Enhancing Electronic Safety: Exploring Non Conductive Coating for Electronics
Enhancing Electronic Safety: Exploring Non Conductive Coating for Electronics
In today’s tech-driven world, electronic devices have become ubiquitous, playing vital roles in various aspects of our lives. However, with their widespread usage comes the imperative need to ensure safety and reliability. One significant aspect of this safety is protecting electronic components from potential electrical hazards. Non conductive coatings offer a promising solution to this challenge, providing a shield against electrical conductivity and enhancing the durability and lifespan of electronic devices. This article delves into Non conductive coatings for electronics, exploring their benefits, applications, and prospects.
Understanding Non Conductive Coatings:
Non conductive coatings serve as protective barriers, preventing electrical conductivity between components or external sources. They are applied to electronic surfaces to insulate and safeguard against damage from moisture, dust, chemicals, and other environmental factors.
Defining Non Conductive Coatings:
Non conductive coatings are specially formulated materials designed to impede the flow of electricity. Unlike conductive coatings that facilitate electrical conduction, these coatings act as insulators, maintaining electrical isolation and preventing short circuits or electrical leakage.
Mechanism of Insulation: How Do They Work?
The effectiveness of Non conductive coatings lies in their ability to interrupt the flow of electrical current. It is achieved by creating a high-resistance barrier, inhibiting electron movement, and minimizing the risk of electrical discharge. These coatings shield electronic components from potential damage by forming a protective layer while maintaining signal integrity.
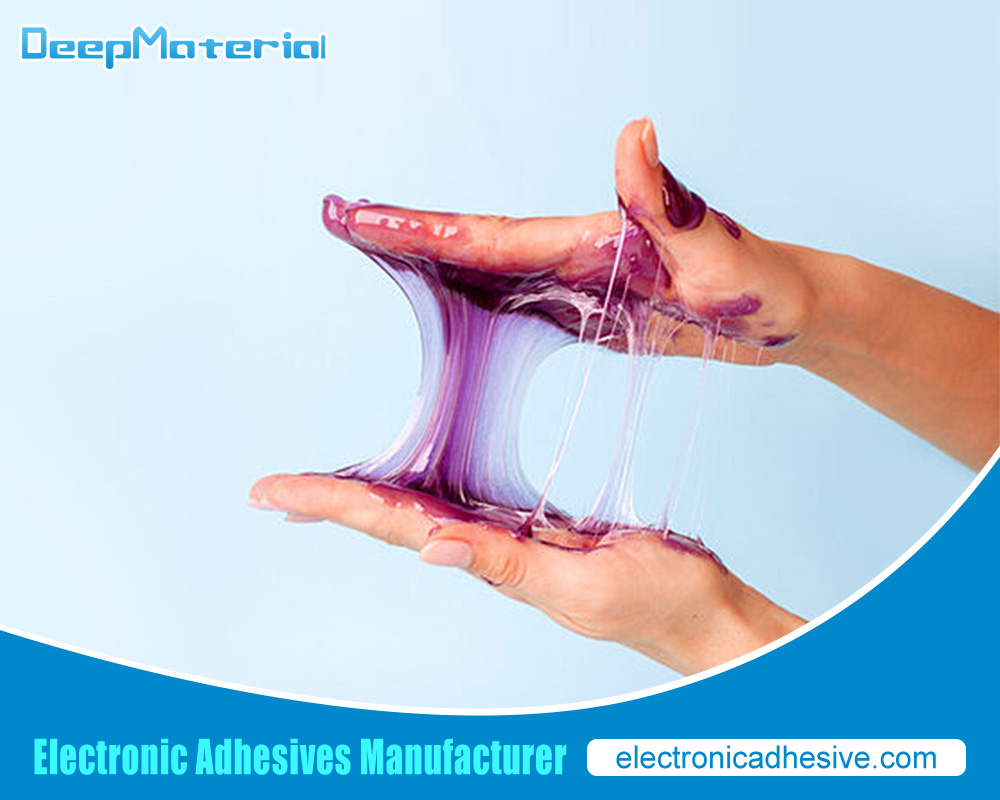
Types of Non Conductive Coatings
Polymeric Coatings:
- They comprise organic polymers such as epoxy, silicone, or acrylic resins.
- Flexible and durable, offering excellent adhesion to various substrates.
- They are widely used in consumer electronics, automotive, and aerospace applications due to their versatility and cost-effectiveness.
Ceramic Coatings:
- Consists of inorganic materials like alumina, silica, or zirconia.
- They are known for their superior thermal and chemical resistance properties.
- Ideal for high-temperature environments and harsh operating conditions, commonly employed in electronic circuit boards, insulators, and semiconductor devices.
Beyond Traditional Coatings:
- Emerging technologies are pushing the boundaries of Non conductive coatings.
- Graphene-based coatings exhibit remarkable conductivity-blocking capabilities alongside exceptional mechanical strength.
- Nanocomposite coatings combine multiple materials to enhance performance, such as improved flexibility, thermal stability, and corrosion resistance.
Advantages of Non Conductive Coatings:
These coatings offer a suite of advantages that protect and enhance electronic components’ performance. Let’s delve into the benefits they bring:
Electrical Insulation: Preventing Short Circuits
- Non conductive coatings act as a barrier between conductive elements, inhibiting the flow of electrical current.
- By preventing short circuits, they ensure the uninterrupted functionality of electronic devices, reducing the risk of malfunctions and damage.
Corrosion Resistance: Prolonging Lifespan
- These coatings protect against corrosive agents like moisture, chemicals, and pollutants.
- By thwarting corrosion, they extend the lifespan of electronic components, enhancing their durability and reliability even in harsh environments.
Thermal Management: Dissipating Heat Effectively
- Non conductive coatings facilitate efficient heat dissipation, preventing thermal buildup within electronic devices.
- By dispersing heat, they prevent overheating, which can degrade performance and compromise the integrity of sensitive components.
Environmental Protection: Shielding Against Moisture and Dust
- The protective barrier created by Non conductive coatings shields electronic components from moisture ingress and dust accumulation.
- By safeguarding against environmental contaminants, they maintain optimal performance and reduce the risk of malfunctions caused by exposure to external elements.
Applications Across Industries
Non conductive coatings are insulating layers applied to electronic components to prevent electrical conductivity. They act as a barrier, shielding devices from moisture, dust, and other contaminants while avoiding short circuits and electrical failures.
- Consumer Electronics:Non conductive coatings safeguard smartphones, laptops, and wearables from environmental factors and accidental spills.
- Automotive Sector:These coatings enhance the reliability of electrical components in vehicles, protecting them from corrosion and ensuring optimal performance, especially in challenging conditions.
- Aerospace and Defense: In harsh environments like those encountered in aerospace and defense applications, Non conductive coatings provide vital insulation, maintaining the integrity and functionality of critical electronics.
- Medical Devices: Promoting safety in healthcare technologies, Non conductive coatings ensure the reliability of medical devices, prevent electrical hazards, and ensure patient well-being.
Benefits of Non Conductive Coatings:
- Electrical Insulation: Prevents electrical conductivity, reducing the risk of short circuits and electrical failures.
- Environmental Protection: Shields electronics from moisture, dust, chemicals, and other contaminants, prolonging their lifespan.
- Enhanced Reliability: Improves the reliability and performance of electronic components, particularly in demanding environments.
- Safety Assurance: Promotes safety in various industries, including healthcare, automotive, aerospace, and consumer electronics, by mitigating electrical hazards.
Innovations and Emerging Trends:
Non conductive coatings for electronics offer a promising solution, providing insulation and protection against external elements. Let’s delve into the innovations and emerging trends shaping this vital field:
Nanotechnology Integration: Miniaturization and Enhanced Performance
- Nanotechnology plays a pivotal role in the development of Non conductive coatings for electronics.
- By harnessing nanoparticles’ unique properties, such as increased surface area and reactivity, manufacturers can achieve remarkable miniaturization without compromising performance.
- Nanocoatings offer superior insulation properties, shielding delicate electronic components from electrical short circuits and corrosion.
Self-Healing Coatings: Repairing Minor Damages Automatically
- Self-healing coatings represent a revolutionary advancement in electronics protection.
- Embedded with microcapsules containing healing agents, these coatings can autonomously repair minor damages, extending the lifespan of electronic devices.
- The self-healing capability reduces maintenance costs and enhances product reliability, particularly in harsh operating environments.
Flexible Substrates: Enabling Conformal Coating for Complex Shapes
- Traditional rigid substrates often pose challenges when coating complex-shaped electronic assemblies.
- Flexible substrates, such as polymers and elastomers, offer greater versatility and conformability, ensuring uniform coverage and protection across intricate geometries.
- Conformal coating facilitates reliable insulation without compromising the mechanical integrity or functionality of the electronic device.
Eco-Friendly Formulations: Sustainable Solutions for the Future
- With increasing environmental concerns, the electronics industry is pivoting towards eco-friendly formulations.
- Bio-based and recyclable materials are incorporated into Non conductive coatings, reducing carbon footprint and minimizing environmental impact.
- Sustainable solutions align with corporate responsibility initiatives and resonate with environmentally-conscious consumers.
Challenges and Considerations
These coatings safeguard electronic components from environmental factors and ensure optimal performance. However, several challenges and considerations must be addressed when implementing Non conductive coatings in electronic applications.
Challenges and Considerations:
- Compatibility with Different Substrates:Non conductive coatings must be compatible with various substrates commonly used in electronics manufacturing, including metals, plastics, and ceramics. Ensuring compatibility minimizes the risk of delamination and provides long-term adhesion.
- Cost-Effectiveness and Scalability: Balancing cost-effectiveness with scalability is essential for widespread adoption. Manufacturers need coatings that are not only affordable but also scalable for mass production without compromising quality.
- Durability and Long-Term Performance:Non conductive coatings must withstand harsh environmental conditions, mechanical stress, and temperature variations while maintaining their electrical insulation properties over time. Ensuring durability is paramount for the longevity of electronic devices.
- Regulatory Compliance and Standards Adherence: In electronics manufacturing, meeting regulatory requirements and industry standards are non-negotiable. Non conductive coatings must comply with regulations like RoHS and adhere to industry standards to ensure product safety and reliability.
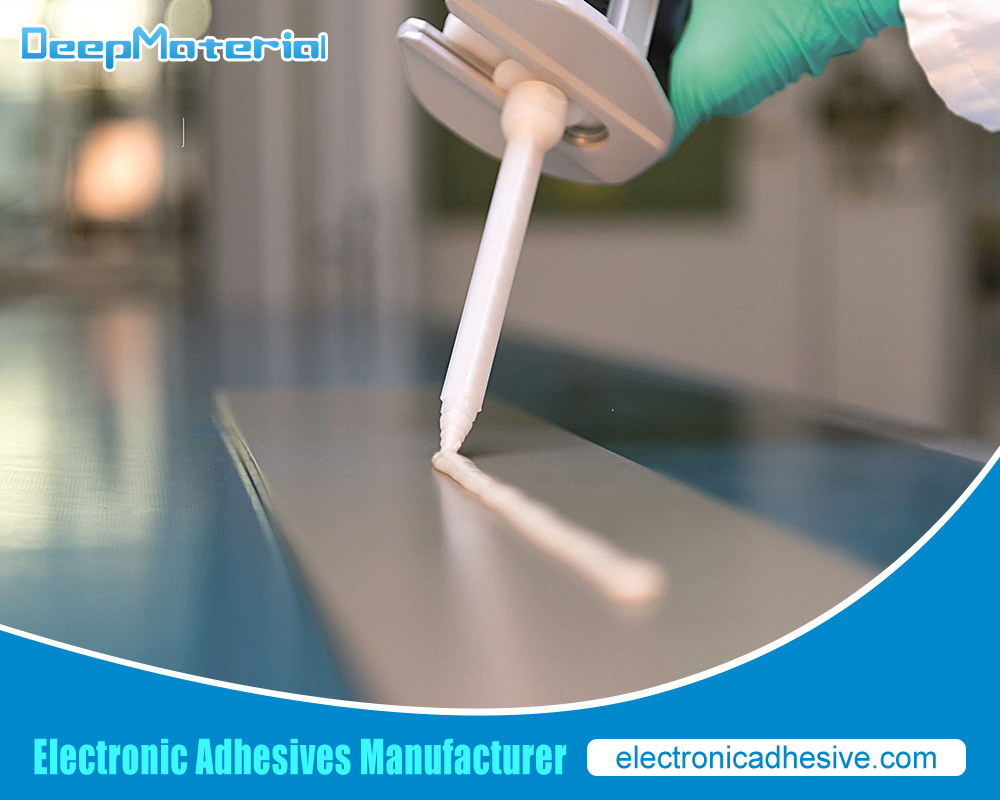
Conclusion
Non conductive coatings are crucial for ensuring the safety and reliability of electronic devices across various industries. From consumer electronics to critical aerospace and defense applications, these coatings shield against electrical hazards, corrosion, and environmental factors. As technology evolves, the demand for more advanced and versatile Non conductive coatings is expected to rise. Innovations in materials science, coupled with collaborative research efforts, promise to unlock new possibilities in electronic safety, paving the way for a future where devices are brighter and safer than ever.
For more about enhancing electronic safety: exploring non conductive coating for electronics, you can pay a visit to DeepMaterial at https://www.electronicadhesive.com/ for more info.