Evaluating The Performance and Reliability of Solutions Within The Conformal Coating in Electronics Market
Evaluating The Performance and Reliability of Solutions Within The Conformal Coating in Electronics Market
Conformal coating is like a protective shield for electronic parts and circuit boards. It keeps them safe from things like moisture, dust, chemicals, and changes in temperature. This coating is really thin and fits closely over the parts it’s protecting. As electronics get smaller and more complex, having this kind of protection is super important.
Importance of Evaluating Performance and Reliability of Solutions
If a conformal coating doesn’t work well, it could cause big problems for electronics, like parts rusting, circuits getting damaged, or the whole device stopping working. This could mean having to fix or replace them, which can cost a lot. That’s why it’s so important to make sure the conformal coating solution is strong and reliable before using it.
Choosing a good conformal coating solution means electronics last longer and work better because they’re protected from damage. It also means people who make and use electronics can feel more confident that their devices won’t easily get damaged.
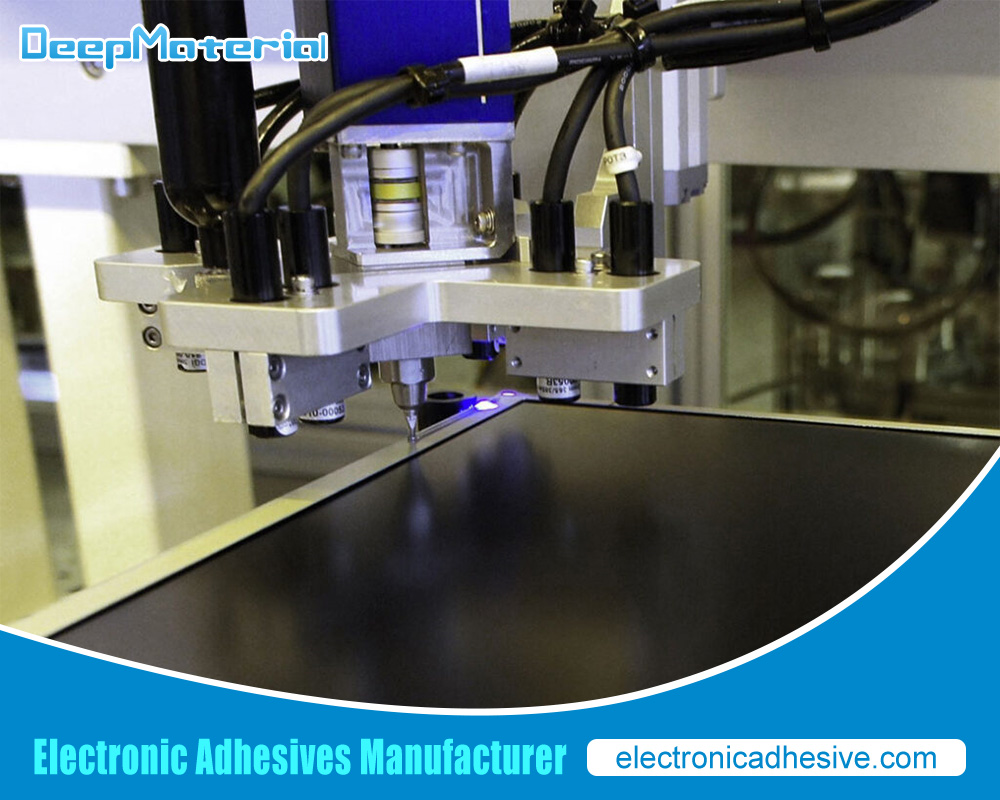
Factors Affecting Performance and Reliability of Conformal Coating Solutions
What the coating is made of really matters because different materials protect against moisture, chemicals, and temperature changes in different ways. Also, how the coating is put on—like what method or tools are used—can change how well it works.
The environment where the electronics are used can also affect the coating. Big changes in temperature or humidity can make materials expand or shrink, which might crack the coating. Chemicals in the air can wear the coating down over time, and sunlight can change the color or weaken some types of coatings. So, it’s important to think about all these things when choosing and using a conformal coating solution.
Types of Conformal Coating Solutions and their Properties
In the market, you can find different types of conformal coating solutions. Each one has special features and is good for certain uses. Acrylic coatings are popular because they keep moisture out really well and are easy to put on. Silicone coatings are great for situations with a lot of temperature changes because they are very flexible and can handle heat well.
Urethane coatings are strong against chemicals and last a long time. Parylene coatings give the best protection against moisture, chemicals, and big temperature changes but need special machines to apply them. When choosing a conformal coating, think about what the electronic part needs, like what kind of weather it will face, how long it needs to last, and how much protection it needs. Knowing about each type of coating helps you pick the best one.
Testing Methods for Evaluating Performance and Reliability
To make sure conformal coatings do their job well, there are different tests you can do. Looking at the coating closely helps see if it covers everything evenly. Adhesion testing checks if the coating sticks well to the part it’s protecting. Moisture resistance testing looks at how well the coating keeps out water over time.
Testing how the coating handles changes in temperature shows if it can last in hot or cold conditions. Other tests, like checking how well it keeps electricity from leaking and how it does against salt spray, might be done too, depending on what the coated part needs to do. These tests help make sure the coating will protect electronic parts well.
Common Issues and Challenges in Conformal Coating Applications
Applying conformal coating can sometimes lead to problems. One issue is when not all parts get covered well, leaving them open to harm. Sometimes, the thickness of the coating isn’t the same everywhere because it wasn’t put on right, which means protection isn’t even.
Delamination, where the coating doesn’t stick and separates from the thing it’s supposed to protect, can happen because it didn’t stick well or the environment messed it up. Dirt or other stuff getting into the coating during the process can make the coating not work well.
To fix these problems, people applying coatings need good training and must follow the best ways to do it. Checking the work carefully and often helps find and fix problems early. Also, picking the right kind of coating that works well with the material it’s going on can stop many issues before they start.
Impact of Environmental Factors on Conformal Coating Performance
The environment can really affect how well conformal coatings work. Changes in temperature and moisture can make materials expand or shrink, which can crack or peel the coating. Being around chemicals can wear the coating down over time, hurting its ability to protect. Sunlight can change the color of some coatings and make them weaker.
To lessen these environmental effects, it’s important to choose a coating that can handle these things. Planning the design to keep harmful elements away, like making sure there’s good air flow and tight seals, can also help. Regular checks and upkeep make sure problems are found and fixed quickly.
Comparison of Different Conformal Coating Solutions
Each type of conformal coating has its own good and bad points. Acrylic coatings are great at keeping moisture out and are easy to use, but they might not be strong enough against chemicals or very hot or cold temperatures. Silicone coatings can handle a wide range of temperatures and are very flexible, but they might yellow as they age.
Urethane coatings are very tough against chemicals and last a long time, but putting them on can require special tools. Parylene coatings protect really well against moisture, chemicals, and extreme temperatures, but they cost more and need special equipment and steps to apply.
Choosing a conformal coating means looking closely at what the coated item needs, like where it will be used, how long it needs to last, and what kind of protection it needs. Thinking about these things helps pick the best coating for the job.
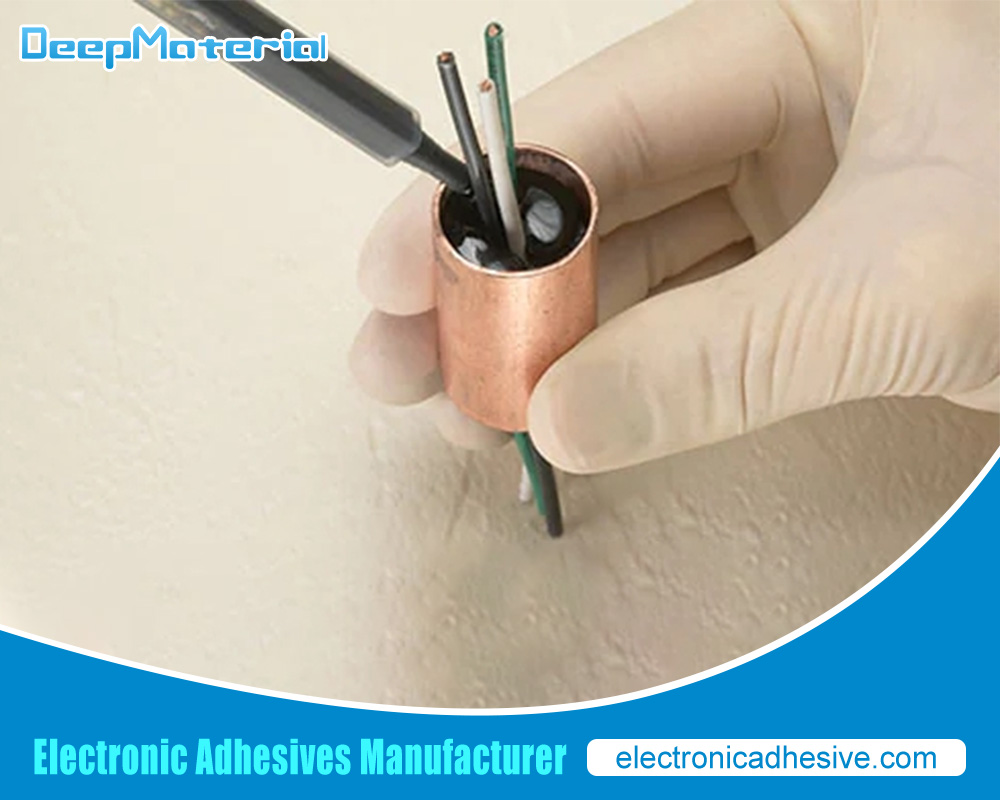
Conclusion and Recommendations
Conformal coating is very important for keeping electronic parts and circuit boards safe from things like moisture, dust, and temperature changes. Making sure the coating works well and can be trusted is key to making electronic devices last longer and work better. The kind of chemicals in the coating, how it’s put on, and the environment around it can all change how well the coating works.
When choosing a coating, it’s smart to think about what the electronic part needs and to look at the good and bad points of different coatings. Testing the coating carefully, following the rules for how to use it, and keeping an eye on it with regular checks are all important steps for doing a good job with conformal coating.
By knowing how important conformal coating is and choosing the right coating with care, companies that make electronics can make sure their products work well and are reliable in all kinds of situations.
For more about evaluating the performance and reliability of solutions within the conformal coating in electronics market, you can pay a visit to DeepMaterial at https://www.electronicadhesive.com/ for more info.