantly impact a product’s reliability and longevity. Exposure to harsh chemicals can cause corrosion, deterioration, and damage to components, leading to system failure. To ensure that a product can withstand chemical exposure, manufacturers must select materials resistant to the specific chemicals the product is likely to encounter.
For example, products used in the chemical processing industry must be made from materials that can withstand exposure to corrosive chemicals. Stainless steel and titanium are two common materials used in the construction of chemical processing equipment due to their chemical resistance properties.
- Thermal cycling resistance: Thermal cycling occurs when a product is subjected to rapid temperature changes, causing the material to expand and contract. This can cause stress on the product’s components and lead to failure over time. Manufacturers must select materials that can withstand the expansion and contraction caused by rapid temperature changes to ensure that a product can withstand thermal cycling.
For example, products used in the aerospace industry must be designed to withstand extreme temperature fluctuations during takeoff and reentry. Materials like carbon composites and titanium alloys are commonly used in the construction of aerospace products due to their thermal cycling resistance properties.
PCB Adhesive Testing and Quality Control
PCB adhesive testing and quality control are critical steps in the production process to ensure that the adhesive used in the assembly of printed circuit boards (PCBs) meets the required standards for reliability and durability. Several types of tests can be performed to evaluate the quality and performance of PCB adhesives, including shear and peel strength tests, accelerated aging tests, and electrical insulation resistance tests.
- Shear and Peel Strength Tests: Shear and peel strength tests commonly evaluate the bonding strength between the adhesive and the PCB substrate. These tests involve subjecting the bonded materials to a tensile force and measuring the force required to cause the bond to fail.
Shear strength tests involve applying a force perpendicular to the plane of the adhesive bond, while peel strength tests involve using a force parallel to the plane of the adhesive bond. Both tests provide critical information about the strength and durability of the adhesive bond, which is essential to ensure the reliability and longevity of the PCB.
- Accelerated Aging Tests:Accelerated aging tests involve subjecting the adhesive bond to accelerated environmental conditions, such as high temperature and humidity, to simulate the effects of long-term exposure to harsh environments. These tests are used to evaluate the adhesive bond’s long-term durability and reliability and identify any potential weaknesses or failure modes that may develop over time.
Accelerated aging tests can help manufacturers identify potential issues with the adhesive bond before they occur in the field, allowing them to make design modifications or select alternative adhesives that better meet the performance requirements.
- Electrical Insulation Resistance:Electrical insulation resistance testing involves measuring the resistance of the adhesive bond to electrical current flow. This test is critical to ensure that the adhesive bond does not become a conductive path between the conductive elements on the PCB, which could cause short circuits and other electrical failures.
A voltage is applied across the adhesive bond to perform the test, and the current flow is measured. The insulation resistance is calculated based on the current flow and the applied voltage. If the insulation resistance is too low, it indicates that the adhesive bond is conductive and may cause electrical issues.
Common Challenges and Troubleshooting
Printed circuit board (PCB) assembly involves adhesives to bond various components and materials. However, like any other manufacturing process, adhesive bonding can encounter several challenges and issues that can impact the quality and reliability of the finished product. Here are three common challenges and troubleshooting techniques in adhesive bonding for PCB assembly:
- Adhesive Dispensing Issues:Adhesive dispensing issues are a common problem encountered in PCB assembly. These issues can result from various factors, including improper equipment calibration, clogged nozzles, or inconsistent adhesive viscosity. When sticky dispensing issues occur, it can lead to insufficient or excessive adhesive application, which can cause bond failure or delamination.
To troubleshoot adhesive dispensing issues, manufacturers should carefully review their adhesive dispensing equipment and processes to identify the root cause of the problem. They may need to recalibrate equipment, replace clogged nozzles, or adjust adhesive viscosity to ensure consistent and proper application.
- Incomplete Curing:Incomplete curing is another common challenge in adhesive bonding for PCB assembly. Incomplete curing occurs when the adhesive does not fully cure, leading to insufficient bond strength and durability. Factors contributing to incomplete curing include inadequate cure time, low temperature, or humidity control.
To troubleshoot incomplete curing, manufacturers should review their adhesive curing process to ensure the adhesive is exposed to the appropriate temperature and humidity for the required cure time. Manufacturers may also need to adjust their curing process by increasing cure time or temperature to ensure the adhesive fully cures.
- Delamination or Bond Failure:Delamination or bond failure is a common challenge in PCB assembly. Delamination or bond failure occurs when the adhesive bond between two materials fails, separating the materials. This can be caused by poor surface preparation, insufficient adhesive application, or exposure to harsh environmental conditions.
Manufacturers should review their adhesive bonding process to troubleshoot delamination or bond failure to identify potential weaknesses or failure modes. This may involve improving surface preparation techniques, increasing adhesive application, or selecting alternative adhesives that better meet the performance requirements.
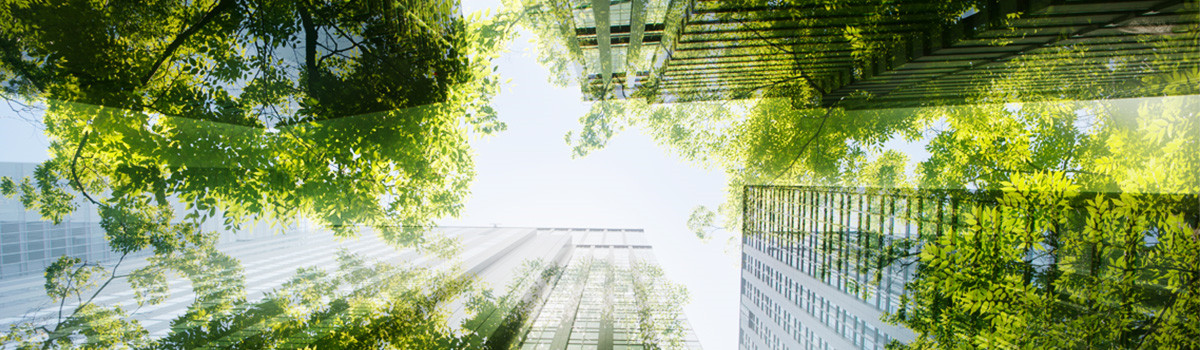
Environmental and Safety Considerations
Environmental and safety considerations are critical in the printed circuit board (PCB) assembly process. PCB assembly involves hazardous materials and can have ecological impacts if proper handling and disposal procedures are not followed. Additionally, workers involved in the PCB assembly process may be exposed to hazardous materials and chemicals, making it essential to take safety precautions. Here are three environmental and safety considerations in PCB assembly:
- Hazardous Materials and Handling:The PCB assembly process often involves using hazardous materials such as adhesives, solvents, and chemicals. If improperly handled, these materials can pose a significant risk to workers and the environment. For example, solvents and chemicals can be flammable or toxic, while adhesives can cause skin irritation or allergic reactions.
To mitigate the risks associated with hazardous materials, manufacturers should ensure that workers receive proper training on handling and disposing of these materials. Manufacturers should also provide workers with personal protective equipment such as gloves, safety glasses, and respirators. Proper labeling and storage of hazardous materials and regular monitoring of air quality in the workplace can also help reduce exposure risk.
- Environmental Regulations: Environmental regulations related to PCB assembly vary depending on the manufacturer’s location and the regulations in place. However, it is essential to comply with all applicable laws to minimize the environmental impact of the PCB assembly process. For example, laws may require the proper handling and disposal of hazardous materials, the reduction of air and water pollution, and the use of environmentally friendly materials.
To comply with environmental regulations, manufacturers should develop an environmental management plan that outlines the environmental impact of their PCB assembly process and the steps taken to minimize this impact. The program should also include regular monitoring and reporting to ensure the manufacturer complies with all applicable regulations.
- Worker Safety Precautions: Workers involved in PCB assembly can be exposed to hazardous materials and chemicals, making it essential to take safety precautions. In addition to providing workers with personal protective equipment, manufacturers should also offer regular training on handling and disposing of hazardous materials.
Other safety precautions that can be taken include implementing safety protocols and procedures, such as emergency response plans and fire prevention measures. Regular monitoring of air quality and noise levels in the workplace helps identify potential hazards and reduce the risk of exposure.
Advancements in PCB Adhesive Technology
Advancements in printed circuit board (PCB) adhesive technology have led to the development of new formulations that offer improved performance, durability, and environmental benefits. Here are three notable advancements in PCB adhesive technology:
- Low-VOC and Eco-friendly Formulations:Low-VOC and eco-friendly adhesives have become increasingly popular in PCB assembly due to their reduced environmental and human health impact. These adhesives are formulated to emit fewer volatile organic compounds (VOCs) during manufacturing, reducing the potential for air pollution and harmful health effects.
Low-VOC adhesives can be made from various materials, including water-based polymers, bio-based resins, and silicone. These adhesives can offer comparable or even superior performance to traditional solvent-based adhesives, making them a desirable option for manufacturers looking to improve the environmental impact of their PCB assembly process.
- Conductive Adhesives:Conductive adhesives can conduct electricity, making them ideal for use in PCB assembly. Conductive adhesives can bond electrical components and circuitry to the PCB, replacing traditional soldering methods. These adhesives can be formulated to offer excellent conductivity, good adhesion strength, and resistance to temperature and humidity.
Conductive adhesives can be made from various materials, including conductive polymers, metallic particles, and carbon nanotubes. These materials are typically mixed with a binder and solvent to form the adhesive. Conductive adhesives can offer several advantages over traditional soldering methods, including reduced assembly time and cost, improved reliability, and increased design flexibility.
- Nanocomposite Adhesives: Nanocomposite adhesives are a relatively new development in PCB adhesive technology. These adhesives are formulated using nanoparticles, which can offer superior performance and durability compared to traditional adhesives. Nanoparticles can be added to the adhesive matrix to improve mechanical strength, thermal stability, and electrical conductivity.
Nanocomposite adhesives can be formulated using a variety of nanoparticles, including graphene, carbon nanotubes, and metal oxides. These nanoparticles can be mixed with a binder and solvent to form the adhesive. Nanocomposite adhesives can offer several benefits over traditional adhesives, including improved performance, reduced weight and size, and increased design flexibility.
PCB Adhesive Removal and Reworking
When removing or reworking PCB adhesives, there are two main methods: solvent-based and thermal. Each method has its advantages and disadvantages, and the choice of method will depend on several factors, such as the type of adhesive, the substrate material, and the desired level of rework.
- Solvent-based Methods:Solvent-based methods involve using a chemical solvent to dissolve the adhesive, making it easier to remove or rework. The type of solvent used will depend on the adhesive removed. For example, acetone is commonly used to remove acrylic adhesives, while methylene chloride is used for epoxy adhesives.
Solvent-based methods can effectively remove adhesives quickly and easily, especially for large areas. However, these methods can harm the environment and human health, as many solvents are toxic and emit volatile organic compounds (VOCs) into the air. Special care and protective equipment must be used when handling these solvents.
- Thermal Methods: Thermal methods use heat to soften the adhesive, making it easier to remove or rework. This can be done using a heat gun, a soldering iron, or a hot air pencil. The heat must be carefully controlled to prevent damage to the PCB or components.
Thermal methods can effectively remove small areas of adhesive, such as around components or traces. It can also be used for removing specific types of bonds that are resistant to solvents. However, this method can be time-consuming and requires high skill and precision to avoid damaging the PCB or components.
Industry-Specific Applications
Consumer Electronics: Consumer electronics refer to a wide range of electronic devices intended for daily use by consumers. These devices include smartphones, laptops, televisions, home appliances, and wearables. Industry-specific applications of consumer electronics include:
- Smart Home Technology: Smart home technology is rapidly gaining popularity, and consumer electronics are at the forefront of this trend. Smart home devices, such as intelligent thermostats, bright lighting, and smart speakers, can be controlled remotely using a smartphone or voice commands.
- Virtual Reality: Consumer electronics, particularly smartphones and gaming consoles, have enabled the growth of virtual reality technology. Virtual reality is being used for entertainment, gaming, and training purposes.
- Wearable Technology: Wearable technology includes smartwatches, fitness trackers, and smart glasses. These devices have become increasingly popular and have fitness, health monitoring, and even fashion applications.
Automotive Electronics: Automotive electronics refer to electronic systems used in automobiles, such as infotainment systems, safety systems, and engine control units. Industry-specific applications of automotive electronics include:
- Autonomous Driving: The development of autonomous driving technology is heavily reliant on automotive electronics. Sensors, cameras, and other electronic systems help self-driving cars navigate roads safely.
- Infotainment Systems: Infotainment systems, such as touchscreens and voice-activated controls, have become a standard feature in modern cars. These systems allow drivers to control music, navigation, and other elements while driving.
- Advanced Safety Systems: Automotive electronics are also being used to develop advanced safety systems such as collision avoidance and lane departure warning systems. These systems use sensors and cameras to monitor the environment around the vehicle and alert drivers of potential hazards.
Aerospace and Defense: Aerospace and defense industries rely heavily on electronic systems for communication, navigation, and weapon systems. Industry-specific applications of aerospace and defense electronics include:
- Communication Systems: Electronic communication systems are essential for aerospace and defense operations. Satellites, radios, and other communication systems allow military personnel to communicate with each other across vast distances.
- Navigation Systems: Aerospace and defense electronics are also used to develop navigation systems for aircraft and missiles. These systems use GPS, radar, and other sensors to help pilots navigate difficult conditions.
- Weapon Systems: Electronic systems are used extensively in developing weapon systems, such as guided missiles and uncrewed aerial vehicles. These systems rely on sensors, cameras, and other electronic components to locate targets and guide weapons to their destination.
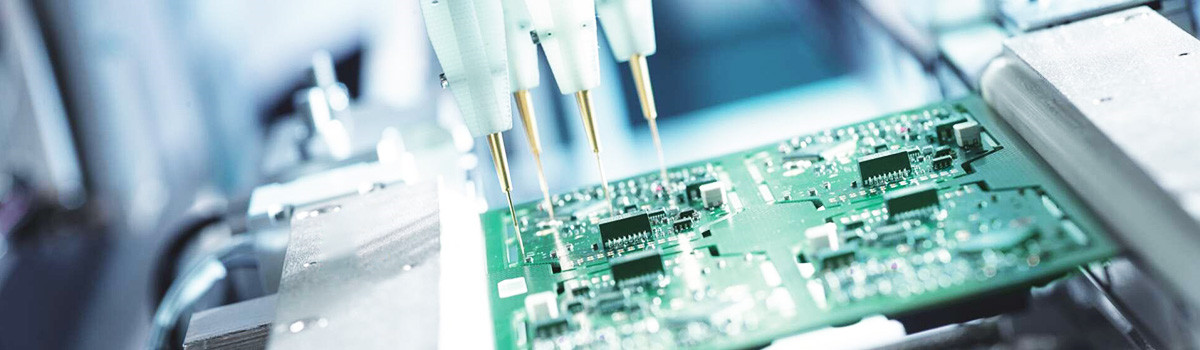
Future Trends in PCB Adhesive
Printed Circuit Boards (PCBs) have been a critical component of electronic devices since their inception. They are the foundation upon which electronic components are mounted, and their reliability is crucial to the device’s performance. The adhesive used in PCBs is essential to ensure the device’s reliability. In recent years, there has been a trend towards miniaturization, higher component density, improved thermal management, and flexible and stretchable adhesives.
- Miniaturization and Higher Component Density
With the rise of smart and portable devices, there has been a demand for smaller and more compact electronic components. This trend has resulted in the miniaturization of PCBs and a higher component density. To achieve this, manufacturers have had to design smaller electronic components, which means that the adhesive used in PCBs must also be smaller and thinner.
One solution to this problem is the use of epoxy-based adhesives. Epoxy adhesives are known for their high strength and excellent adhesion properties, and they are also available in various formulations customized to suit specific applications. Epoxy adhesives can be applied in thin layers, making them ideal for miniaturized PCBs.
- Improved Thermal Management
The performance of electronic devices is affected by heat generated during operation, and heat can damage the components, reduce their lifespan, and affect the device’s performance. Therefore, thermal management is a critical consideration in PCB design.
To address this issue, manufacturers are using thermally conductive adhesives. These adhesives have a high thermal conductivity, which allows heat to dissipate quickly. This helps reduce the electronic components’ temperature and improve their performance. Thermally conductive adhesives are also used in applications with temperature fluctuations, such as automotive and aerospace electronics.
- Flexible and Stretchable Adhesives
The demand for flexible and stretchable electronic devices has increased in recent years. These devices can be integrated into clothing, medical devices, and other applications where flexibility and stretchability are essential. To achieve this, manufacturers are using flexible and stretchable adhesives in PCBs.
Flexible and stretchable adhesives are typically made from silicone or acrylic materials, which can be stretched and bent without breaking or losing their adhesive properties. They also resist temperature changes, making them ideal for various applications.
Cost Considerations in PCB Adhesive Selection
There are several cost considerations when selecting an adhesive for printed circuit boards (PCBs). These costs can be broken down into material, application, reliability, and maintenance costs.
Material Costs
The material cost of an adhesive is the price of the adhesive itself. Different types of adhesives have different material costs. For example, some epoxy adhesives can be more expensive than acrylic adhesives. It is essential to consider the material price of a bond when selecting it for a PCB, as it can significantly impact the overall cost of the PCB.
Application Costs
The application cost of an adhesive is the cost of applying the adhesive to the PCB. This can include the cost of equipment, labor, and any other associated costs. Different types of bonds may require additional application methods. For example, some bonds may require a unique applicator or curing process, which can add to the overall application cost. It is essential to consider the application cost of a bond when selecting it for a PCB, as it can significantly impact the overall cost of the PCB.
Reliability and Maintenance Costs
An adhesive’s reliability and maintenance cost is the cost associated with maintaining the adhesive over time. This can include the cost of repairs or replacements if the adhesive fails and the cost of any maintenance required to keep the adhesive functioning properly. Different types of bonds may have different reliability levels and require additional maintenance. For example, some adhesives may be more prone to failure than others, resulting in higher reliability and maintenance costs. It is essential to consider the reliability and maintenance cost of an adhesive when selecting it for a PCB, as it can significantly impact the overall cost of the PCB over its lifespan.
Best Practices for PCB Adhesive Application
PCB adhesive application is a critical process in the electronics manufacturing industry, and proper adhesive application is crucial to ensure a reliable and durable electronic product. The following are best practices for PCB adhesive application:
Proper Storage and Handling: Adhesives must be stored in the manufacturer’s recommended conditions. Improper storage can cause the adhesive to harden, lose its properties, or separate into components. Therefore, following the recommended temperature, humidity, and shelf life instructions are essential. Adhesives should be kept in a dry, calm, dark environment to prevent degradation and contamination. The adhesive container should be closed tightly after use and kept away from direct sunlight, heat, and moisture.
Adhesive Mixing and Dispensing Techniques: Adhesive mixing and dispensing should be done carefully to ensure the adhesive is uniformly mixed and dispensed. Adhesive mixing ratios and times should be followed as recommended by the manufacturer. It is essential to use the right equipment, such as a scale and a mixer, and to follow the manufacturer’s instructions carefully. The adhesive should be mixed until it is homogeneous and no streaks are visible. After mixing, the bond should be dispensed onto the substrate immediately to prevent it from hardening.
Adequate Curing and Drying Conditions: Adhesive curing and drying are crucial for the adhesion of the components. The curing, drying time, and temperature should be based on the manufacturer’s recommendations. The curing temperature and humidity should be controlled to ensure the adhesive is adequately cured. There needs to be more curing time to lead to good adhesion while over-curing can cause the adhesive to become brittle and lose its properties. The drying process should also be controlled to ensure the adhesive dries uniformly and without bubbles or defects. The drying temperature and humidity should be based on the manufacturer’s recommendations.
Case Studies and Success Stories
- Applications in High-Frequency PCBs:
High-frequency printed circuit boards (PCBs) are crucial components in various electronic devices, especially those operating in the radio frequency (RF) and microwave frequency range. These PCBs are designed to handle high-speed digital, RF, and microwave signals with minimal loss and interference. Here are a few case studies and success stories showcasing the applications of high-frequency PCBs:
Case Study 1: Wireless Communication Systems A telecommunications company requires high-performance PCBs for its wireless communication systems. They collaborated with a PCB manufacturer specializing in high-frequency designs. The manufacturer utilized advanced materials like Rogers and Teflon to ensure low dielectric loss and excellent signal integrity. The resulting high-frequency PCBs improved the system’s overall performance, enabling faster and more reliable wireless communication.
Case Study 2: Radar Systems A defense contractor needed high-frequency PCBs for their advanced radar systems. The PCB manufacturer employed controlled impedance design techniques to maintain consistent signal transmission across the board. They also implemented advanced manufacturing processes to achieve tight tolerances and steady signal losses. The high-frequency PCBs enhanced radar system sensitivity and accuracy, which is crucial for military applications.
Success Story: 5G Technology The emergence of 5G technology has driven the demand for high-frequency PCBs. Telecom equipment manufacturers have partnered with PCB suppliers to develop PCBs capable of handling the high-speed, high-frequency signals associated with 5G networks. Through innovative design techniques and material selection, these high-frequency PCBs enable reliable and efficient 5G communication, supporting faster data rates, reduced latency, and improved network coverage.
- Harsh Environment Electronics:
Harsh environment electronics refers to electronic devices and systems that operate reliably in extreme conditions such as high temperatures, humidity, vibration, and chemical exposure. These devices find applications in the aerospace, automotive, oil and gas, and industrial sectors. Here are some case studies and success stories demonstrating the successful implementation of harsh environment electronics:
Case Study 1: Automotive Electronics An automotive manufacturer requires electronics capable of withstanding high temperatures and vibrations for their engine control systems. They collaborated with an electronics company specializing in harsh environment applications, and the company developed ruggedized electronic components using advanced encapsulation techniques, thermal management solutions, and conformal coatings. These robust electronics enabled reliable engine control in extreme automotive environments.
Case Study 2: Oil and Gas Industry An oil and gas exploration company needed electronic systems for downhole drilling tools. These tools operate in harsh conditions, including high temperatures, pressure, and exposure to corrosive fluids. A specialized electronics manufacturer designed and tested electronic modules with hermetic packaging, specialized coatings, and high-temperature-resistant materials. The resulting electronics could withstand the demanding downhole environment, contributing to more efficient and reliable drilling operations.
Success Story: Aerospace Electronics The aerospace industry relies heavily on electronics that can withstand extreme temperature fluctuations, high altitude conditions, and intense vibrations. Electronic component manufacturers have developed ruggedized solutions incorporating advanced materials, conformal coatings, and shock-resistant designs. These electronics have been successfully deployed in aircraft avionics systems, satellite communication equipment, and space exploration missions, ensuring reliable operation in harsh aerospace environments.
- High-Reliability Medical Devices:
High-reliability medical devices are critical for patient safety, accurate diagnostics, and effective treatments. These devices must meet stringent regulatory standards and operate flawlessly in challenging healthcare environments. Here are some case studies and success stories highlighting the application of high-reliability medical devices:
Case Study 1: Implantable Devices A medical device company aimed to develop implantable cardiac devices with exceptional reliability. They collaborated with electronic component manufacturers specializing in medical-grade materials and manufacturing processes. Through rigorous testing, quality control measures, and adherence to regulatory requirements, they created implantable devices with extended battery life and improved sensing capabilities And reduced failure rates. These high-reliability devices have contributed to better patient outcomes and enhanced quality of life for individuals with cardiac conditions.
Case Study 2: Diagnostic Imaging Systems Medical imaging systems like computed tomography (CT) scanners and magnetic resonance imaging (MRI) machines require high-reliability electronics for accurate and timely diagnosis. A manufacturer of diagnostic imaging systems collaborated with electronic component suppliers to develop ruggedized electronics capable of withstanding the demanding clinical environment. These high-reliability electronics ensure precise imaging, reduce downtime and improve patient throughput.
Success Story: Point-of-Care Devices The emergence of point-of-care devices has transformed healthcare delivery by enabling faster and more accurate diagnoses at the bedside. These devices must be reliable, easy to use, and capable of withstanding repeated use and disinfection. A medical device company collaborated with electronics manufacturers to develop point-of-care devices like blood glucose meters and portable ECG machines. The resulting high-reliability electronics improve patient outcomes, reduce healthcare costs, and increase patient satisfaction.
Conclusion: PCB adhesive plays an integral role in the manufacturing and performance of electronic devices, providing mechanical stability, electrical connectivity, and protection against environmental factors