Conformal Coatings for Electronics Applications
Conformal Coatings for Electronics Applications
Conformal coatings protect electronic components from environmental damage and ensure their longevity and reliability. These protective coatings, applied in thin layers, conform to the contours of the electronic components and assemblies, providing a barrier against moisture, dust, chemicals, and temperature extremes. This article will delve into the types of conformal coatings, their applications, benefits, challenges, and future trends in the field.
Types of Conformal Coatings
Conformal coatings are available in various materials, each with unique properties and applications. The main types include acrylics, silicones, polyurethanes, epoxy resins, and perylene.
Acrylics
Acrylic conformal coatings are widely used for their ease of application, removal, and reworkability. They provide excellent protection against moisture and are resistant to various chemicals. However, acrylics have limited resistance to abrasion and high temperatures.
Silicones
Silicone coatings offer superior flexibility and thermal stability, making them suitable for high-temperature applications. They provide excellent moisture resistance and electrical insulation. Silicones are also known for their good adhesion properties. However, they can be more challenging to remove and rework than acrylics.
Polyurethanes
Polyurethane conformal coatings are known for their toughness and resistance to abrasion and chemicals. They provide reasonable protection against moisture and offer excellent electrical properties. Polyurethanes are often used in applications where durability and chemical resistance are critical. However, they can be more challenging to apply and remove than other types.
Epoxy Resins
Epoxy conformal coatings are highly durable and offer excellent chemical and moisture resistance. They provide strong adhesion to various surfaces and are often used in harsh environments. However, epoxies are less flexible and can become brittle over time, which may lead to cracking under thermal or mechanical stress.
Parylene
Parylene coatings are applied through vapor deposition, resulting in a uniform and pinhole-free coating. They provide excellent protection against moisture, chemicals, and temperature extremes. Parylene coatings have outstanding electrical insulation properties and are highly resistant to abrasion. However, the application process is more complex and expensive than that of other conformal coating types.
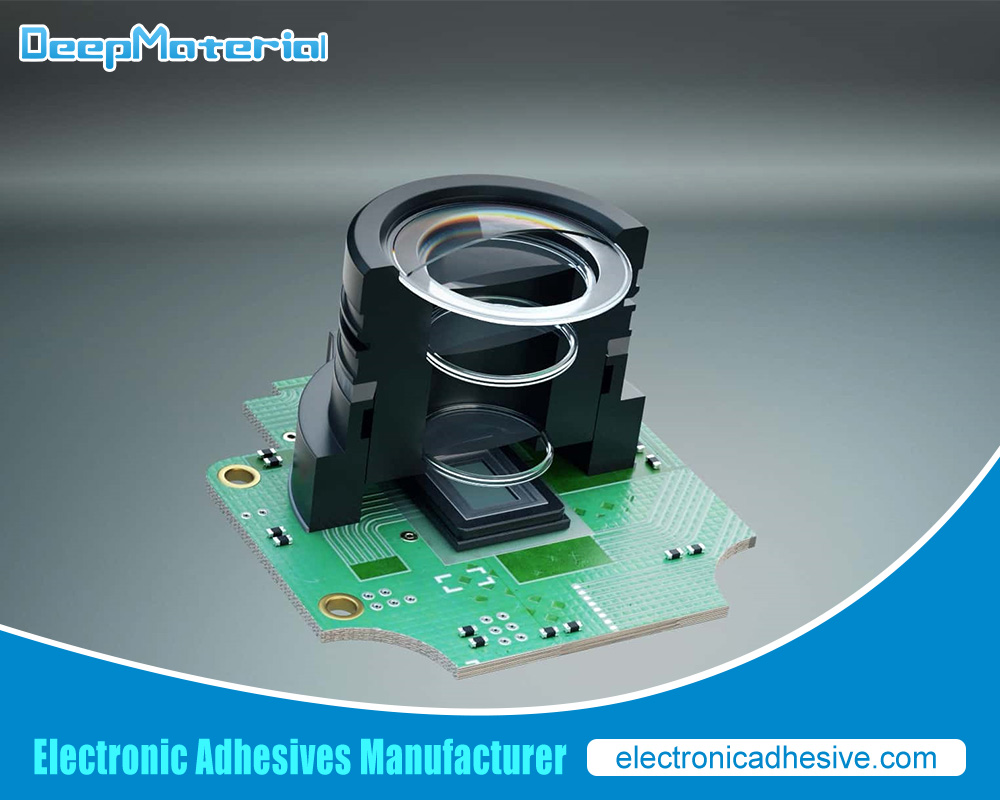
Applications of Conformal Coatings
Conformal coatings are used in various industries and applications to protect electronic components and assemblies from environmental factors. Some of the critical applications include:
Automotive Electronics
Electronic components are exposed to harsh environments in the automotive industry, including temperature fluctuations, moisture, dust, and chemicals. Conformal coatings protect electronic control units (ECUs), sensors, and other critical components to ensure reliable operation and longevity.
Aerospace and Defense
Aerospace and defense applications require high reliability and performance under extreme conditions. Conformal coatings protect avionics, communication systems, and other electronic components from moisture, temperature extremes, and corrosive environments.
Consumer Electronics
Conformal coatings are used in consumer electronics to protect printed circuit boards (PCBs) and other components from moisture, dust, and contaminants. This helps enhance the durability and reliability of devices such as smartphones, tablets, and wearable electronics.
Medical Devices
Medical devices often require protection from moisture and contaminants to ensure their proper functioning and longevity. Conformal coatings protect electronic components in medical devices such as pacemakers, hearing aids, and diagnostic equipment.
Industrial Electronics
Industrial electronics are exposed to harsh environments, including dust, moisture, chemicals, and temperature extremes. Conformal coatings protect sensors, control systems, and other electronic components in industrial applications, ensuring reliable operation and minimizing downtime.
Benefits of Conformal Coatings
Conformal coatings offer several benefits, making them essential to electronic component protection. Some of the key benefits include:
Moisture and Chemical Protection
Conformal coatings provide a barrier against moisture, preventing corrosion and short circuits. They also protect electronic components from chemicals and contaminants that could cause damage and reduce reliability.
Electrical Insulation
Conformal coatings offer excellent electrical insulation properties, preventing electrical shorts and ensuring the reliable operation of electronic components. This is particularly important in high-voltage applications and densely packed PCBs.
Thermal Stability
Many conformal coatings, such as silicones and perylene, offer excellent thermal stability, protecting electronic components from temperature extremes. This is critical in applications where temperature fluctuations are typical.
Mechanical Protection
Conformal coatings provide mechanical protection against abrasion, vibration, and impact. This helps enhance electronic components’ durability and reliability, especially in harsh environments.
Flexibility and Adhesion
Conformal coatings are designed to be flexible, allowing them to conform to the contours of electronic components and assemblies. They also offer good adhesion properties, ensuring a reliable protective barrier.
Challenges and Considerations
While conformal coatings offer numerous benefits, there are challenges and considerations to consider when selecting and applying these coatings.
Application Process
The application process for conformal coatings can be complex and requires specialized equipment and expertise. Depending on the type of coating and the specific application, different methods, such as brushing, spraying, dipping, and vapor deposition, may be used. Ensuring uniform coverage and avoiding issues such as bubbles, voids, and pinholes is critical for adequate protection.
Removal and Rework
Some conformal coatings, such as silicones and polyurethanes, can be challenging to remove and rework. This can complicate repair and maintenance processes, particularly in applications where components may need to be replaced or updated.
Environmental and Health Considerations
Certain solvents and chemicals used in the application and removal of conformal coatings can pose environmental and health risks. Proper handling, ventilation, and disposal procedures must be followed to minimize these risks.
Cost
The cost of conformal coatings can vary widely depending on the type of coating and the application process. While some coatings, such as acrylics, are relatively inexpensive, others, such as perylene, can be more costly due to the specialized equipment and processes required.
Compatibility and Performance
Selecting the suitable conformal coating for a specific application requires careful consideration of factors such as compatibility with the substrate, environmental conditions, and performance requirements. Thorough testing and evaluation are essential to ensure optimal protection and performance.
Future Trends in Conformal Coatings
The field of conformal coatings is continuously evolving, driven by advancements in materials science, application techniques, and industry demands. Some of the emerging trends and future directions in conformal coatings include:
Advanced Materials
Researchers are exploring new materials and formulations to enhance the properties and performance of conformal coatings. This includes the development of nanocoatings, which offer superior protection and can be applied in ultra-thin layers. Advanced materials with improved thermal stability, chemical resistance, and mechanical properties are also being investigated.
Smart Coatings
Innovative conformal coatings responding to environmental changes or external stimuli are an active research area. These coatings may incorporate self-healing properties, where the coating can repair itself in response to damage, or sensors that can monitor and report on the condition of the coating and the underlying components.
Environmentally Friendly Coatings
There is a growing emphasis on developing environmentally friendly conformal coatings that reduce the use of hazardous solvents and chemicals. Water-based and solvent-free coatings are gaining popularity as they reduce environmental impact and improve worker safety.
Automation and Precision Application
Advancements in automation and precision application techniques are improving the efficiency and accuracy of conformal coating processes. Robotic systems and automated dispensing equipment can ensure uniform coverage and reduce the risk of defects, leading to higher quality and more reliable coatings.
Enhanced Testing and Inspection
Innovations in testing and inspection methods are helping to ensure the quality and performance of conformal coatings. Non-destructive testing techniques like X-ray and optical inspection can detect defects and provide uniform coverage without damaging the coated components.
Integration with Additive Manufacturing
An emerging trend is the integration of conformal coatings with additive manufacturing (3D printing) processes. This allows for the direct application of conformal coatings during the manufacturing process, enhancing the protection and performance of complex and custom-designed electronic components.
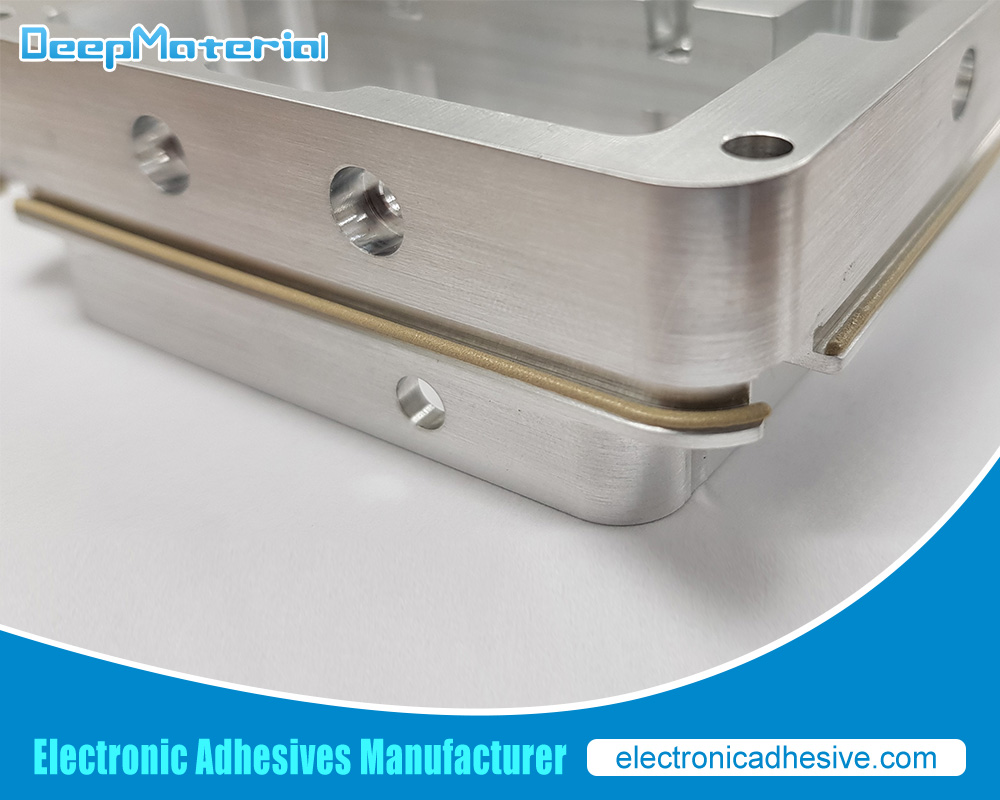
Conclusion
Conformal coatings protect electronic components and assemblies from environmental factors, ensuring their reliability and longevity. With various materials and application techniques available, selecting the appropriate conformal coating for each application is essential. As technology advances, the development of new materials, innovative coatings, and automated application processes will continue to drive innovation in the field, providing enhanced protection and performance for electronic components across various industries.
For more about choosing the top conformal coatings for electronics applications, you can pay a visit to DeepMaterial at https://www.electronicadhesive.com/ for more info.