Electronics Encapsulation Epoxy: An In-Depth Guide
Electronics Encapsulation Epoxy: An In-Depth Guide
Electronics encapsulation epoxy plays a pivotal role in modern electronics, ensuring that sensitive components and circuits are protected from various environmental factors and physical stresses. This comprehensive guide will explore the critical aspects of electronics encapsulation epoxy, including its types, applications, benefits, and best practices for use.
1. Understanding Electronics Encapsulation Epoxy
Electronics encapsulation epoxy is a resin used to encase electronic components, circuits, and assemblies. The primary purpose of this epoxy is to safeguard electronic devices from environmental hazards such as moisture, dust, chemicals, and temperature extremes. Encapsulation also provides mechanical support and protection against physical damage during handling and operation.
Encapsulation epoxy is typically made from a blend of resins and hardeners that, when mixed, undergo a chemical reaction to form a durable and resilient solid. This solid material is then used to coat or encase electronic components, ensuring their longevity and reliability.
Critical Components of Encapsulation Epoxy:
- Resins:These are the main components of epoxy, providing the material’s structural properties. Common resins used in electronics encapsulation include epoxy, silicone, and polyurethane resins.
- Hardeners:Also known as curing agents, hardeners are added to resins to initiate the curing process. The choice of hardener affects the epoxy’s curing time, temperature resistance, and overall performance.
- Additives:Various additives, such as flame retardants, thermal conductivity agents, and colorants, may be included to enhance the epoxy’s properties.
2. Types of Electronics Encapsulation Epoxy
Electronics encapsulation epoxies come in several types, each designed to meet specific requirements and applications. Understanding these types helps in selecting the proper epoxy for particular needs.
**2.1. Standard Epoxy Resins
Standard epoxy resins are widely used due to their excellent mechanical properties, adhesion capabilities, and chemical resistance. They are commonly used in electronic components such as circuit boards, connectors, and chips.
Characteristics:
- High mechanical strength
- Good electrical insulation properties
- Excellent chemical resistance
- Relatively low thermal conductivity
Applications:
- Printed circuit boards (PCBs)
- Integrated circuits (ICs)
- Electrical connectors
**2.2. Silicone-Based Epoxies
Silicone-based epoxies offer superior flexibility and thermal stability compared to standard epoxy resins. They are ideal for applications requiring high-temperature resistance and flexibility.
Characteristics:
- High thermal stability
- Excellent flexibility and elongation
- Good electrical insulation
- Resistant to extreme temperatures and environmental conditions
Applications:
- High-temperature electronics
- Automotive electronics
- Aerospace components
**2.3. Polyurethane-Based Epoxies
Polyurethane-based epoxies are known for their toughness and abrasion resistance. They are often used in applications requiring impact resistance and durability.
Characteristics:
- High toughness and impact resistance
- Good abrasion resistance
- Excellent adhesion to various substrates
- Moderate thermal resistance
Applications:
- Electronic assemblies exposed to harsh environments
- Industrial Electronics
- Consumer electronics with high wear and tear
**2.4. Thermally Conductive Epoxies
Thermally conductive epoxies are designed to dissipate heat away from electronic components, enhancing their performance and reliability. These epoxies contain fillers that improve thermal conductivity without compromising electrical insulation properties.
Characteristics:
- High thermal conductivity
- Good electrical insulation
- Thermal management properties
Applications:
- Heat sinks
- Power Electronics
- LED assemblies
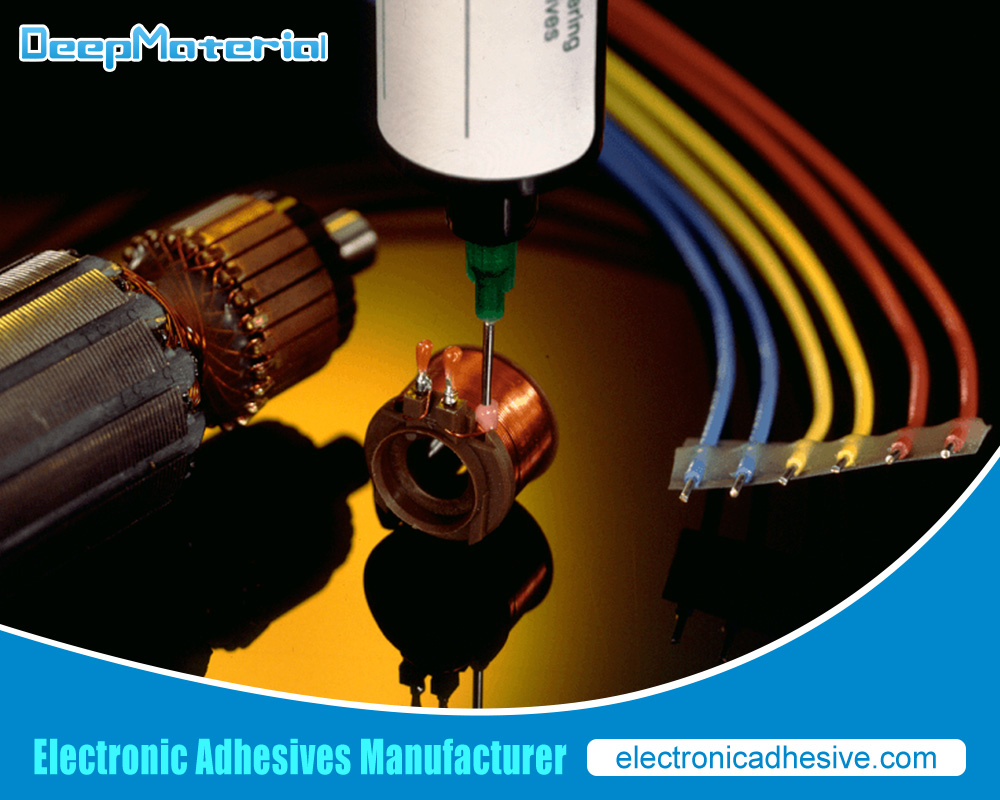
3. Benefits of Electronics Encapsulation Epoxy
Electronics encapsulation epoxy offers several benefits that contribute to the reliability and longevity of electronic devices. Here are some of the key advantages:
**3.1. Protection from Environmental Factors
Encapsulation epoxy protects against moisture, dust, chemicals, and other environmental contaminants. This protection is crucial for ensuring the functionality and durability of electronic components, particularly in harsh environments.
**3.2. Mechanical Support
Encapsulation epoxy adds mechanical strength to electronic assemblies, reducing the risk of physical damage during handling, transportation, and operation. It helps to secure delicate components and connections, preventing mechanical stress and vibration from causing damage.
**3.3. Electrical Insulation
The epoxy’s electrical insulation properties prevent short circuits and electrical failures by isolating conductive paths and components. This insulation ensures reliable performance and safety of electronic devices.
**3.4. Thermal Management
Thermally conductive epoxies help manage heat dissipation, preventing electronic components from overheating. This capability is essential for maintaining optimal performance and extending the lifespan of electronic devices.
**3.5. Enhanced Longevity
Encapsulation epoxy enhances the overall longevity and reliability of electronic components by providing protection against environmental and mechanical stresses. This leads to reduced maintenance and replacement costs.
4. Best Practices for Using Electronics Encapsulation Epoxy
Following best practices for application, curing, and handling is essential to achieve optimal results with electronics encapsulation epoxy. Here are some basic guidelines:
**4.1. Surface Preparation
Proper surface preparation is crucial for ensuring good adhesion of the epoxy to the electronic components. Surfaces should be cleaned of dust, grease, or moisture contaminants. Abrading the surface can also enhance adhesion.
**4.2. Mixing and Application
Follow the manufacturer’s instructions for mixing the epoxy resin and hardener. Accurate mixing ratios are essential for achieving the desired properties and performance. Apply the epoxy evenly to avoid voids or air bubbles, which can affect the encapsulation’s effectiveness.
**4.3. Curing Conditions
Curing conditions such as temperature and humidity can significantly impact the epoxy’s properties. Ensure the epoxy is cured under recommended conditions to achieve the best results. Some epoxies may require specific curing times or temperatures to reach full strength.
**4.4. Safety Precautions
Handle epoxy resins and hardeners with care, following safety guidelines provided by the manufacturer. Use appropriate personal protective equipment (PPE) such as gloves, goggles, and respirators to avoid exposure to harmful chemicals.
**4.5. Quality Control
Regularly inspect encapsulated components for defects or inconsistencies. Conduct quality control tests such as adhesion tests, electrical insulation resistance tests, and thermal conductivity measurements to ensure the epoxy meets performance standards.
5. Challenges and Considerations
While electronics encapsulation epoxy offers numerous benefits, there are also challenges and considerations to keep in mind:
**5.1. Cost
High-performance encapsulation epoxies can be expensive, particularly those with specialized properties such as high thermal conductivity or extreme temperature resistance. Budget constraints may limit the choice of epoxy in some applications.
**5.2. Compatibility
Ensure that the chosen epoxy is compatible with the materials used in the electronic components and assemblies. Incompatibility can lead to poor adhesion, chemical reactions, or degradation of the epoxy’s properties.
**5.3. Environmental Impact
The environmental impact of epoxy resins and hardeners should be considered, particularly regarding waste disposal and potential hazards. Opting for environmentally friendly formulations and following proper disposal practices can mitigate adverse effects.
**5.4. Aging and Degradation
Over time, encapsulation epoxy may experience aging and degradation due to exposure to environmental factors such as UV radiation, moisture, and temperature fluctuations. Selecting epoxy with appropriate longevity characteristics can help address this issue.
6. Future Trends and Innovations
The field of electronics encapsulation is continuously evolving, with ongoing research and development leading to innovations and improvements. Some emerging trends include:
**6.1. Advanced Materials
The development of advanced materials, such as nanocomposites and hybrid resins, is enhancing the performance of encapsulation epoxies. These materials offer improved properties such as higher thermal conductivity, better mechanical strength, and excellent environmental resistance.
**6.2. Eco-Friendly Formulations
A growing focus is on developing eco-friendly encapsulation epoxies with reduced environmental impact. These formulations aim to minimize the use of hazardous chemicals and improve the sustainability of electronic manufacturing processes.
**6.3. Smart Epoxies
Smart epoxies with integrated sensors or self-healing properties are being explored for applications in advanced electronics. These intelligent materials can provide real-time monitoring, damage detection, and self-repair capabilities.
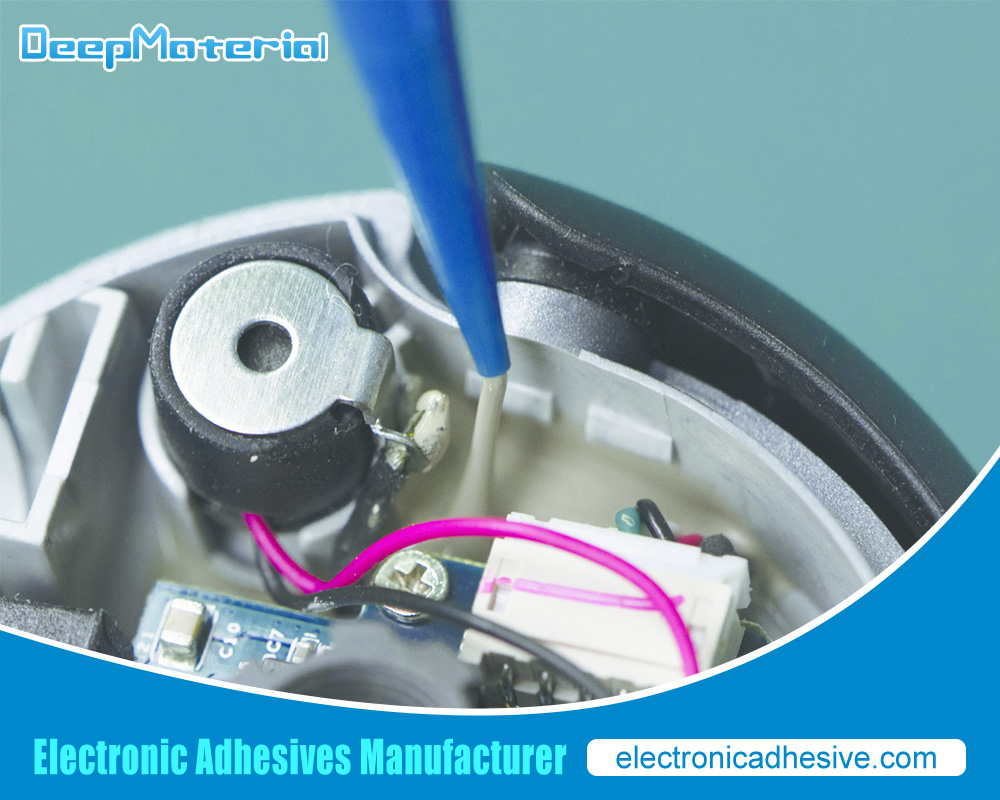
Conclusion
Electronics encapsulation epoxy is critical to ensuring electronic devices’ reliability, durability, and performance. By protecting environmental factors, mechanical stress, and electrical issues, encapsulation epoxy contributes significantly to the longevity and functionality of electronic components. Understanding the types, benefits, and best practices associated with encapsulation epoxy is essential for making informed choices and achieving optimal results in electronic applications. As technology advances, encapsulation epoxy innovations will likely drive further improvements in electronic manufacturing and performance.
For more about choosing the Top Electronics Encapsulation Epoxy: An In-Depth Guide, you can pay a visit to DeepMaterial at https://www.electronicadhesive.com/ for more info.