Non-Conductive Coatings for Electronics: Enhancing Performance and Protection
Non-Conductive Coatings for Electronics: Enhancing Performance and Protection
Introduction to Non-Conductive Coatings
In the realm of electronics, ensuring the longevity and reliability of components is paramount. One critical strategy employed to achieve this is the use of non-conductive coatings. These coatings protect electronic components from environmental factors, prevent electrical shorts, and improve overall device performance. This article delves into the significance of non-conductive coatings, their types, applications, and the benefits they offer to the electronics industry.
Types of Non-Conductive Coatings
Non-conductive coatings come in various forms, each tailored to meet specific needs and requirements in electronics. Here, we explore some of the most commonly used types:
Epoxy Coatings
Epoxy coatings are known for their excellent adhesion, chemical resistance, and mechanical properties. These coatings are widely used in electronics because they form a rigid, protective barrier over surfaces. Epoxy coatings are particularly beneficial in protecting circuit boards and other sensitive components from moisture, dust, and chemicals.
Polyurethane Coatings
Polyurethane coatings offer flexibility and durability, making them suitable for a wide range of electronic applications. These coatings are resistant to abrasion, chemicals, and UV radiation. Polyurethane coatings are often used in applications where flexibility is essential, such as in wearable electronics and flexible circuit boards.
Silicone Coatings
Silicone coatings are highly valued for their thermal stability and flexibility. They can withstand extreme temperatures and provide excellent insulation properties. Silicone coatings are commonly used in high-temperature environments and in applications where thermal management is crucial, such as in power electronics and LED devices.
Acrylic Coatings
Acrylic coatings are known for their ease of application and quick drying time. They provide good moisture resistance and electrical insulation. Acrylic coatings are often used in consumer electronics and other applications where fast production turnaround is necessary.
Applications of Non-Conductive Coatings
Non-conductive coatings are applied across various sectors of the electronics industry. Their versatility and protective capabilities make them indispensable in numerous applications:
Printed Circuit Boards (PCBs)
Printed circuit boards are the backbone of most electronic devices. Non-conductive coatings protect PCBs from environmental factors such as moisture, dust, and chemicals. They also help prevent electrical shorts by insulating components and traces. Epoxy and acrylic coatings are commonly used for this purpose.
Semiconductor Devices
Semiconductor devices, such as integrated circuits and microchips, require protection from contaminants and mechanical damage. Non-conductive coatings provide a protective barrier that enhances the reliability and longevity of these critical components. Silicone coatings are often preferred for their thermal stability.
Consumer Electronics
In consumer electronics, non-conductive coatings protect devices such as smartphones, tablets, and wearable technology. These coatings ensure that devices can withstand everyday wear and tear, exposure to moisture, and accidental spills. Polyurethane coatings are prevalent in this sector due to their flexibility and durability.
Automotive Electronics
Automotive electronics, including sensors, control units, and infotainment systems, are exposed to harsh environments. Non-conductive coatings protect these components from temperature fluctuations, vibrations, and exposure to chemicals and moisture. Silicone and epoxy coatings are commonly used in automotive applications.
Medical Devices
Medical devices, such as diagnostic and implantable devices, require high levels of reliability and protection. Non-conductive coatings ensure that these devices remain functional in challenging environments, including exposure to bodily fluids and sterilization processes. Biocompatible coatings, such as specific silicone formulations, are used in medical applications.
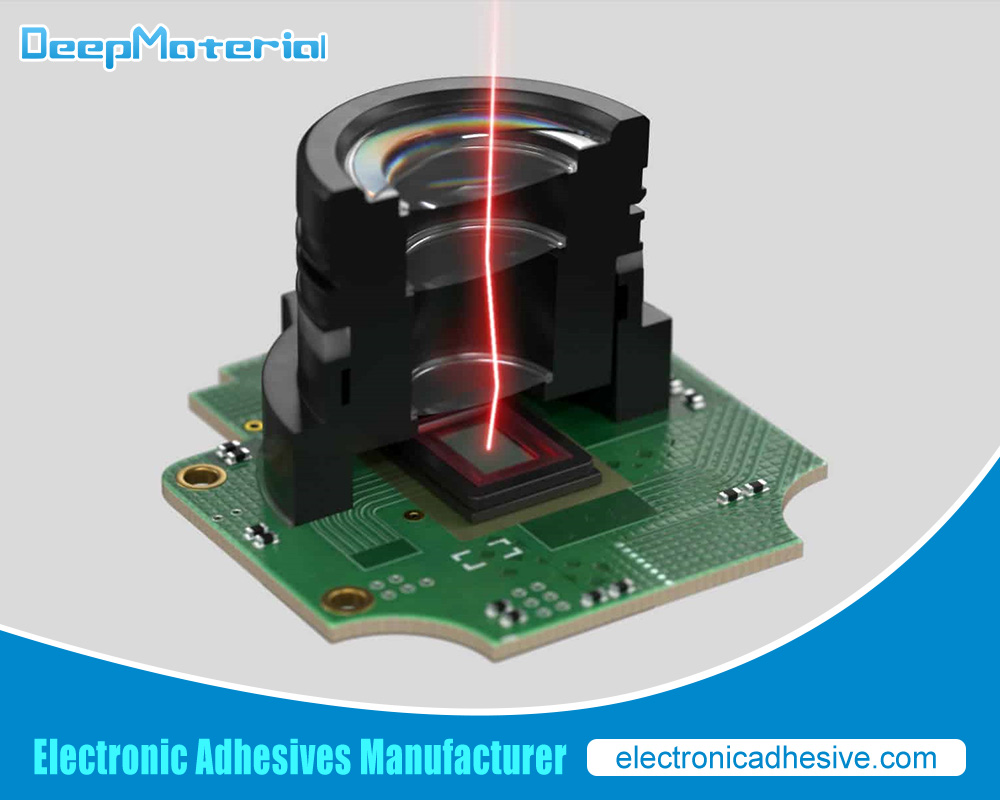
Benefits of Non-Conductive Coatings
The use of non-conductive coatings in electronics offers numerous benefits that enhance device performance, reliability, and longevity:
Environmental Protection
Non-conductive coatings provide a barrier against environmental factors such as moisture, dust, and chemicals. This protection is crucial in preventing corrosion, oxidation, and other forms of damage that can compromise electronic components.
Electrical Insulation
Non-conductive coatings enhance the reliability of electronic devices by preventing electrical shorts and ensuring proper insulation. This is particularly important in high-density circuits and devices with closely spaced components.
Thermal Management
Some non-conductive coatings, particularly silicone-based ones, offer excellent thermal management properties. They help dissipate heat and protect components from thermal stress, ensuring stable operation in high-temperature environments.
Mechanical Protection
Non-conductive coatings provide mechanical protection by forming a durable layer over electronic components. This protection helps prevent physical damage, such as scratches, abrasions, and impacts, which can affect the performance and longevity of devices.
Chemical Resistance
In industrial and automotive applications, electronic components are often exposed to chemicals and solvents. Non-conductive coatings provide a chemical-resistant barrier, preventing damage and degradation caused by exposure to harsh substances.
Flexibility and Conformality
Many non-conductive coatings are flexible and conformal, meaning they can adapt to the shape of the components they cover. This is particularly important in applications where components may undergo mechanical stress or where space constraints are a concern.
Innovations and Future Trends
The field of non-conductive coatings for electronics is continuously evolving, driven by advancements in materials science and technology. Several emerging trends and innovations are shaping the future of this field:
Nanocoatings
Nanocoatings, composed of nanoscale materials, offer enhanced protective properties compared to traditional coatings. These coatings provide superior barrier protection, improved thermal conductivity, and increased mechanical strength. Nanocoatings are being explored for various electronic applications, including wearables and flexible electronics.
Biocompatible Coatings
With the growing demand for medical devices and implantable electronics, biocompatible non-conductive coatings are gaining importance. These coatings are designed to be safe for use in the human body and to withstand sterilization processes. Advances in biocompatible coatings are expanding the possibilities for medical electronics.
Self-Healing Coatings
Self-healing coatings can autonomously repair minor damages, enhancing the longevity and reliability of electronic devices. These coatings can recover from scratches, abrasions, and other forms of mechanical damage. Research in self-healing materials opens new avenues for durable and resilient non-conductive coatings.
Environmentally Friendly Coatings
Sustainability is becoming a key consideration in the development of non-conductive coatings. Environmentally friendly coatings, made from biodegradable or non-toxic materials, are being developed to reduce the environmental impact of electronic manufacturing and disposal. These coatings aim to provide adequate protection while minimizing ecological harm.
Advanced Deposition Techniques
Innovations in deposition techniques, such as atomic layer deposition (ALD) and plasma-enhanced chemical vapor deposition (PECVD), are enabling the precise application of non-conductive coatings. These techniques allow for uniform and conformal coatings on complex geometries, improving the performance and reliability of electronic components.
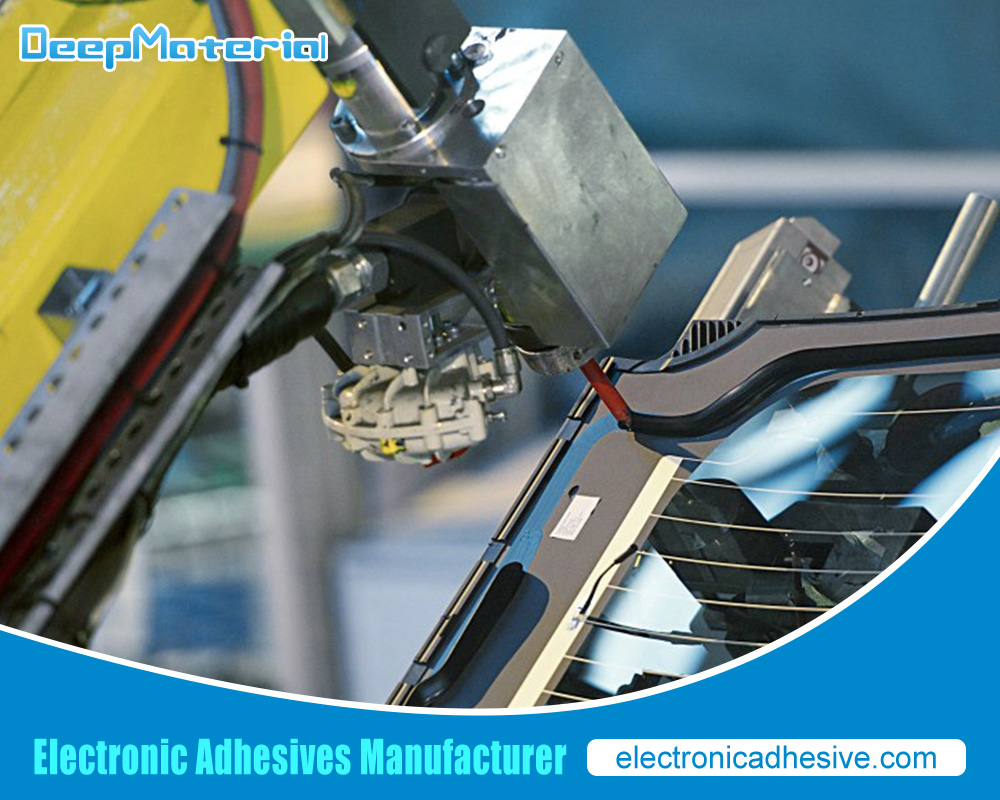
Conclusion
Non-conductive coatings play a crucial role in enhancing the performance, reliability, and longevity of electronic devices. By protecting environmental factors, electrical shorts, and mechanical damage, these coatings ensure the optimal functioning of components in a wide range of applications. As technology advances, innovations in materials and deposition techniques are driving the development of more effective and sustainable non-conductive coatings. The future of electronics is poised to benefit from these advancements, resulting in more robust and reliable devices across various industries.
For more about choosing the top non-conductive coatings for electronics: enhancing performance and protection, you can pay a visit to DeepMaterial at https://www.electronicadhesive.com/ for more info.