Low Temperature Adhesives: Innovation and Application in Modern Industry
Low Temperature Adhesives: Innovation and Application in Modern Industry
In recent years, the demand for efficient and versatile adhesives has increased due to the rise of advanced manufacturing and sustainable processes. Low temperature adhesives have garnered particular attention among the various adhesives available today. These adhesives are designed to cure and bond materials at lower temperatures than traditional alternatives. Their benefits include energy savings, reduced thermal damage to sensitive substrates, and quicker curing times, making them suitable for various industries, including electronics, automotive, aerospace, and medical devices.
This article will explore the key advantages, applications, and emerging trends associated with Low temperature adhesives and showcase why they are becoming essential solutions in modern industry.
What Are Low Temperature Adhesives?
Low temperature adhesives are bonding materials that cure or set at relatively lower temperatures, typically below 100°C. Unlike traditional adhesives, which require high heat to activate and heal, these adhesives are engineered to perform optimally under more excellent conditions. This allows for bonding temperature-sensitive materials without the risk of heat-induced degradation.
Types of Low Temperature Adhesives
There are several types of low temperature adhesives, each with its properties and uses:
- Epoxy Adhesives:Epoxies are known for their strong bonding capabilities. They can be formulated to cure at lower temperatures while still providing a robust bond.
- Acrylic Adhesives: These adhesives cure quickly at low temperatures and are often used for bonding plastics and metals.
- Silicone Adhesives: Silicone-based adhesives are suitable for applications where flexibility and temperature resistance are essential. They can bond materials without requiring excessive heat.
- Polyurethane Adhesives: Offering high strength and flexibility, polyurethane adhesives are often chosen for applications requiring resistance to environmental factors such as moisture and chemicals.
Critical Advantages of Low Temperature Adhesives
Reduced Thermal Stress on Materials
One of the primary benefits of Low temperature adhesives is their ability to reduce thermal stress during bonding. This is especially important for heat-sensitive materials such as certain plastics, composites, and electronic components. By curing at lower temperatures, these adhesives help prevent the warping, cracking, or melting of delicate substrates.
Energy Efficiency
Lower curing temperatures translate into significant energy savings, particularly in industries requiring large-scale adhesive applications. Conventional adhesives that require high heat for activation consume more energy, increasing operational costs and environmental impact. Low temperature adhesives offer a more sustainable alternative, making them ideal for companies focused on reducing their carbon footprint.
Faster Production Cycles
In manufacturing environments where time is critical, the quick curing time of Low temperature adhesives offers a competitive advantage. These adhesives often require shorter curing periods than traditional adhesives, speeding up production cycles and increasing efficiency.
Enhanced Compatibility with Sensitive Electronics
The growing complexity of electronic devices demands adhesives that can be applied without damaging sensitive components. Low temperature adhesives are particularly suited for use in electronics assembly, where overheating can lead to component failure or reduced device lifespan. These adhesives provide a reliable bond while safeguarding the integrity of delicate circuitry.
Improved Worker Safety
Adhesives that require high temperatures for application pose potential hazards to workers, including burns or inhalation of harmful fumes. Low temperature adhesives reduce these risks, creating a safer work environment by minimizing exposure to excessive heat and volatile compounds.
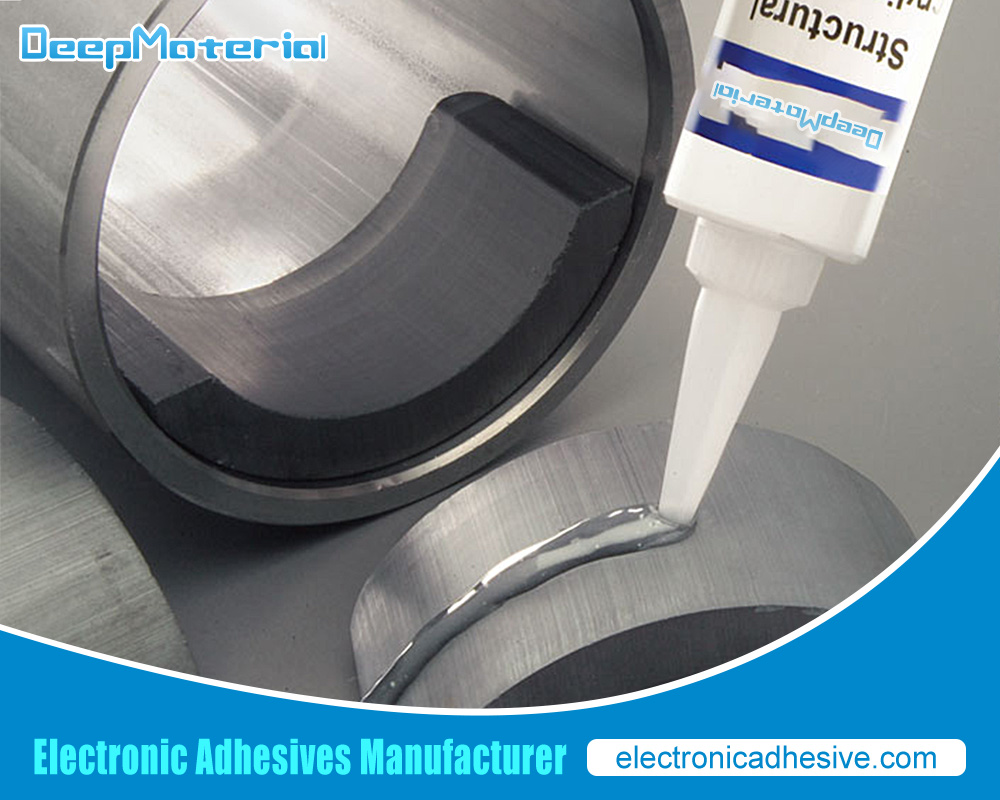
Applications of Low Temperature Adhesives
Electronics and Electrical Components
Low temperature adhesives have become integral to the production of modern electronics. Their ability to bond without damaging sensitive components has made them a preferred choice for assembling printed circuit boards (PCBs), sensors, and microchips. These adhesives also help seal and encapsulate delicate parts, offering protection from moisture, dust, and other environmental contaminants.
- Printed Circuit Board (PCB) Assembly:Low temperature adhesives are used to attach surface-mounted devices (SMDs) and other electronic components to PCBs without exposing them to high temperatures that could damage them.
- Battery Sealing:In battery manufacturing, particularly for electric vehicles, Low temperature adhesives bond and seal battery cells, ensuring long-term durability and performance.
- Heat-sensitive Sensors: Many sensors in modern devices require precise bonding without exposure to heat, so Low temperature adhesives play a critical role in maintaining their accuracy and functionality.
Automotive and Aerospace Industries
The automotive and aerospace industries continually seek materials that offer strength, durability, and energy efficiency. Low temperature adhesives meet these criteria, allowing manufacturers to assemble complex components while reducing overall energy consumption during production.
- Interior Assembly: Adhesives that cure at low temperatures are commonly used in vehicle interiors, where bonding materials like plastic, fabric, and rubber must be used without being subjected to heat that could warp or damage them.
- Composite Bonding: In aerospace applications, Low temperature adhesives are essential for bonding lightweight composites, which are crucial for reducing aircraft weight and improving fuel efficiency.
- Thermal Management in Automotive Electronics:Low temperature adhesives help assemble electronic control units (ECUs) and sensors within vehicles, offering stable bonds without affecting thermal-sensitive components.
Medical Devices and Biocompatible Applications
The medical field demands materials that function efficiently and meet stringent safety and biocompatibility standards. Low temperature adhesives are increasingly used for assembling medical devices, from diagnostic tools to implantable devices, due to their ability to bond without compromising the properties of delicate medical-grade plastics and metals.
- Wearable Medical Devices: Adhesives are essential in producing wearable devices like heart monitors and glucose sensors, where low temperature curing is necessary to preserve the device’s sensitive electronics.
- Implantable Devices: Low temperature adhesives that meet biocompatibility standards are used to manufacture implantable devices, ensuring safe and effective bonding without causing adverse reactions.
- Single-use Instruments: For disposable medical tools, adhesives that bond quickly and at low temperatures help streamline production while maintaining sterile conditions.
Packaging and Consumer Goods
Low temperature adhesives are increasingly used in the packaging industry for applications requiring secure sealing without high heat. It is essential for heat-sensitive packaging materials such as plastics, films, and biodegradable options that might degrade under high temperatures.
- Flexible Packaging: Low temperature adhesives are ideal for bonding thin films and flexible packaging materials in the food and beverage, pharmaceutical, and consumer goods industries.
- Product Labeling: Many consumer goods use low temperature adhesives in product labeling to ensure secure attachment without distorting the label due to heat.
Emerging Trends in Low Temperature Adhesive Technology
Green Adhesives and Sustainability
Developing eco-friendly low temperature adhesives is becoming a trend as industries push toward more sustainable production practices. Formulations based on bio-based ingredients, water-based systems, and solvent-free options are being developed to reduce the environmental impact of adhesive use. These innovations aim to offer the same performance as traditional adhesives while minimizing their carbon footprint.
Advances in Smart Adhesives
Innovative adhesives that respond to specific stimuli such as temperature changes, pressure, or electrical currents are incorporated into Low temperature formulations. These adhesives can be designed to bond only when exposed to certain conditions, offering greater control and precision in manufacturing processes.
Hybrid Adhesives for Multifunctional Use
Hybrid adhesives that combine the properties of different types of adhesives are being developed to meet the specific needs of various industries. For example, combining silicone’s flexibility with epoxy’s strength results in a hybrid adhesive that can bond materials requiring both flexibility and stability at low temperatures.
Miniaturization and Electronics
With electronic devices’ ongoing miniaturization, the demand for Low temperature adhesives that can bond at a microscopic level is increasing. These adhesives must provide solid bonds, ensure the efficient dissipation of heat, and protect tiny, intricate assemblies from environmental factors.
Challenges and Limitations of Low Temperature Adhesives
While low temperature adhesives offer numerous benefits, they are not without challenges:
- Limited Strength at High Temperatures:Some low temperature adhesives may lose their strength or degrade when exposed to high temperatures after curing, which can limit their use in specific applications.
- Slower Curing in Some Cases: Although Low temperature adhesives typically cure quickly, specific formulations may take longer to set than their high-temperature counterparts, depending on the particular application.
- Cost: Advanced Low temperature adhesives may have a higher initial cost due to the specialized materials and formulations required for production. However, the long-term savings in energy and reduced material degradation often offset these costs.
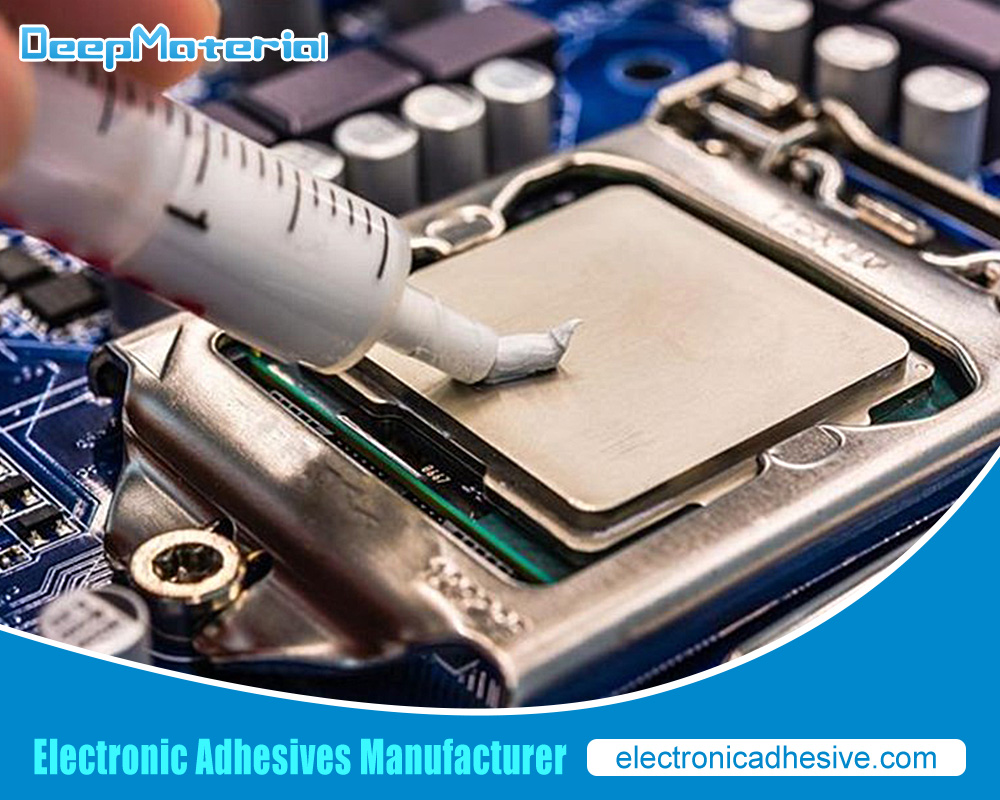
Conclusion
Low temperature adhesives are revolutionizing how industries approach bonding and assembly, mainly where energy efficiency, material sensitivity, and speed are critical factors. By allowing for strong, durable bonds at cooler temperatures, these adhesives offer a versatile solution across diverse sectors such as electronics, automotive, aerospace, medical devices, and packaging.
For more about choosing the Top Low Temperature Adhesives: Innovation and Application in Modern Industry, you can pay a visit to DeepMaterial at https://www.electronicadhesive.com/ for more info.