Exploring the Different Types of Non Conductive Coating for Electronics
Exploring the Different Types of Non Conductive Coating for Electronics
Non conductive coating for electronics is a protective layer that is applied to electronic components to prevent electrical conductivity. It is essential in ensuring the longevity and reliability of electronic devices. Non conductive coatings provide insulation and protection against moisture, corrosion, and other environmental factors that can damage electronics. In this article, we will explore the importance of using non conductive coating for electronics, the different types of coatings available, the benefits they offer, factors to consider when choosing a coating, application methods, common uses, challenges and limitations, and future trends in the industry.
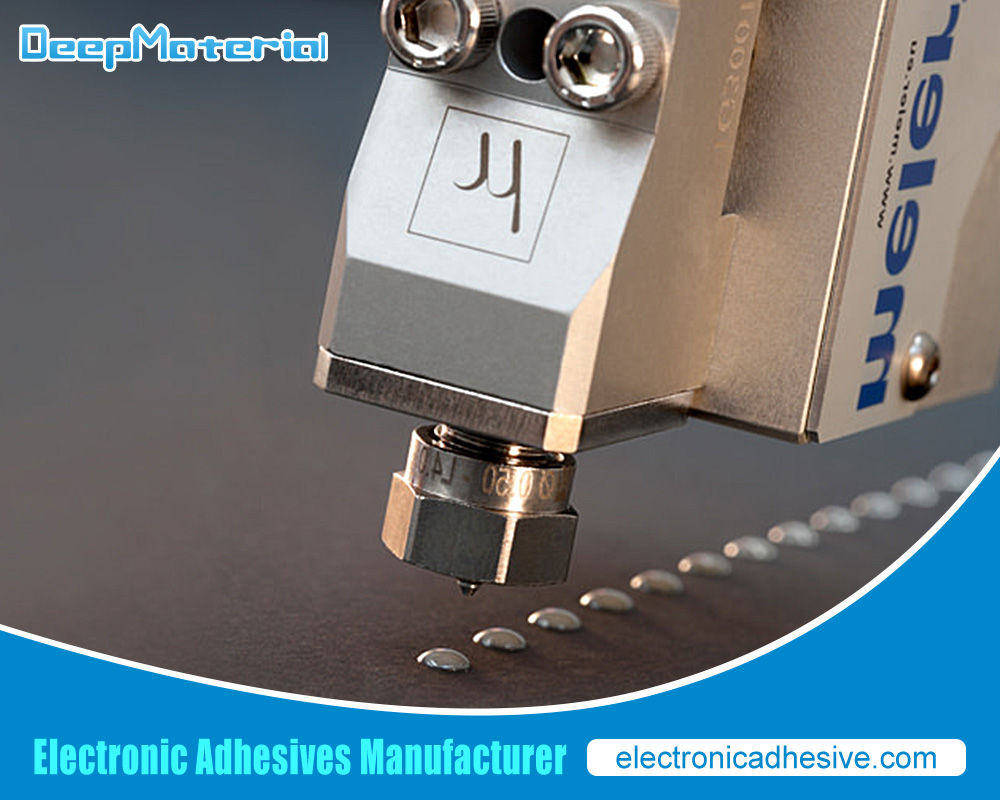
Types of Non Conductive Coating for Electronics
There are several types of non conductive coatings available for electronics, each with its own unique properties and applications. Some of the most common types include acrylic coatings, epoxy coatings, silicone coatings, polyurethane coatings, and parylene coatings.
Acrylic coatings are known for their excellent adhesion and flexibility. They provide good protection against moisture and corrosion and are often used in consumer electronics and automotive applications.
Epoxy coatings offer high chemical resistance and excellent adhesion to various substrates. They are commonly used in industrial applications where durability and protection against harsh environments are required.
Silicone coatings are known for their high temperature resistance and flexibility. They provide excellent protection against moisture, chemicals, and UV radiation. Silicone coatings are often used in aerospace, automotive, and medical applications.
Polyurethane coatings offer excellent abrasion resistance and durability. They provide protection against moisture, chemicals, and UV radiation. Polyurethane coatings are commonly used in outdoor applications and in environments where high durability is required.
Parylene coatings are unique in that they are applied through a vacuum deposition process. They offer excellent protection against moisture, chemicals, and temperature extremes. Parylene coatings are often used in medical devices, aerospace, and defense applications.
Benefits of Using Non Conductive Coating for Electronics
Using non conductive coating for electronics offers several benefits in terms of protection, insulation, durability, and resistance to chemicals and abrasion.
One of the primary benefits is protection against moisture and corrosion. Non conductive coatings create a barrier that prevents moisture from reaching the electronic components, reducing the risk of corrosion and damage. This is particularly important in outdoor or humid environments where electronics are exposed to moisture.
Non conductive coatings also provide improved insulation. They prevent the flow of electricity between components, reducing the risk of short circuits and electrical damage. This is especially important in high voltage applications or in environments where there is a risk of electrical discharge.
Another benefit is enhanced durability and longevity. Non conductive coatings provide a protective layer that can withstand harsh environments, chemicals, and abrasion. This extends the lifespan of electronic devices and reduces the need for frequent repairs or replacements.
Non conductive coatings also offer increased resistance to chemicals and abrasion. They protect electronic components from exposure to chemicals that can cause corrosion or damage. Additionally, they provide a protective layer that can withstand abrasion from handling or environmental factors.
Factors to Consider When Choosing Non Conductive Coating for Electronics
When choosing a non conductive coating for electronics, there are several factors to consider to ensure the best performance and compatibility with the specific application.
The type of electronics being coated is an important consideration. Different coatings have different properties and may be more suitable for certain types of electronics. For example, a silicone coating may be more appropriate for a medical device that requires high temperature resistance, while an epoxy coating may be better suited for an industrial application that requires high chemical resistance.
Environmental factors also play a role in choosing the right coating. The temperature, humidity, and exposure to chemicals or UV radiation in the environment can affect the performance of the coating. It is important to select a coating that can withstand the specific environmental conditions.
The application method is another factor to consider. Different coatings may require different application methods such as spray coating, dip coating, brush coating, or vacuum deposition. The chosen method should be compatible with the coating and the specific requirements of the application.
Cost and availability are also important factors to consider. Some coatings may be more expensive or harder to source than others. It is important to balance the cost with the desired performance and availability of the coating.
Common Uses of Non Conductive Coating for Electronics
Non conductive coatings are used in a wide range of electronic applications to provide protection and insulation. Some of the common uses include printed circuit boards, sensors, medical devices, aerospace and defense equipment, and consumer electronics.
Printed circuit boards (PCBs) are one of the most common applications for non conductive coatings. The coating is applied to the PCBs to protect the components from moisture, dust, and other contaminants. It also provides insulation and prevents electrical conductivity between the components.
Sensors often require non conductive coatings to protect them from moisture, chemicals, and temperature extremes. The coating helps to ensure the accuracy and reliability of the sensor readings.
Medical devices such as pacemakers, implantable devices, and diagnostic equipment require non conductive coatings to protect them from moisture, body fluids, and chemicals. The coating also provides insulation and prevents electrical conductivity in these sensitive devices.
Aerospace and defense equipment often operate in harsh environments and are exposed to extreme temperatures, moisture, and chemicals. Non conductive coatings are used to protect the electronic components from these hazards and ensure their reliable operation.
Consumer electronics such as smartphones, tablets, and wearable devices also benefit from non conductive coatings. The coating provides protection against moisture, dust, and other contaminants that can damage the components. It also enhances the durability and longevity of these devices.
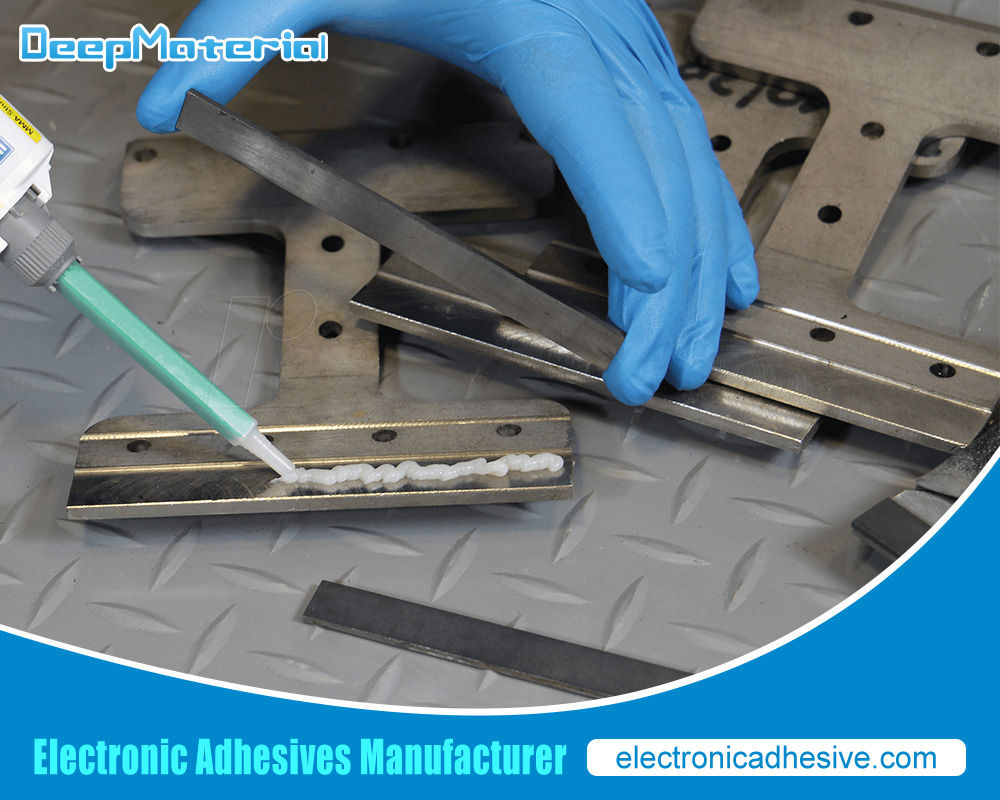
Final Thoughts
In conclusion, non conductive coating for electronics is essential in protecting electronic components from moisture, corrosion, and other environmental hazards. It provides insulation and prevents electrical conductivity, ensuring the reliable and safe operation of electronic devices. When choosing a non conductive coating, it is important to consider factors such as the type of electronics, environmental conditions, application method, and cost. By selecting the right coating, you can enhance the durability and longevity of your electronics and ensure their optimal performance.
For more about choosing the Non Conductive Coating for Electronics, you can pay a visit to DeepMaterial at https://www.electronicadhesive.com/about/ for more info.